Adhesive Properties of PUD Made With 3-Methy-1,5-Pentanediol and Dicarboxylic Acid with Aromatic Rings
MarekUsz / Getty Images Plus via Getty Images
Adhesive Properties of PUD Made With 3-Methy-1,5-Pentanediol and Dicarboxylic Acid with Aromatic Rings
Share-ify, the industry-leading, secure, private network for trading partners and customers to share business information, has announced its 2023 results with a 35 percent increase in sales year over year and a forecast that 2024 will be even better. Photo courtesy of Ales-A/iStock / Getty Images Plus via Getty Images.
By combining MPD with highly cohesive carboxylic acids, it is possible to get a PUD with a balance of adhesion, durability, and handling.
Share-ify Launches Into 2024 after Stellar 2023 Results
By Shun Okura, Sales Engineer & Researcher for Advanced Chemicals at Kuraray America, Inc.; Hoan Tran, Market Manager for Elastomers and Advanced Chemicals at Kuraray America, Inc., Houston, Texas
Due to the increasing demand to reduce VOC emissions, many solvent-based polyurethanes have been replaced by water-based polyurethanes. This presentation reports the unique properties of 3-methyl-1,5-pentanediol (MPD)-based polyols and polyurethane dispersions (PUDs) made from these polyols.
In general, PUDs introduce hydrophilic groups such as carboxylic acids and sulfonic acids into the primary structure to disperse polyurethane in water. However, some problems may arise such as low hydrolysis resistance due to the hydrophilic group. In addition, since polyurethane forms micelles, molecular entanglement does not occur easily in the coating film formation process, resulting in low bond strength. To address these problems with a polyol structure, it is necessary to incorporate a high-cohesion structure such as an aromatic ring. Considering these factors, we hypothesize that it is possible to simultaneously improve the bond strength by increasing the cohesion between molecules and hydrolysis resistance by inhibiting water intrusion with short intermolecular distance. On the other hand, the introduction of a high-cohesion structure to an excessive degree leads to high viscosity and high melting point, making it difficult to synthesize polyols. In order to solve these problems at once, it is necessary to control the degree of cohesion. In this paper, we propose a polyol that combines MPD and aromatic dicarboxylic acid, which take these issues into account. Since MPD has a methyl branch at the center position and a main chain of a certain length, we hypothesize that by introducing it into a polyol, it would be possible to achieve both high cohesion from the aromatic ring and low viscosity from MPD.
Although it is possible to synthesize a polyol with reference diol and terephthalic acid (TPA), it is not possible to synthesize PUD due to high viscosity and melting point. On the other hand, polyols with MPD and TPA are liquid at 80 °C, and PUD could also be synthesized.
The PUD synthesized by polyol made from MPD and TPA is tenacious, with high adhesion to various substrates and has high solvent durability when made into PUD. Thus, it can be applied as an adhesive for a broad range of materials including a variety of metals and plastics. Comparing the PUD adhesives made from conventional polyol to that which are made from MPD and TPA, it was found that the MPD polyol system exhibited higher adhesion than the reference polyol and maintained strength even under high temperature and high humidity.
However, the polyol from MPD and TPA also has a high viscosity, which may affect the ease of handling. Therefore, we examined the viscosity of polyols with reduced molecular weight and polyols whose crystallinity was reduced by switching TPA to isophthalic acid (IPA), and the physical properties of PUD using them. Based on this study, we found that PUD with a better balance between handling and adhesive properties can be achieved.
In conclusion, we found that it is possible to have a PUD that is a good in balance of adhesion, durability, and handling by combining MPD with highly cohesive carboxylic acids.
Introduction
The majority of current polyurethanes are solvent based because they have very good physical properties. However, solvent-based polyurethanes have high VOCs and pose some negative effects on both the environment and human health. For these reasons, we see the increase in regulations and trends towards more environmentally friendly and safe water-based polyurethanes.
In general, polyurethane adhesives demonstrate good chemical resistance, elasticity, and durability depending on the combination of raw materials. Polyurethane adhesives can also be used to bond various types of substrates such as wood, textile, plastic and metal. However, water-based adhesives have some limitations such as low adhesion and durability compared to solvent-based adhesives.
PUDs have two issues. First, the emulsifier for forming micelles makes hydrolysis resistance low due to the structure including an ionic group, which is highly hydrophilic. Secondly, PUDs lack strength. There are three steps to form PUD coating films. The first step is evaporation of water. In the next step, water evaporates further and molecules get closer to each other. In the last step, molecules are fused to each other by heat, and molecular entanglement is more difficult compared to a solvent-type PU. As a result, PUD film has low strength. For many adhesive applications, high adhesion strength and hydrolysis resistance are critical performance requirements. For this purpose, it is necessary to include a structure with high cohesion structure, such as an aromatic ring or ester group, in the polyol. However, an increase in the ester group generally makes hydrolysis resistance lower. Whereas an increase in the aromatic rings will result in high strength and hydrolysis resistance. Furthermore, introducing aromatic rings will increase viscosity and raise the melting point. To address these issues, we propose the use of MPD to offset the negative effects of the aromatic rings. We believe that the branched structure of MPD can reduce viscosity and lower melting point. And by incorporating MPD into the polyol structure, the amount of aromatic ring can be further increased while balancing the required physical properties of polyols and polyurethanes.
Measurement of Properties
Tensile test
Film thickness: 40µm
Drying conditions: rt 2h, 100 °C 16 h
Method: ISO 37
Specimen size: Type.5 Dumbbell test piece
Tensile speed: 50mm/min
Tensile shearing test
Coating area: 12mm×25mm
Adhesive layer thickness: 0.2mm
Drying conditions: rt 2h, 100 100 °C 12 h
Method: ISO 4587
Tensile speed: 2mm/min
Hydrolysis resistance test
Temperature and Humidity: 85 °C 85%RH
Viscosity
Rotational viscometer
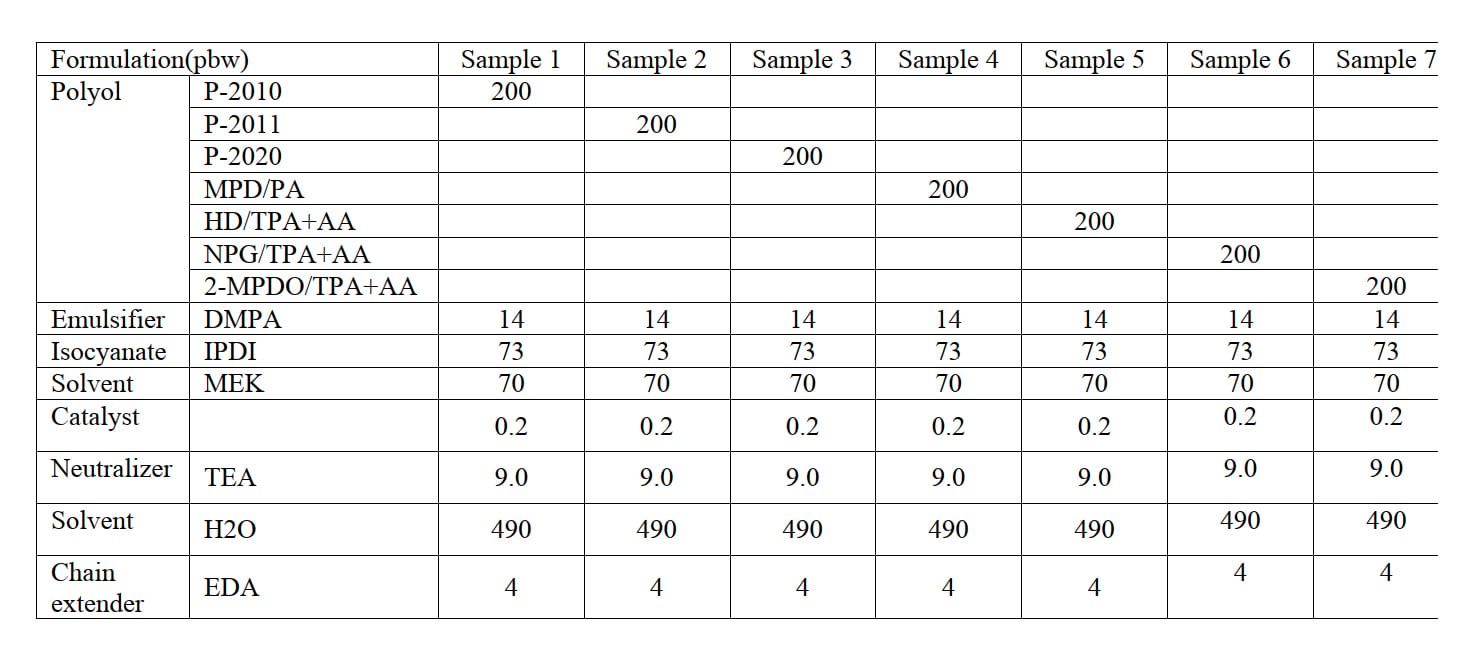
Table 2: Formulation of PUD using polyols with MW 2000 (Unit: gram).
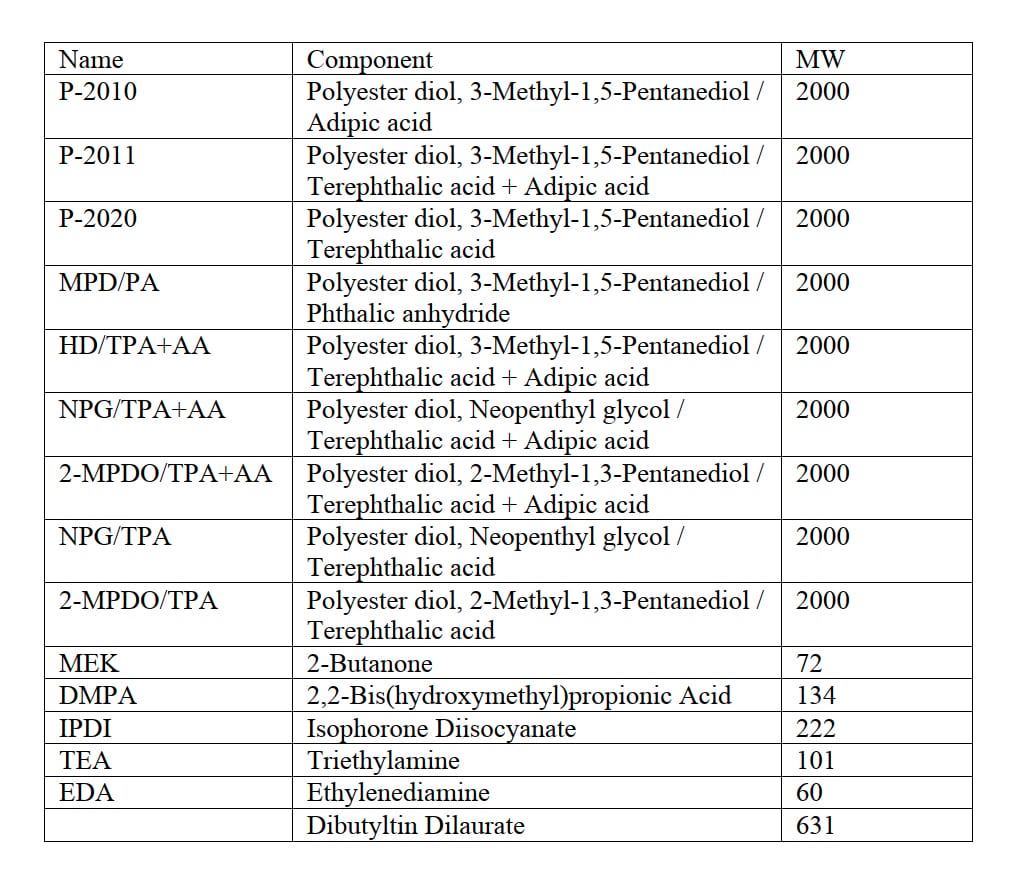
Table 1: Raw materials.
Experimental
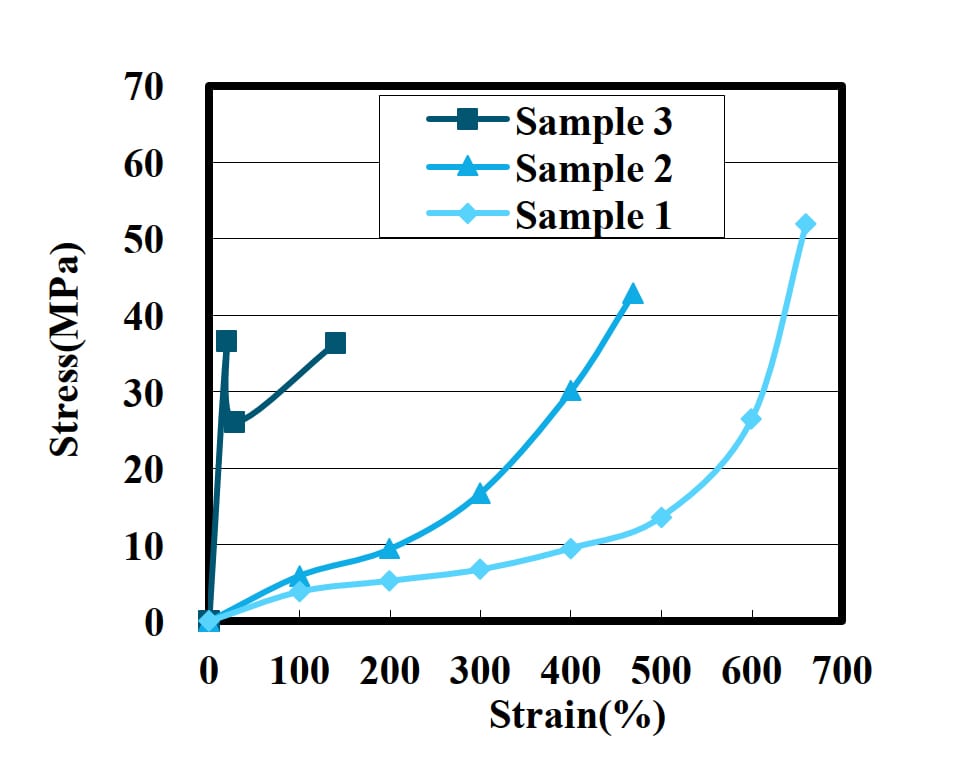
Figure 1: Tensile strength of PUD film with terephthalic acid.
Results and Discussion
1.Tensile property
1-1. The effect of content of terephthalic acid
The results of tensile strength are shown in Figure 1. The initial strength of sample 2 at 100% modulus is highest. The initial strength depends on the amount of terephthalic acid.
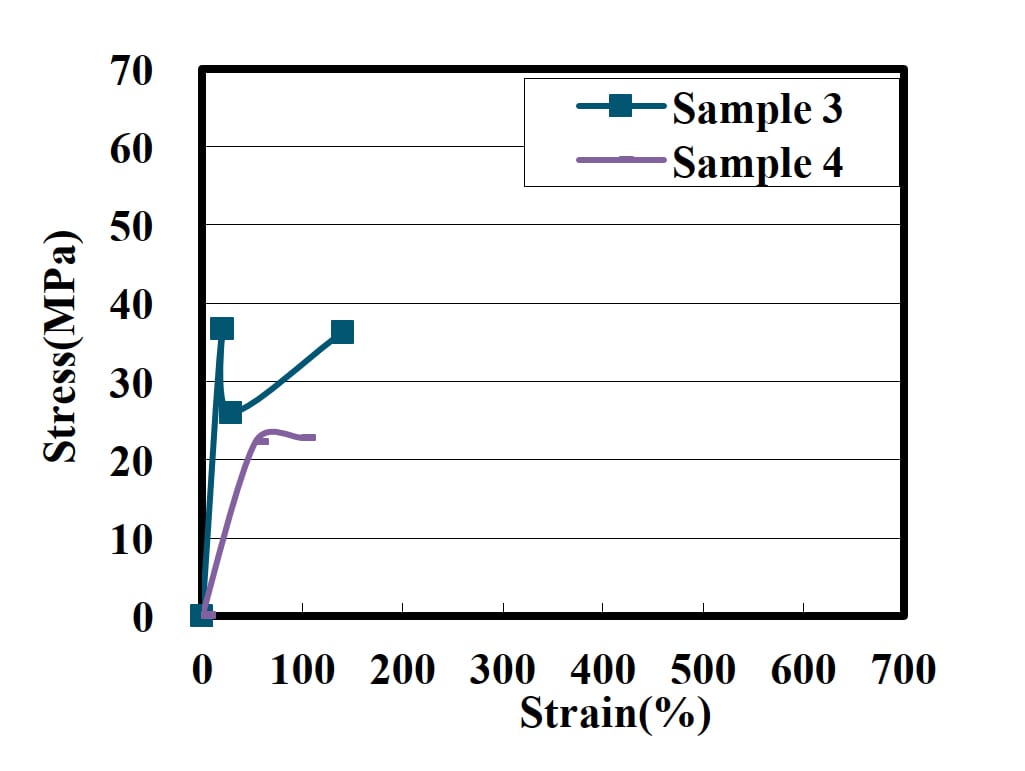
Figure 2: Tensile strength of PUD film with phthalic acid.
1-2. The effect of position of ester groups in phthalic acid
We examined the effect of the position of the ester group on the aromatic ring on the strength (Figure 2). The initial strength of Sample 3 is higher than Sample 4. In the case of the para position, the polyurethane molecule is considered to have a relatively linear structure. On the other hand, ester groups in the ortho position make the polyurethane structure helix or bent. Therefore, terephthalic acid can easily form a cohesion structure of the aromatic ring.
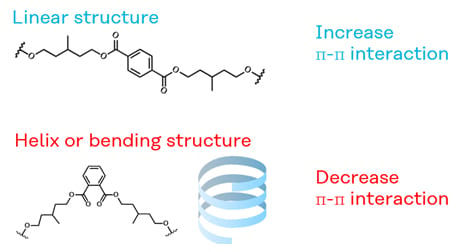
1-3. The effect of diol structure
In case of using TPA and AA, Sample 6 has the highest strength (Figure 3). Diols with a shorter main chain and suppressed molecular motility have higher strength. In NPG, the rotation of the molecular chain is further suppressed by two methyl branches.

Figure 3: Tensile strength of PUD film with some diols.
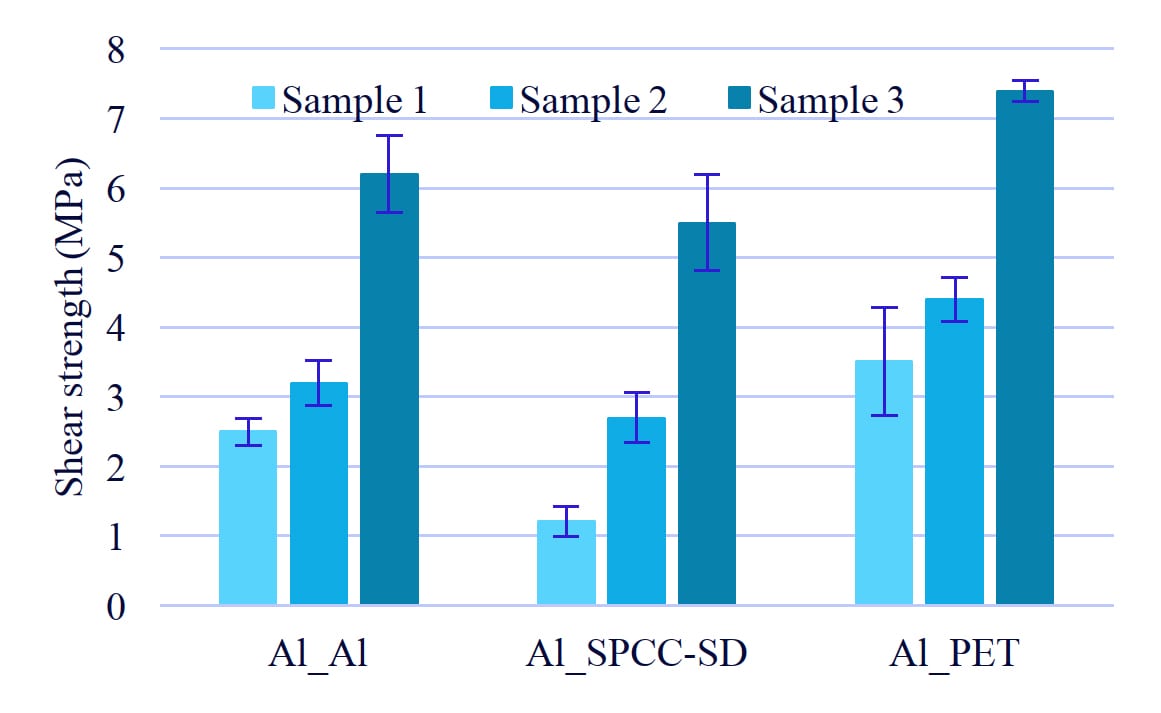
Figure 4: Tensile shearing test of PUD with terephthalic acid.
2. Tensile shearing test
2-1. The effect of content of terephthalic acid
The results of tensile shearing test are shown in Figure 4. Sample 3 has the highest adhesion of any substrate. The adhesion strength is dependent on the amount of aromatic rings.
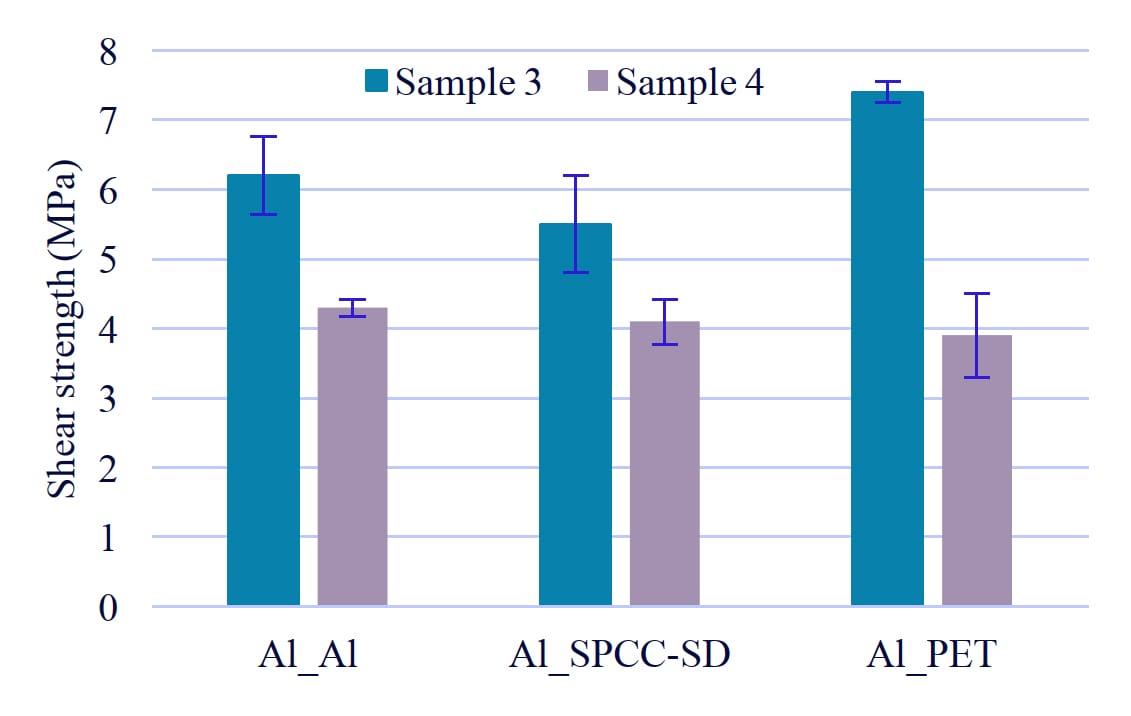
Figure 5: Tensile shearing test of PUD with phthalic acid.
2-2. The effect of position of ester groups in phthalic acid
Similar to tensile strength, the adhesive strength was lower in the para position (Figure 5, Sample 3) compared to the ortho position (Sample 4). From these results, the adhesive strength is also affected by the steric influence of polyurethane molecules.
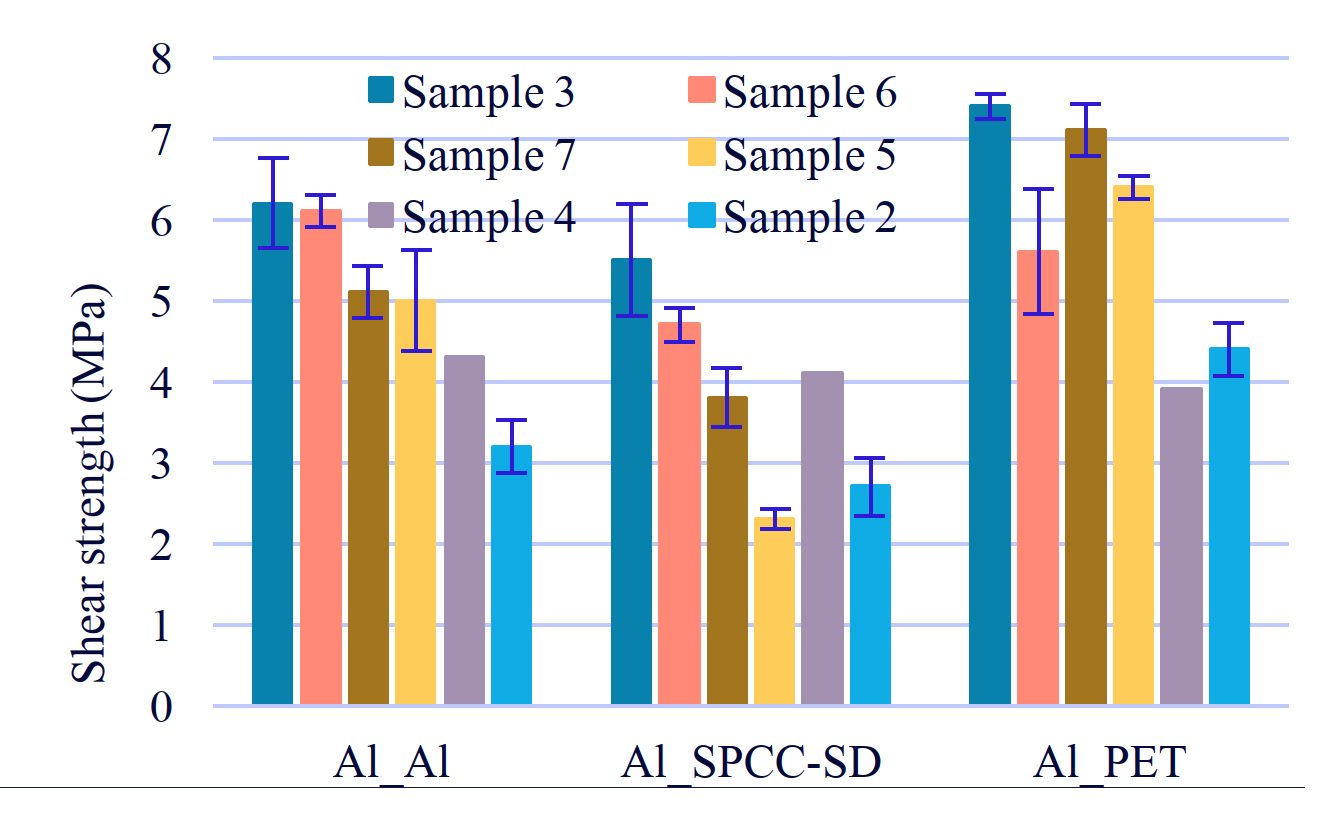
Figure 6: Tensile shearing test of PUD with some diols.
2-3. The effect of differences in the structure of diol
Sample3 showed high strength not only in adhesion between aluminum, but also in adhesion between aluminum and other substrates (Figure 6). Sample 4 had the same adhesive strength as Sample 5 and Sample 7.
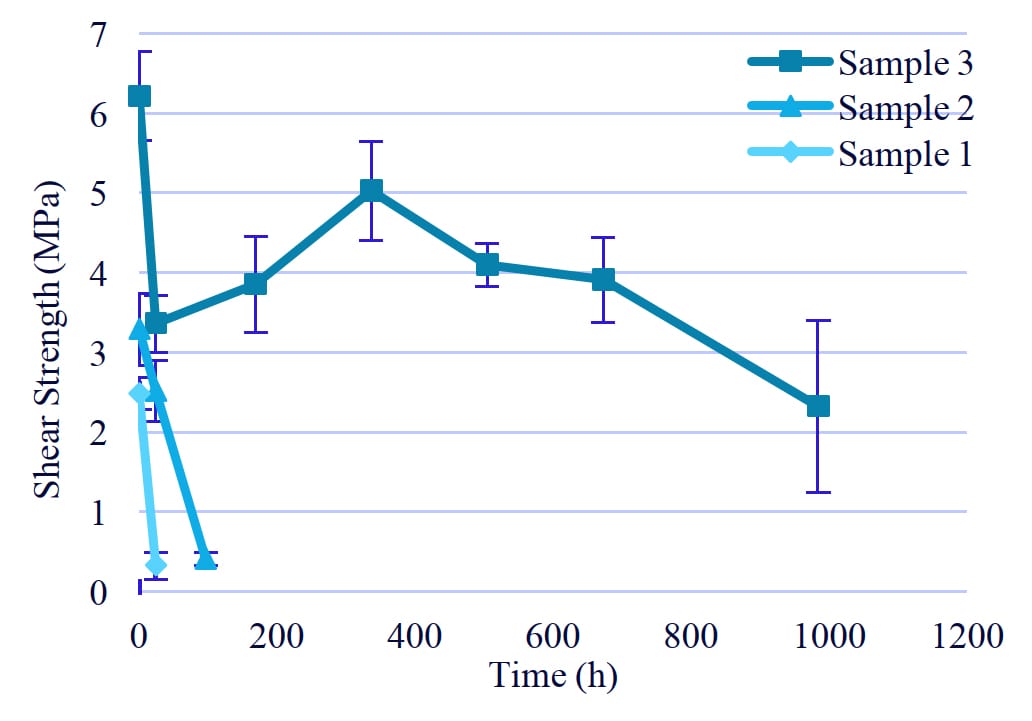
Figure 7: Hydrolysis resistance of PUD with terephthalic acid.
3. Hydrolysis resistance test
3-1. The effect of content of terephthalic acid
For hydrolysis resistance, the aluminum substrates bonded by PUD were exposed to 85 ℃ and 85% humidity for up to 1000 hours (Figure 7). Sample 3 had higher hydrolysis resistance than Sample 1 and Sample 2. From these results, we hypothesize that water ingress is inhibited by the steric hindrance by methyl branch and the π-π interaction of aromatic rings.
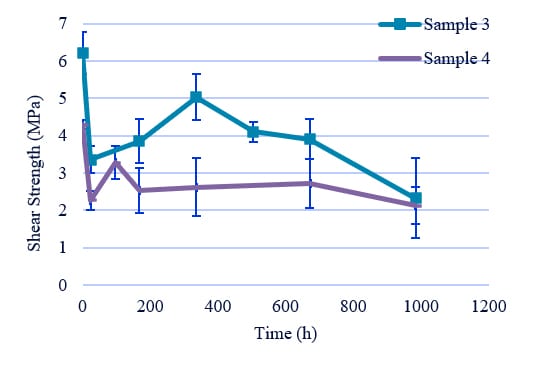
Figure 8: Hydrolysis resistance of PUD with phthalic acid.
3-2. The effect of position of ester groups in phthalic acid
Sample 3 was found to have the same hydrolysis resistance as Sample 4 (Figure 8). These results are considered to be due to the steric hindrance caused by the folding of the polyurethane structure derived from ortho-phthalic acid and the interaction of the aromatic rings, which inhibits the ingress of water. On the other hand, the introduction of phthalic acid into the polyol structure was found to lower the strength but not the hydrolysis resistance compared to the introduction of terephthalic acid.
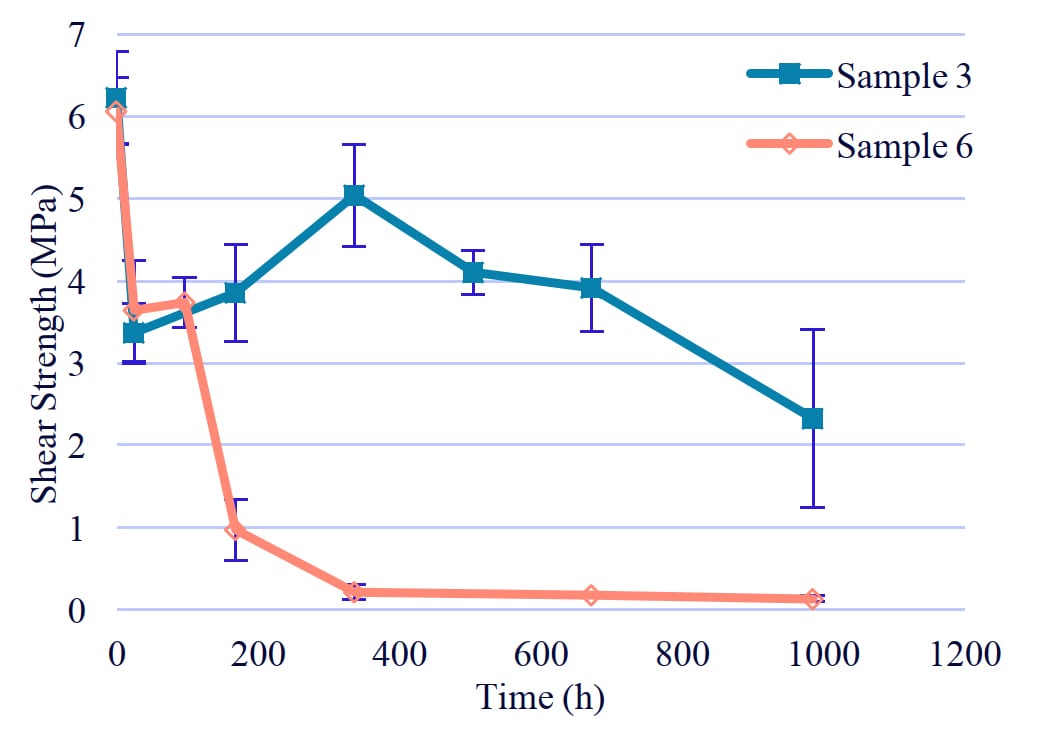
Figure 9: Hydrolysis resistance of PUD with terephthalic acid.
3-3. The effect of diol structure
Sample 3 and Sample 6 had similar adhesion strength, but Sample 3 had better hydrolysis resistance (Figure 9). One significant observation was that there was little change in the molecular weight of the PUD, which consists of Sample 3, while MW of that with Sample 6 dropped significantly. The aromatic ring contents of Sample 3 was higher than that of Sample 6. We thought that it was difficult for water to penetrate between molecules by increasing aromatic rings. Samples 2, 5, and 7 copolymerized with adipic acid had low hydrolysis resistance, as Sample 6.
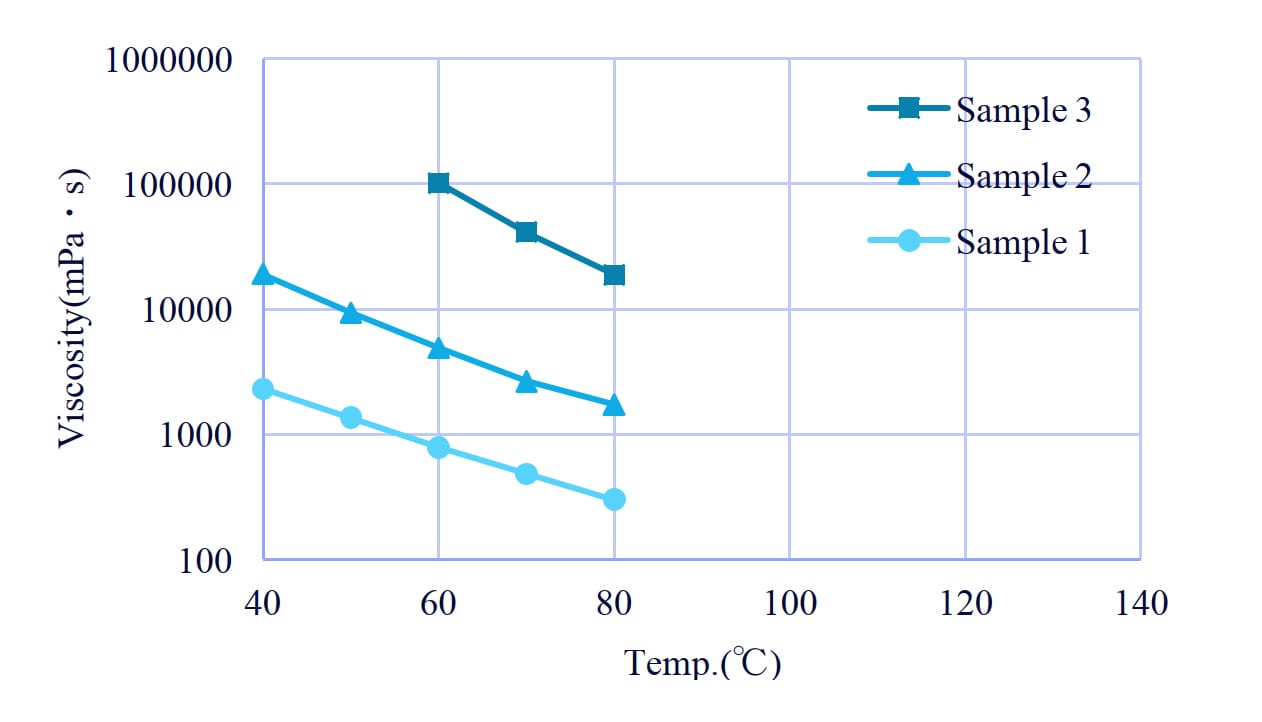
Figure 1: Viscosity of polyol with terephthalic acid.
4. Viscosity of polyol
4-1. The effect of content of terephthalic acid
MPD/TPA has the highest viscosity; the higher the TPA content, the higher the viscosity tended to be (Figure 10). The viscosity also increased with the introduction of a highly cohesive structure.

Figure 11: Viscosity of polyol with terephthalic acid.
3-2. The effect of types of diols and the position of ester groups in phthalic acid
MPD/TPA had the lowest viscosity among the various diol/terephthalic acid combinations (Figure 11). We think that the viscosity of MPO increased due to its short main chain and that of NPG due to the inhibition of rotation of the main chain by methyl branching.
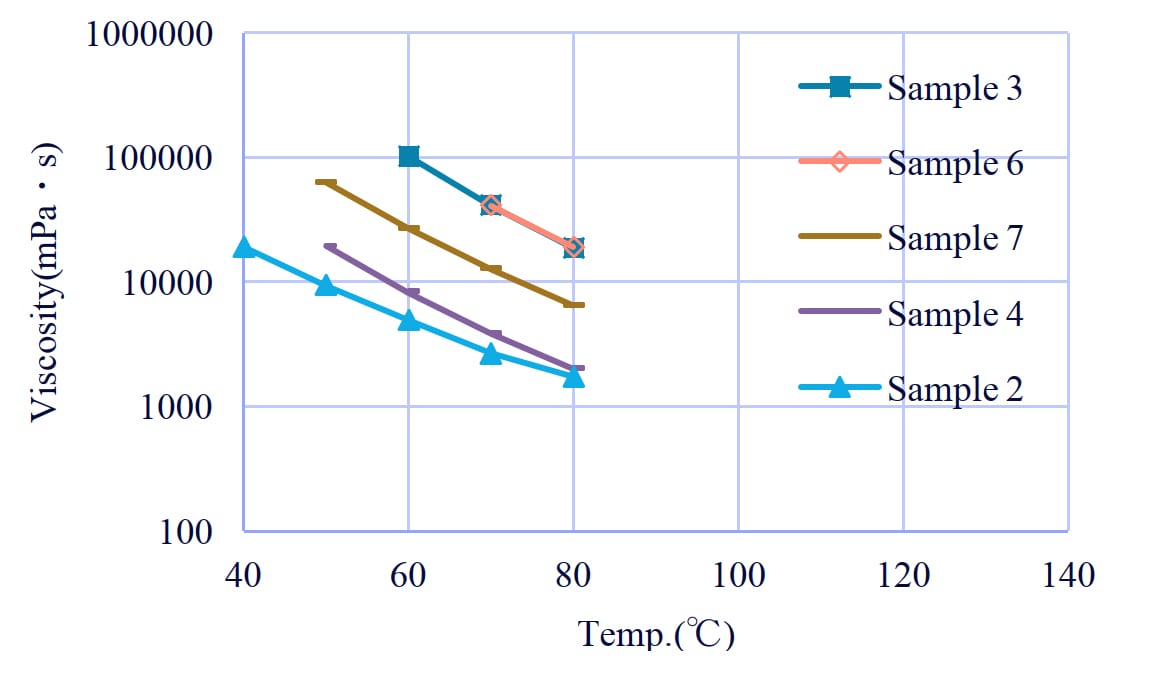
Figure 12: Viscosity of polyol with phthalic acid.
3-2. The effect of types of diols and the position of ester groups in phthalic acid
Surprisingly, the viscosity of MPD/PA was lower than polyols composed of 2-MPDO or NPG, TPA and AA (Figure 12). This is thought to be due to the fact that the bending structure of phthalic anhydride prevents intermolecular entanglement and the steric hindrance effect of the methyl branching of MPD causing an extreme decrease in viscosity.
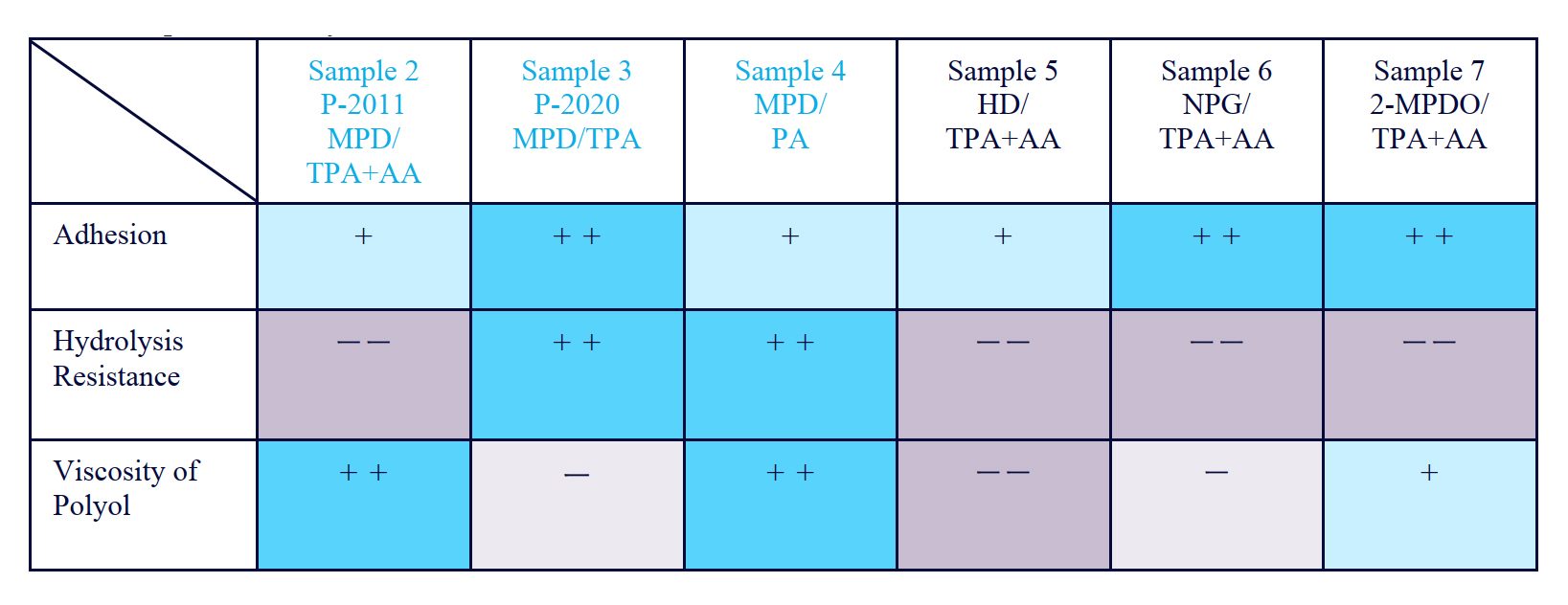
Table 3: Using MPD and phthalic anhydride achieves a balance of adhesive strength, hydrolysis resistance, and viscosity.
Conclusion
Polyol synthesized with MPD and terephthalic acid only has excellent adhesive strength and hydrolysis resistance. However, viscosity was still relatively high, even with some reduction of viscosity by MPD. When a grade blended with terephthalic acid and adipic acid was used, viscosity was reduced, but hydrolysis resistance was significantly reduced. It was confirmed that a balance of adhesive strength, hydrolysis resistance, and viscosity can be achieved by using MPD and phthalic anhydride.
"Adhesive Properties of PUD Made With 3-Methy-1,5-Pentanediol and Dicarboxylic Acid with Aromatic Rings " 2024 Polyurethanes Technical Conference September 30 to October 2, 2024, Atlanta, Georgia, USA. Published with permission of CPI, Center for the Polyurethanes Industry, Washington, DC.