Andrei Nasonov / iStock / Getty Images Plus
Comparison of Low-Tg Acrylic Latex Binders to Increase Durability of Elastomeric Liquid Roofing Membranes
Share-ify, the industry-leading, secure, private network for trading partners and customers to share business information, has announced its 2023 results with a 35 percent increase in sales year over year and a forecast that 2024 will be even better. Photo courtesy of Ales-A/iStock / Getty Images Plus via Getty Images.
to Increase Durability of Elastomeric Liquid Roofing Membranes
Share-ify Launches Into 2024 after Stellar 2023 Results
By Artur Palasz, Ph.D., Spektrochem, Poland
Flat roofs are highly exposed to weather conditions and, over time, are subjected to factors that cause gradual aging and deterioration. Solar radiation, rain, temperature fluctuations, air pollution, snow and ice all contribute to the weathering of acrylic liquid elastomeric coatings applied to both new and renovated flat roofs. Rainwater can lead to surfactant migration, softening the coatings and causing blistering, particularly in areas where water stagnates. In heavy-duty environments, acid rain may further exacerbate damage through acid etching. Solar radiation, combined with fluctuating temperatures, humidity, snow and ice, creates stresses that, over prolonged exposure, may result in cracking and a loss of elasticity. As the binder in a coating ages, chalking can also occur. Additionally, biological pollutants, increased porosity, and a tendency to trap dirt heighten the risk of mold growth on these roofs.
Ensuring the quality and durability of elastomeric liquid acrylic roof membranes presents a significant challenge for the R&D departments of raw material producers and manufacturers. External laboratories, which assist in testing raw materials and evaluating their performance in formulations, provide essential insights. Proper use of these materials in formulations simplifies their selection and integration into the final product. Performance tests of raw materials for elastomeric roof coatings, based on acrylic polymer latex dispersions, involve multistage laboratory processes that progressively help develop formulations with the properties needed to withstand the weathering challenges outlined above.
Developing a well-formulated roof coating is crucial not only for protecting the building from weathering but also for economic reasons. Roof renovations are costly, often requiring the dismantling of numerous components (e.g., air conditioning units, chimneys, ladders), and this work can typically only be done during limited weather windows. Furthermore, ensuring the quality and cleanliness of elastomeric roof coatings, especially those designed for cool-roof applications, adds complexity to the selection of raw materials and the formulation process.
Elastomeric Liquid Membranes
Liquid roofing membranes made from acrylic polymers can be defined in several ways. For this article, we will use the definition from ASTM D6083, which specifies that the product must be in liquid form for application to the roof surface by brushing, squeegeeing, rolling or spraying. The product should consist of a water-based acrylic latex elastomeric emulsion polymer, with added pigments and other additives to provide the necessary physical properties.1 Depending on the region, these coatings require different functional properties. Typically, they are white, waterproofing coatings designed to reflect sunlight and serve as cool-roof coatings. In most cases, they have a flat sheen; however, in some countries, market preferences or local regulations may require a slight gloss. In the EU, the parameter requirements are specified by ETAG guidelines for issuing European Technical Assessments. ASTM D6083, which outlines the requirements and test methods, is a crucial standard for formulating and evaluating raw materials during the selection process.
Polymer Latex Binders
The binder plays a crucial role in the elastomeric properties of liquid roof coatings. It is a polymer dispersion, similar to latex wall paints, but made with monomers that provide high, permanent flexibility with a low Tg value (glass transition temperature). These binders are typically pure acrylic dispersions or styrene-acrylic dispersions, the latter containing small amounts of styrene that significantly increase the Tg. In many cases, polyurethane dispersions (PUDs) are also used.
The long-term flexibility and tightness of the coating are key factors in selecting polymer dispersions. Flexibility is especially important at low temperatures, where the coating needs to remain deformable and resistant to thermal stress in winter and freezing conditions. While the binder is a major contributor to these properties, other formulation ingredients, such as HEUR thickeners, can significantly increase dirt pick-up.2
The binder in elastomeric liquid roofing membranes is also responsible for resistance to chalking, which occurs when the binder degrades due to sunlight exposure. Chalking causes a powdery residue to form on the coating, which initiates its erosion. This increases porosity, weakens waterproofing properties, reduces sunlight reflection and allows contaminants to accumulate, leading to potential dirt retention and mold growth.
Given the wide variety of polymer dispersions available for elastomeric liquid roof membranes, it is essential to choose a dispersion suited to the specific application. Some dispersions are ideal for use in colder environments, such as northern Europe, where flexibility at negative temperatures is critical. Others are better suited for hot climates, like Arizona, where resistance to chalking is the primary concern, and flexibility is less important.
Experimental
To present the differences among market polymer dispersions used in elastomeric liquid roof coatings formulations, nine polymer dispersions available in the North American and European markets—both styrene-acrylic and acrylic—were tested. The characteristics of these dispersions are presented in Table 1.
Polymer dispersions, characterized by technical data sheets (TDS), allow for the estimation of flexibility through Tg analysis. However, this only provides an initial estimation of flexibility, and it is impossible to predict how the polymer will behave after exposure to weather conditions. Similarly, resistance to chalking cannot be predicted based on very rough information about the surfactants used. Some polymer dispersions do not have this data provided by manufacturers.
For polymer comparisons, the starting formulation presented in Table 2 was prepared. Due to the varying solid content of the tested polymer dispersions, the amount of water in the formulation was adjusted to maintain a PVC (pigment volume concentration) of 44% for each dispersion, regardless of solid content. Samples were built based on each dispersion with varying solid content to always achieve the same PVC, by calculating the amount of polymer dispersion in the formulation based on its solid content. A simple formulation was used without focusing on special additives, allowing for an undisturbed evaluation of the polymer dispersions.
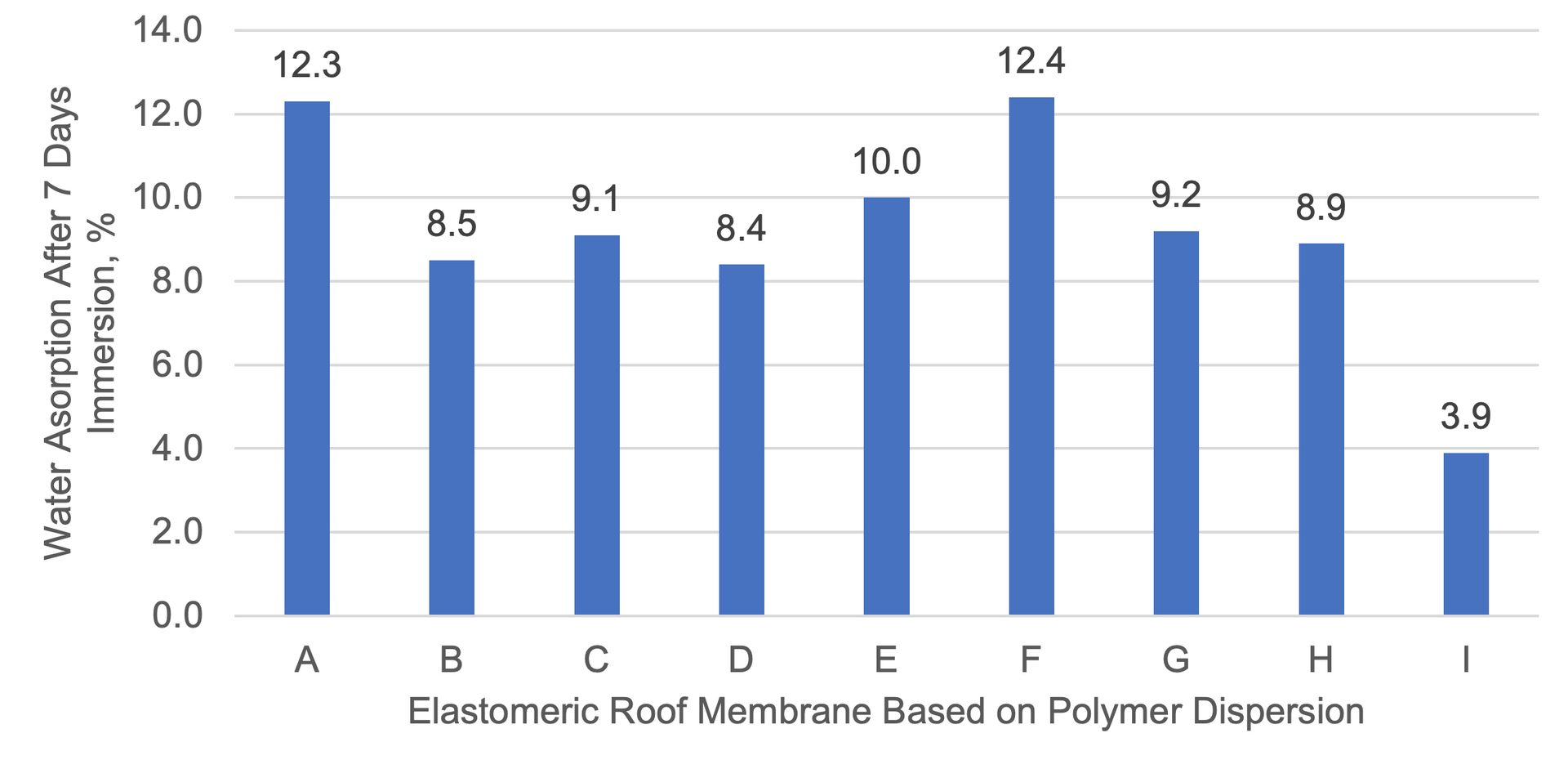
FIgure 1. Water absorption.
Water Absorption
Samples were prepared by drawdown on Leneta release paper, separated from the substrate after 7 days of conditioning at 23 °C ± 2 °C (73.5 °F ± 3.5 °F) and 50% ± 5% relative humidity. The coatings were weighed on an analytical balance and then immersed in demineralized water at a temperature of 23 °C to 25 °C (73.5 °F to 75 °F) and conductivity <5 µS/cm. After removal, the samples were weighed again, and the percentage weight gain was calculated. The results are shown in Figure 1.
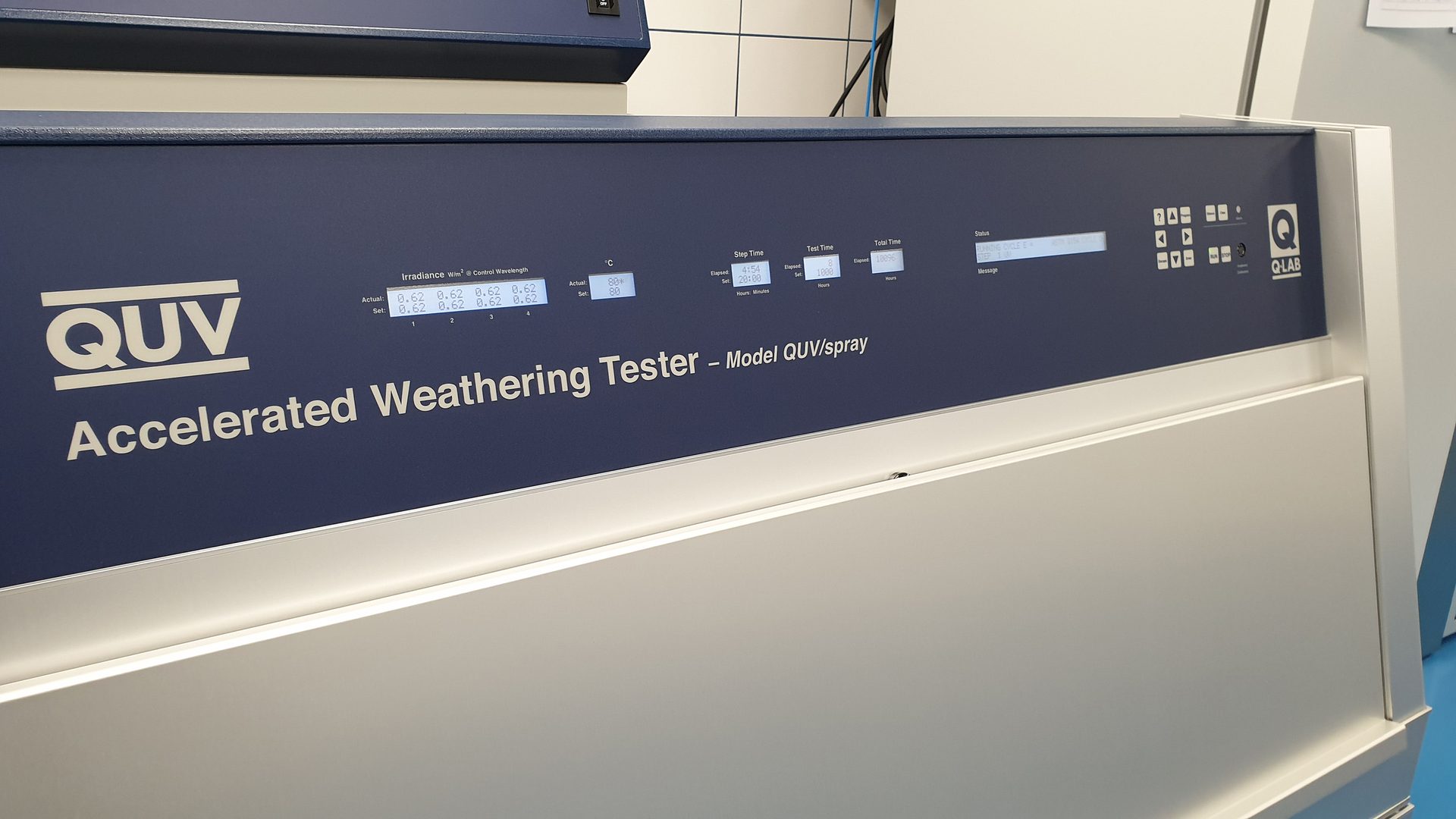
Figure 2. Q-UV chamber during a given test with the tested coatings.
The water absorption results show a variation between 8.4% and 12.4% after 7 days of immersion in water. However, one of the polymer dispersions (Dispersion I) exhibited a significantly lower water absorption of 3.9%. These results indicate that the differences in water absorption due to changing polymer dispersions can be significant. Thus, this parameter should be considered when selecting a binder for liquid acrylic roofing membranes.
Accelerated Artificial Weather Exposure
If polymer dispersions affect water absorption, they also significantly impact the resistance of coatings, which are subjected to atmospheric factors such as rainwater saturation and temperature fluctuations, along with destruction caused by solar radiation. It is well-known that atmospheric factors vary in different latitudes, as do the highest and lowest temperatures, which can cause stresses on coatings. In this study, exposure tests were conducted in a Q-UV chamber (Figure 2), with a cycle selected to simulate extremely aggressive UV radiation exposure. After a planned exposure period in the Q-UV chamber, tests were performed to check the flexibility of the coatings at negative temperatures and compare whether there was any loss of flexibility relative to pre-exposure tests.
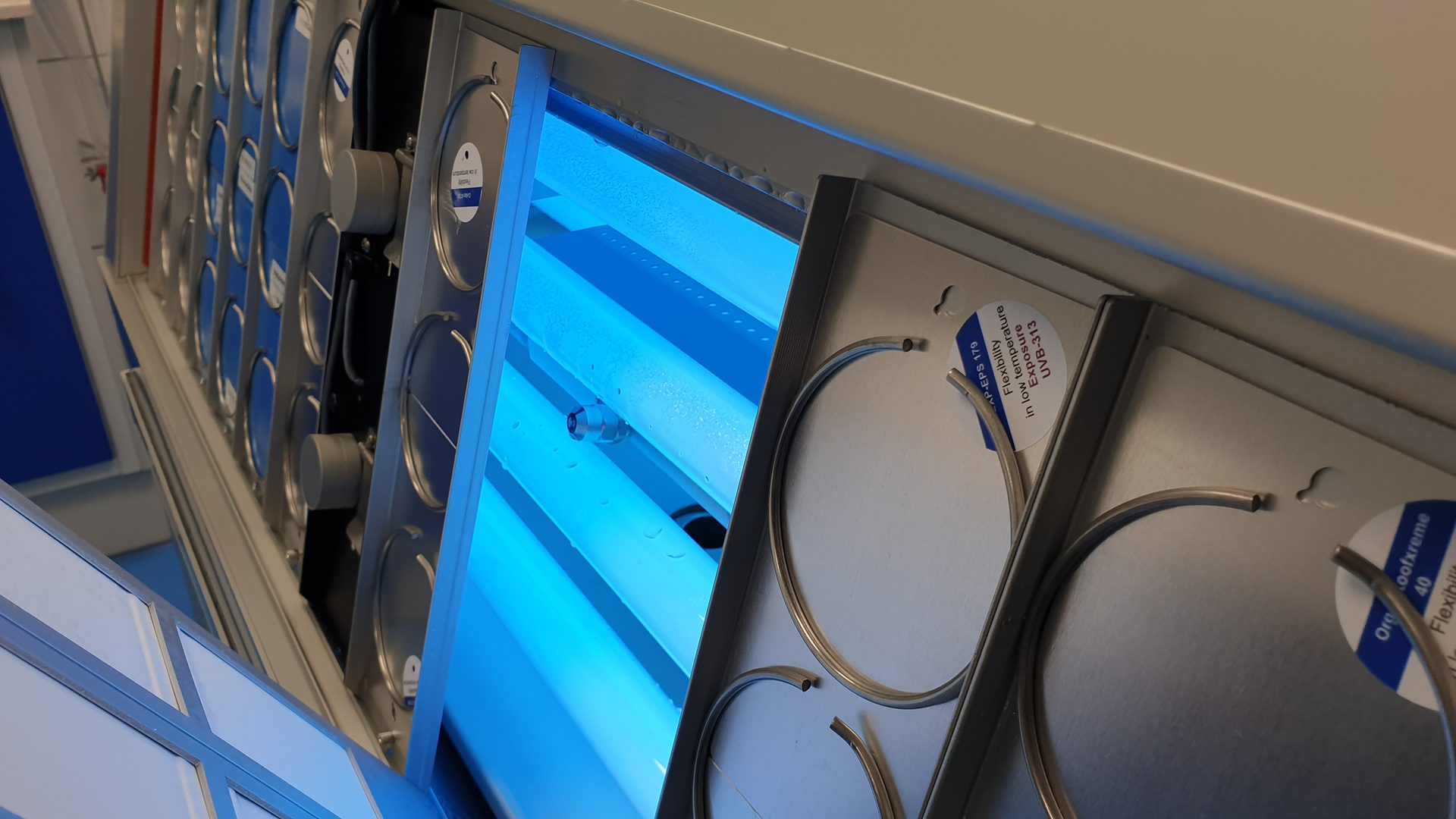
Figure 3. Coating samples inside the Q-UV chamber with UVB-313EL lamps.
Cycle 5 in the ASTM G154 standard involves longer exposure to UV rays (20 hours per cycle), with radiation from UVB-313EL lamps being much more aggressive than UVA-340 lamps. UVB-313EL lamps emit radiation that includes significant unnatural UV bands below the solar cut-off of 295 nm. These lamps are typically used to test the durability of extremely resilient coatings and to assess performance in simulated conditions of extreme radiation.
The project aimed to examine how polymer dispersions affect changes in coating properties under extreme test conditions. The coatings were subjected to 42 daily cycles of UV radiation from UVB-313EL lamps, alternating with condensation, causing the coatings to become more porous and saturated with water vapor. They were then dried at an elevated temperature of up to 80 °C during the radiation phase. The choice of the condensation cycle was made to observe differences between binders in terms of chalking. Using water spray during exposure could wash away any chalking that formed.
Table 3. Comparison of the exposure cycle used with the typical ASTM G154 cycle.
The exposure was conducted in accordance with ASTM G154, Cycle 5, as described in Table 3. A comparison with the more commonly used Cycle 1, and the rationale for selecting this more aggressive exposure method, is also provided in Table 3.
The results in Table 4 show elasticity changes in some samples, particularly those based on binders A, B, C, D, and I. Sample A exhibited failure after exposure, but only in the elasticity test at -26 °C. Before and after exposure, it passed the bend test at -10 °C. The binder used for sample A had a Tg of 0 °C. By comparison, sample D failed the test even before exposure, unable to withstand the bend test at both -10 °C and -26 °C, despite having a slightly lower Tg (-5 °C). This suggests that relying solely on Tg when selecting polymer dispersions for applications like elastomeric roof coatings is not ideal. Many theoretical Tg calculations or measurements do not accurately interpret the binder’s elasticity, especially at temperature extremes. While not all climates require binders with a Tg of -30 °C to -40 °C, which can achieve excellent elasticity even after exposure, it is crucial to carefully test binders for specific applications where flexibility is critical.
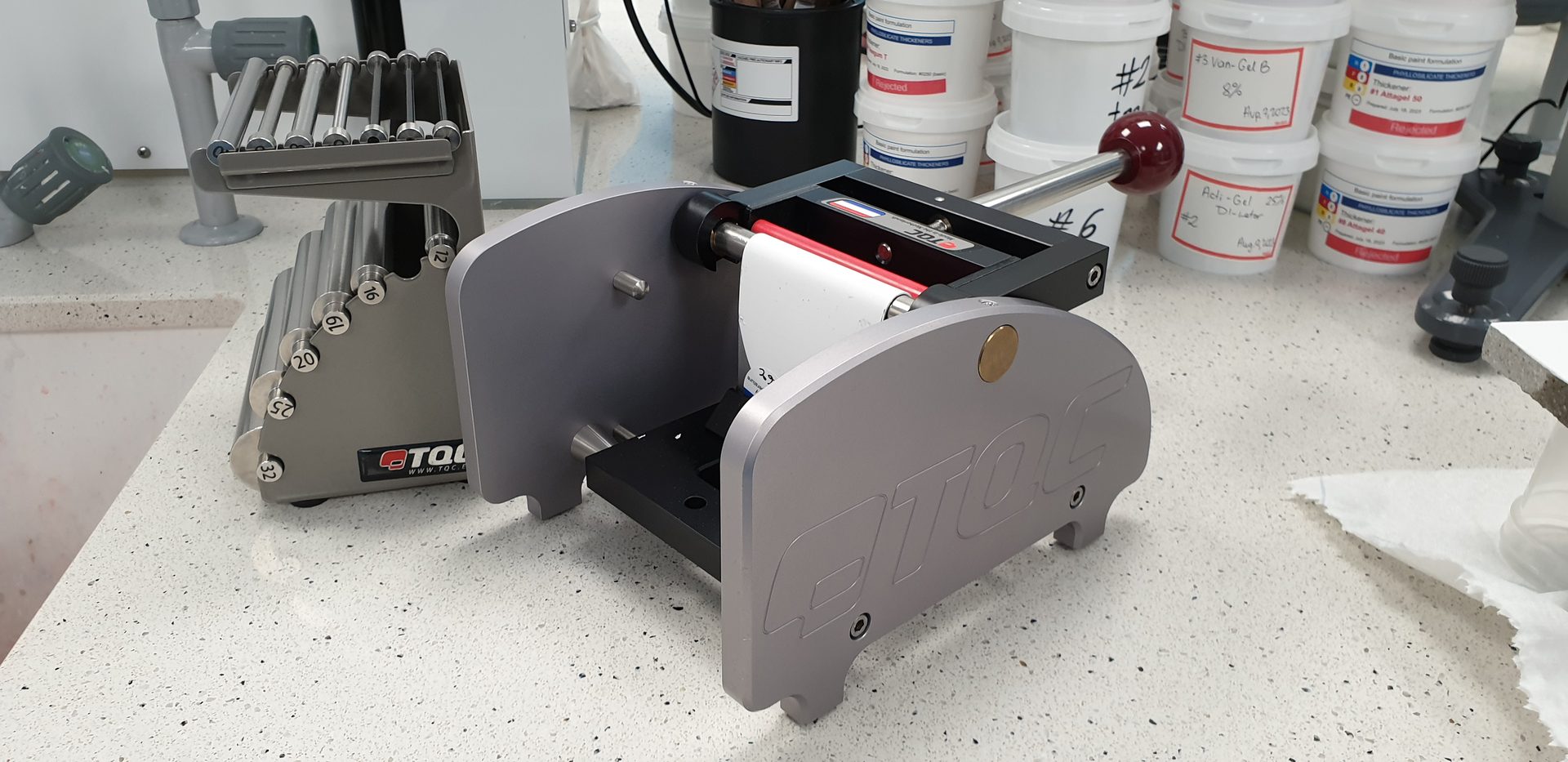
Figure 4. Flexibility testing device with bent coating on a cylindrical mandrel.
Flexibility Before and After Exposure
To measure changes in the coatings after exposure in the QUV chamber, several methods were used, including a flexibility assessment. The test, carried out according to ASTM D522 (mandrel bend test) (Figure 4), involved bending the coating on cylindrical pins to assess the change in flexibility compared to unexposed samples. The bend test was conducted on coatings frozen to -10 °C (14 °F) and -26 °C (-15 °F) by bending them on a cylindrical mandrel with a diameter of 0.5 inch (13 mm), as required by ASTM D6083. The results of the assessment are presented in Table 4.
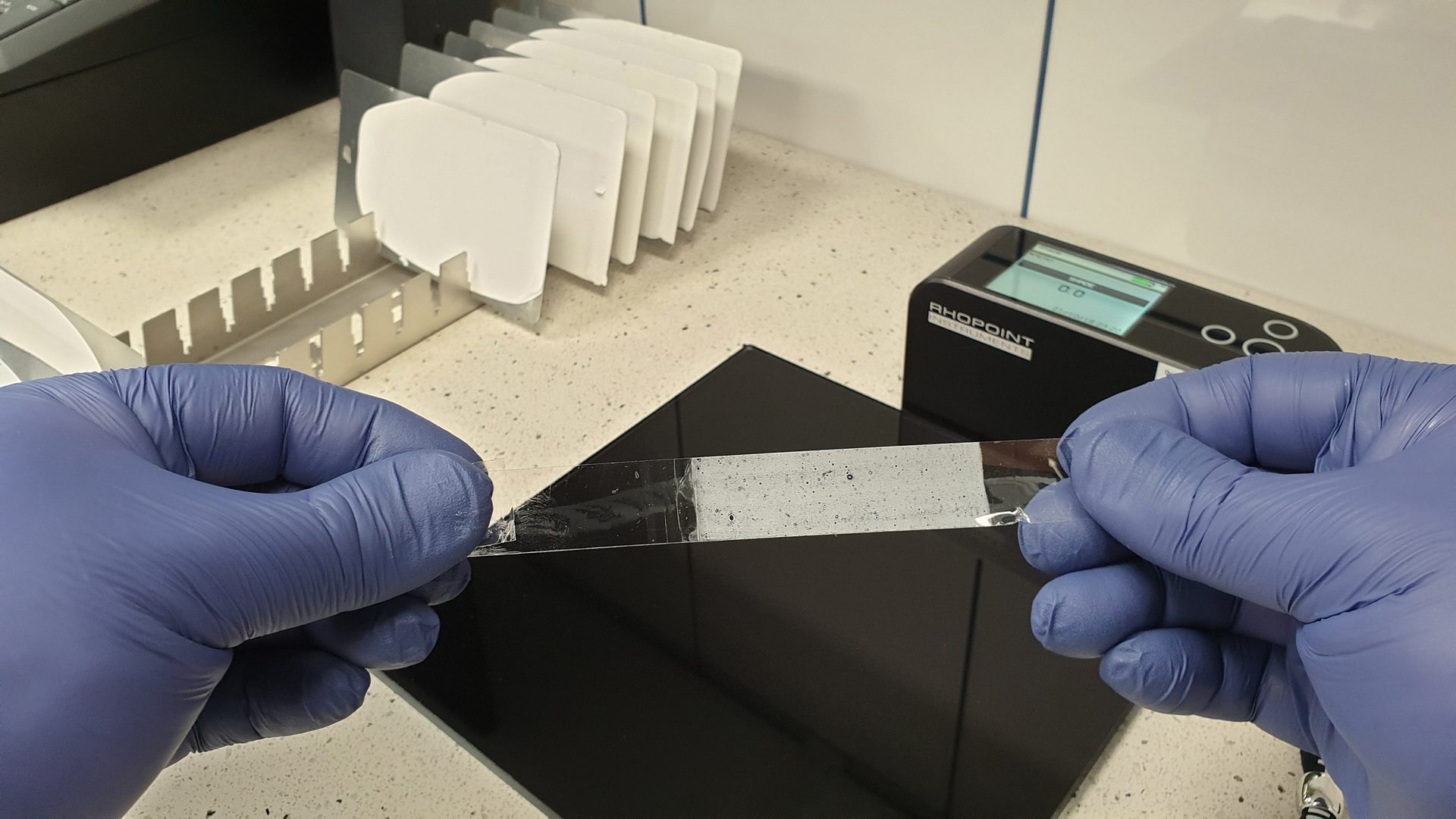
Figure 6. ASTM chalking assessment using tape and reflectometer.
Chalking
Chalking resistance refers to a coating’s ability to resist the formation of a friable powder on its surface, caused by the degradation of the binder due to weather exposure. In roof coatings, this is particularly important since they are constantly subjected to changing weather conditions. Chalking occurs when the binder decomposes, initiated by UV radiation, which was further amplified by the aggressive exposure method selected for this test using UVB-313 lamps. Condensation, rather than spraying, was deliberately used during testing to avoid washing away the chalking that formed. Chalking assessment was conducted according to ASTM D4214 using tape, a BYK opacity/chalking black plate, and a Rhopoint Novo-shade Duo+ reflectometer (Figure 6). The results were compared to the ASTM D4214 chalking rating and are shown in Figure 7.
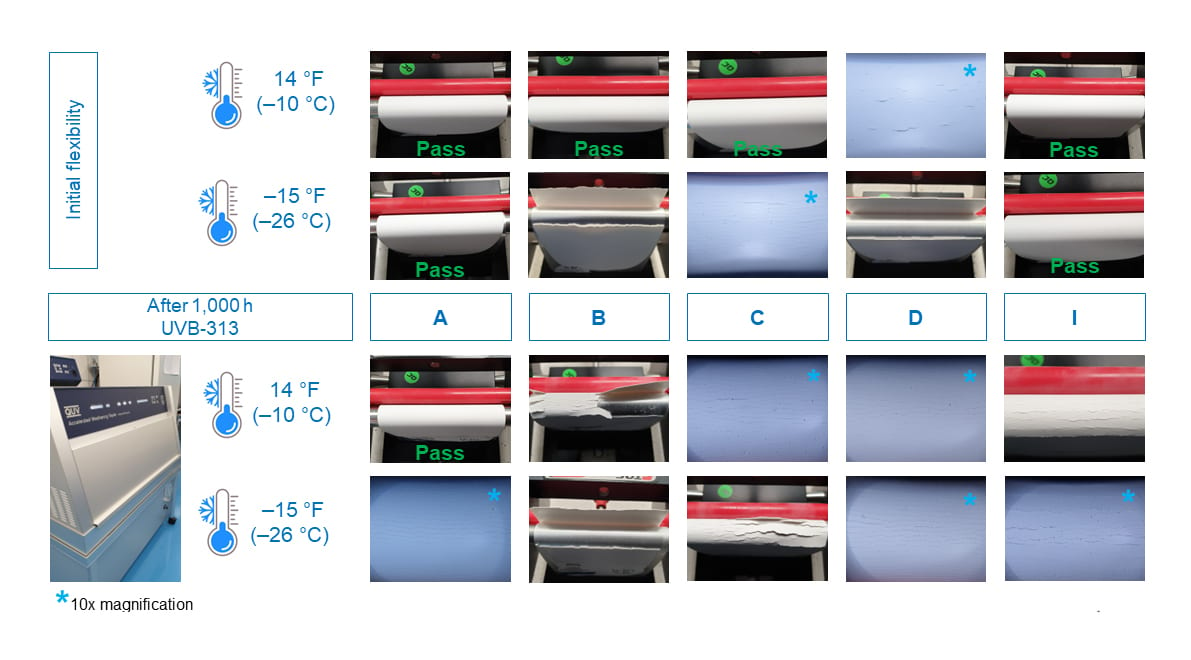
Figure 5. Additional analysis for failed samples.
The bend test was simplified to pass/fail results for ease of assessment. However, for samples that showed differences in flexibility failure after exposure, the extent of failure was further analyzed. Figure 5 presents this additional analysis for samples that shifted from pass to fail, highlighting that not all failures were the same. For example, in some coatings, such as sample A at -26 °C, only surface checking occurred (cracking that did not reach the substrate). This more detailed analysis helps to determine further formulation modifications, such as changing the binder or adjusting the PVC, or even introducing additional plasticizers.
In cases where flexibility results border on acceptable limits, it is also essential to consider other mandrel sizes for the bend test to obtain a more complete picture of elasticity changes.
Summary
The comparative tests conducted represent a case study showing how changes in polymer dispersions within formulations can yield different results in the durability of roof coatings. In the case of liquid elastomeric roof coatings, such comparisons are crucial for determining which polymer dispersions are promising candidates for R&D efforts focused on specific applications. As the test results show, polymer dispersions may be characterized by various parameters in technical data sheets. However, only laboratory comparisons of performance within formulations can reliably indicate which dispersions are suited for use in hot climates, cold climates, or temperate climates. Providing such data to formulators is key to optimizing formulations, accelerating R&D processes, and minimizing potential failures when applied to roofs.
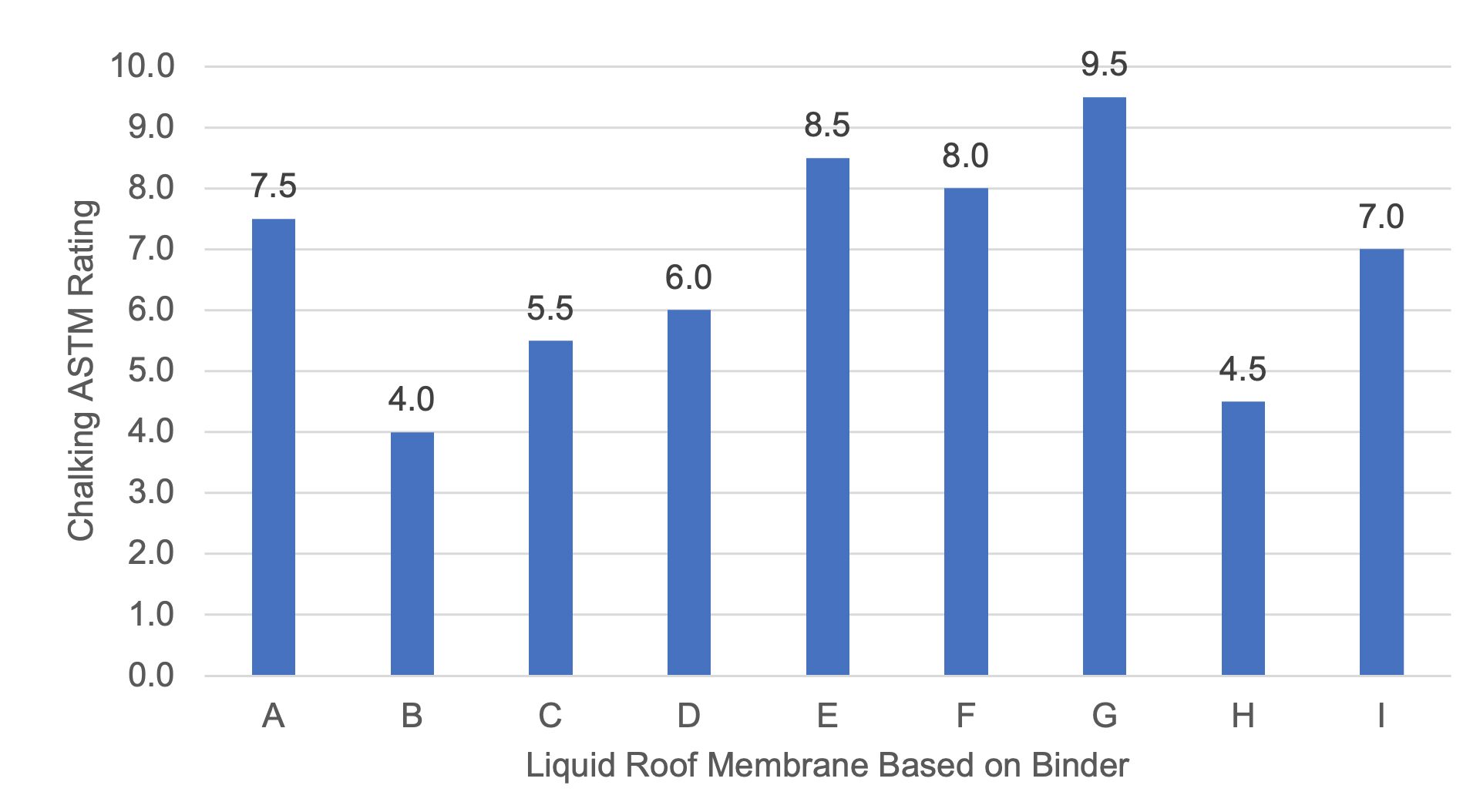
Figure 7. Assessment of chalking on elastomeric roof coatings after 1,000 hrs UV-B 313 exposure.
As shown in the chart (Figure 7), the samples exhibited varying resistance to chalking. The 0-10 scale (0 = greatest chalking, 10 = no chalking) reflects how much friable powder appeared on the coating after exposure. Samples based on binders B and H had the lowest resistance to chalking. For sample B, this negative result was compounded by its poor flexibility and bending resistance at low temperatures. Conversely, for sample H, this result suggests that the dispersion may not be suitable for use in high solar radiation climates but could perform well in environments where flexibility at low temperatures is essential. The best resistance to chalking was observed in samples G and E, which, even after exposure to highly aggressive conditions, demonstrated excellent performance. This indicates they may be ideal for use in climates with high sun exposure.
References
1 ASTM D6083 Standard Specification for Liquid-Applied Acrylic Coating Used in Roofing
2 Advanced modification of liquid acrylic roof membranes with rheological additives in the entire area of shear forces, Artur Palasz, paper European Coatings Show and Conference, Nuremberg 2023
This technical article is based on the presentation given at the CTT Summit 2023, "Influence of polymer emulsions on the durability of liquid acrylic elastomeric roof membranes," by Artur Palasz, SPEKTROCHEM, on September 7, 2023, in Lombard, IL.