SPONSORED CONTENT
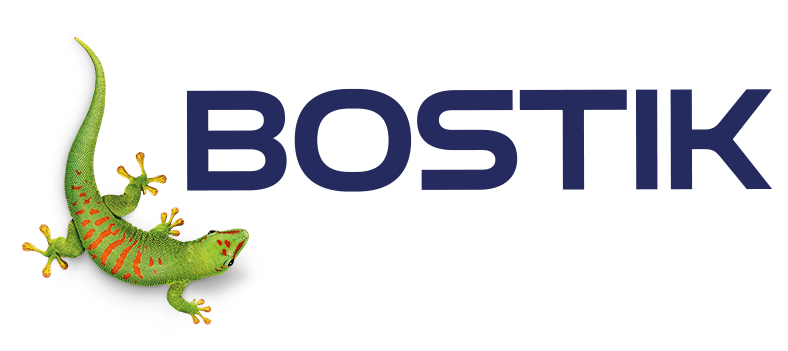
Design for Sustainability with Adhesives in Mind
XXXXX / iStock / Getty Images Plus
By Bostik, Inc.
In today’s industrial markets, manufacturers strive to enhance product sustainability while meeting high performance and efficiency standards. Adhesive selection is key to helping achieve these goals, though historically, adhesives often have been overlooked. This has been primarily due to a lack of awareness and understanding about adhesives and because manufacturers have been inclined to focus simply on whether the adhesive works. However, by assessing an adhesive’s formulation, optimizing performance attributes and understanding end-of-life impact while in the product development stage, manufacturers can better design for sustainability.
Consider an Adhesive’s Formulation
Adhesives are commonly based on fossil fuels, due to extensive historical research and infrastructure created to produce them. However, fossil fuels take millions of years to form; so, heavy reliance on them as feedstock can pose availability concerns. Alternative options exist that can be replenished at a faster rate than fossil fuels, such as adhesives formulated with recycled, bio-based or bio-attributed raw materials. These can include hot melts based partially on natural rosins or polyurethanes developed using vegetable castor oil. In addition to reducing fossil fuel dependency, these adhesives can be a good option to decrease a design’s carbon footprint and help mitigate the climate change impact of material sourcing. They can be processed at decreased temperatures and with fewer steps compared to fossil-fuel-based adhesives, which contributes to energy savings.
It’s also important to choose alternative adhesives formulated with little to no harmful substances, such as certain solvents or isocyanates as well as tin, because they can pose environmental and safety concerns. Instead, manufacturers can consider the latest adhesive innovations. For example, UV acrylic adhesives are formulated to offer high-performance capabilities comparable to solvent-based adhesives but do not contain solvents. As a result, no harmful chemicals are evaporated into the environment during production. Isocyanate-free adhesives, such as silyl modified polymers or low monomer polyurethane adhesives, can be used across industrial applications as well. Other examples include tin-free polyesters for packaging applications and low VOC liquid adhesives for automotive interior trim bonding.
Adhesive formulation can affect manufacturers’ environmental impact during production as well. For example, when an adhesive does not have much or any substance that needs to evaporate first, such as the case with UV acrylics, plant space can be more efficiently utilized, and production lines can run more seamlessly. Additionally, certain adhesives, like hot melts, can be formulated to have low activation temperatures. This helps keep energy usage low.
Manufacturers also can choose adhesives that are formulated for precise application methods to help reduce adhesive usage and waste output. For example, MECA-based, cyanoacrylate instant adhesives can be specifically formulated for “by the dot” needs to help ensure only the right amount of adhesive is dispensed for a given application.
Optimize an Adhesive’s Performance Attributes
When designing for sustainability, it’s also important for manufacturers to consider an adhesive’s ability to form and maintain proper bonds to certain substrates. For example, highly-recycled corrugate is a more sustainable material than virgin corrugate, which is why many package manufacturers may want to utilize it in their package designs. However, this type of packaging substrate is comprised of short paper fibers; adhering to the fibers can prove challenging, primarily because they have minimal surface area and therefore reduced points of contact for the adhesive to bond. These fibers also can be uneven and porous, which can cause adhesive performance issues. Additionally, low-surface-energy package materials (polyethylene and polypropylene) are deemed sustainable for several reasons; for example, they can be easily recycled, and their durability helps extend packaged products’ life. However, these materials also can be difficult for adhesives to form and maintain a bond, because their smooth surface’s molecular structure causes them to naturally resist adhesion.
To overcome these challenges, manufacturers should consider adhesives with performance attributes optimized for more sustainable substrates. These can include having tailored polymer chemistry or incorporating additives that improve wet out and penetration.
When designing residential house wraps for building envelope applications, manufacturers may also want to use more sustainable, low-surface-energy materials, such as nonwovens. Nonwovens offer some sustainability advantages over traditional house wrap materials; for example, they allow for increased breathability, which allows unwanted moisture to escape and is key in certain environments. However, nonwoven materials can pose adhesion challenges because of texture or surface coatings. It is important to select appropriate adhesive and sealant solutions designed to be compatible with nonwoven house wraps to sufficiently protect the building from air and moisture infiltration and ultimately improve energy efficiency.
Further, it is beneficial to assess the range of materials to which the adhesive can bond. Choosing an adhesive that can bond to many substrates allows for optimized material usage that can reduce overall footprint and waste. This capability contributes to decreased SKU needs and improved manufacturing efficiencies, which also help minimize carbon footprint.
Consider an Adhesive’s End-of-Life Impact
While adhesives often account for a small volume of the finished product, they can affect the entire product’s environmental impact at the end of its life. In certain applications, when not removed properly, adhesives can compromise recycling stream effectiveness. For example, polyethylene terephthalate (PET) bottles and trays can be recycled and repurposed into other PET-based products; this contributes to overall circularity. However, if the bottle or tray uses labels with adhesives that are unable to properly wash off from the product during the agitation process, then the label’s materials, such as the paper, inks and coatings, can cause recycling stream contamination. Ultimately, this can render recycled polyethylene terephthalate (rPET) to have reduced clarity as well as weakened strength and overall structure. While it’s possible that the contaminated rPET can still be turned into other recycled items, such as clothing fibers or carpets, it can no longer contribute to PET circularity. Therefore, manufacturers should consider an adhesive that offers wash-off capabilities across application and temperature ranges to improve PET circularity.
Additionally, as stated in this article, certain cold seals may influence polyethylene (PE) recycling stream effectiveness as well and render recycled PE film unusable in second- or third-generational packaging. This is because they may cause gels, and therefore holes, to form when blowing recycled PE resins into film, which can hinder the film’s appearance and functionality. Certain cold seals may also cause newly recycled flexible PE to lose its rigidity and cause it to be unusable for applications that require specific film tension. Further, they may decrease recycled PE film properties, making it unfit for its intended end-use application and leading to waste. Therefore, to minimize contamination and improve recyclability levels, it’s important for manufacturers to consider adhesives that have passed third-party testing protocol, such as those established by the Association of Plastic Recyclers or RECYCLASS. They can consult this article that details how to create a PE film packaging structure that passes the tests. Manufacturers can also consider certain reseal and laminating adhesives that are approved to be co-recycled under the right conditions.
Certain adhesives can help end-use products decompose at the end of life as well. While many adhesives can deteriorate over time, their composition as well as biological and environmental conditions can cause them to take centuries to do so, hindering the end-use product’s ability to break down, too. This can contribute to landfill waste and trash found in oceans. Therefore, when applicable, manufacturers should consider adhesives designed specifically to break down more quickly and naturally, such as those that can be used in compostable packaging applications.
Further, easy material separation helps with recycling efficiencies, resource conservation, energy reduction and more. However, it can be challenging to achieve this separation due to several factors, including complex materials and chosen adhesives. One way to alleviate this issue is to create monomaterial, uniform products whenever possible. This means that all components, including the adhesives, are of the same chemistry backbone to facilitate streamlined recycling. For example, industrial carpets are often made with polyester carpet fibers; therefore, choosing a polyester-based carpet adhesive over a latex-based adhesive helps enable the entire carpet to be recyclable and reduce landfill waste.
The journey to reduce environmental impact throughout a product’s lifecycle is a key challenge to tackle. Closing the circulatory loop and changing the way products are designed require more collaboration than ever, and Bostik, the adhesive solutions segment of Arkema, is here to help. In addition to formulating solutions to meet performance and sustainability goals, Bostik offers dedicated, technical expertise at a global and regional scale. By understanding how adhesives influence sustainability levels throughout a product’s life, manufacturers can better design for sustainability. Contact a Bostik expert today to learn more.
All images courtesy of Bostik.