SPONSORED CONTENT
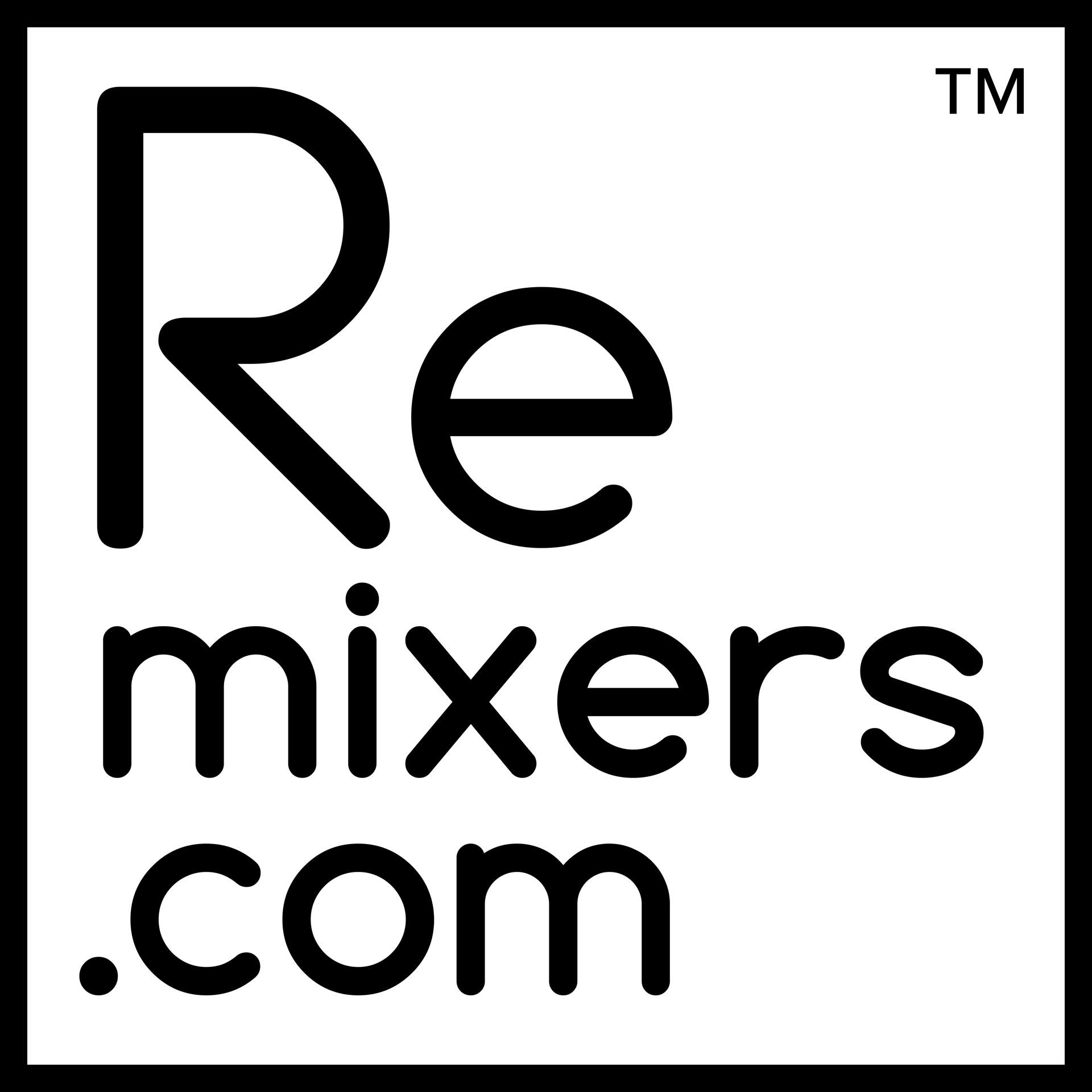
The Next Generation of Static Mixing Nozzles
Rattankun Thongbun / iStock / Getty Images Plus
Figure 1: Bell and Bayonet mixing nozzles utilizing third-generation Xemex mixing technology.
By Eric Ronning, Founder & CEO, Re Mixers Inc., Madison, Wisconsin
How additive manufacturing and advanced mixing science are driving the adoption of ultra-efficient nozzles, disrupting a 50-year-old industry.
Share-ify Launches Into 2024 after Stellar 2023 Results
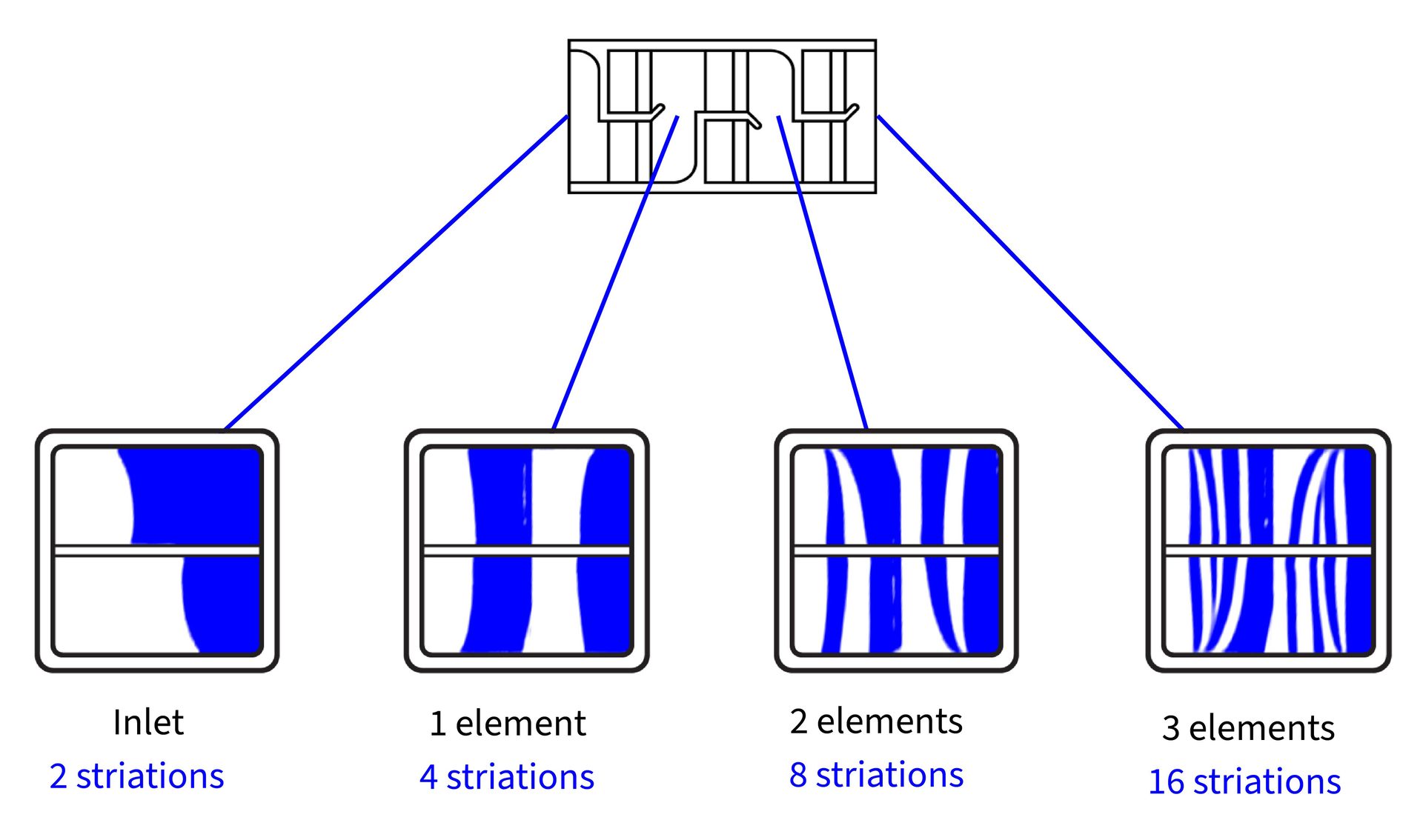
Figure 3: Second-generation mixers also utilize the baker’s transformation to generate 16 striations after 3 elements.
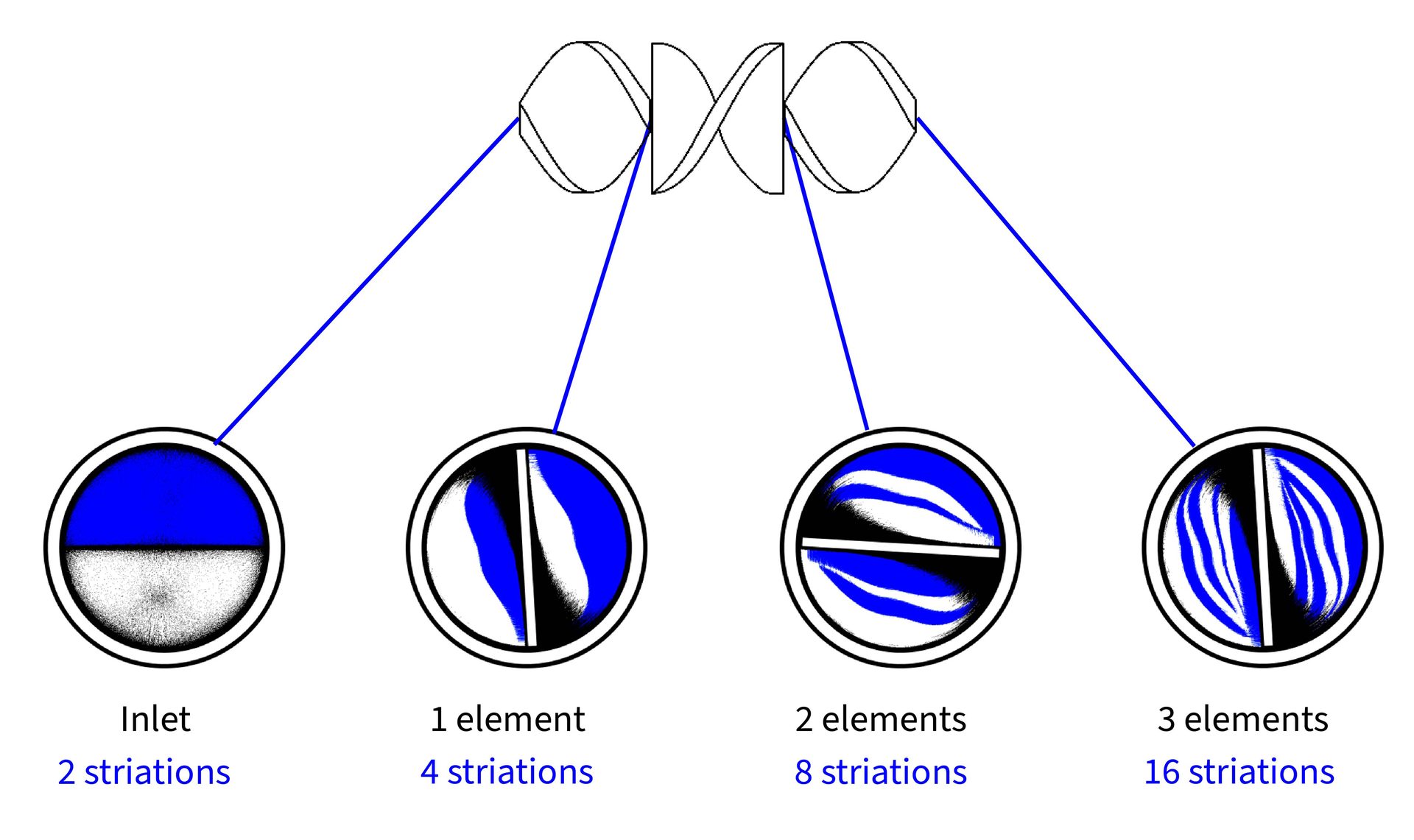
Figure 2: First-generation mixing nozzles utilize the baker’s transformation to produce 16 striations after 3 helical elements.
In recent years, manufacturers have realized the vital role mixing nozzles play in their operations. Traditional designs are not only wasteful but also plagued by supply chain disruptions, impacting industries reliant on 2K adhesives. Now, a new wave of advanced static mixers is transforming the landscape — delivering unprecedented efficiency, superior mix quality, and a reliable U.S.-based supply that challenges the old standards. These innovations are now prompting manufacturers to rethink their mixer choices for both new and existing 2K adhesive applications.
Baker’s Transformation
Traditional helical mixing nozzles use a method called the baker’s transformation, inspired by the way bakers knead dough. These first-generation nozzles double the fluid striations with each mixing element, typically requiring 24 to 32 elements to effectively mix two-part adhesives. This large element count leads to significant adhesive waste, driving up costs for industrial users.
In the early 2000s, certain initiatives spurred the development of more efficient alternatives. This led to square-shaped mixers, a second-generation design aimed at reducing waste. However, these mixers still rely on the baker’s transformation and generally need 24 to 32 elements for adequate mixing, limiting their waste reduction to just 7% compared to helical designs.
A straightforward way to evaluate mixer efficiency is by counting fluid striations after each element. As illustrated in Figures 2 and 3, both first- and second-generation designs require three elements to achieve 16 fluid striations, highlighting their inherent limitations.
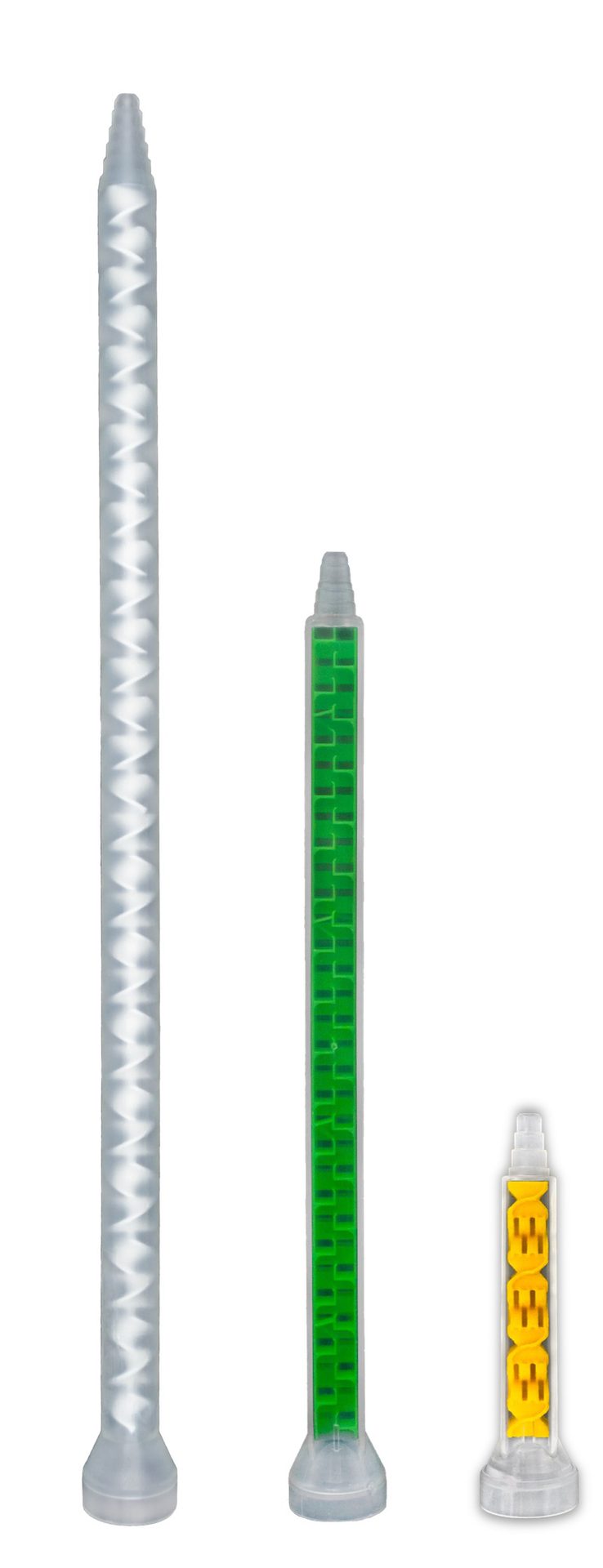
A visual comparison of first-, second-, and third-generation mix nozzles.
Sustainability & Impact
Xemex nozzles bring several key advantages over previous designs: superior mix quality, closer application to work surfaces, and precise positioning in automated systems. Most compellingly, these nozzles cut adhesive waste by 75%, helping manufacturers meet their sustainability goals.
Adhesive waste from traditional nozzles is substantial. Standard practice involves purging an amount equivalent to the nozzle’s internal volume before use, which is doubled in retained volume after use. First- and second-generation mixers waste an average of 19.1 mL per nozzle. In contrast, Xemex nozzles reduce this to just 5.0 mL, offering such significant efficiency gains that they effectively pay for themselves when compared to legacy designs.
A moderate manufacturer using 1,000 nozzles annually can eliminate 14,100 mL of adhesive waste by switching to third-generation technology. On a global scale, where conservatively, an estimated one billion nozzles are used each year, the potential impact is enormous. By transitioning to Xemex mixers, the industry could eliminate up to 12 million kg of adhesive waste annually, marking a significant step towards a more sustainable future.
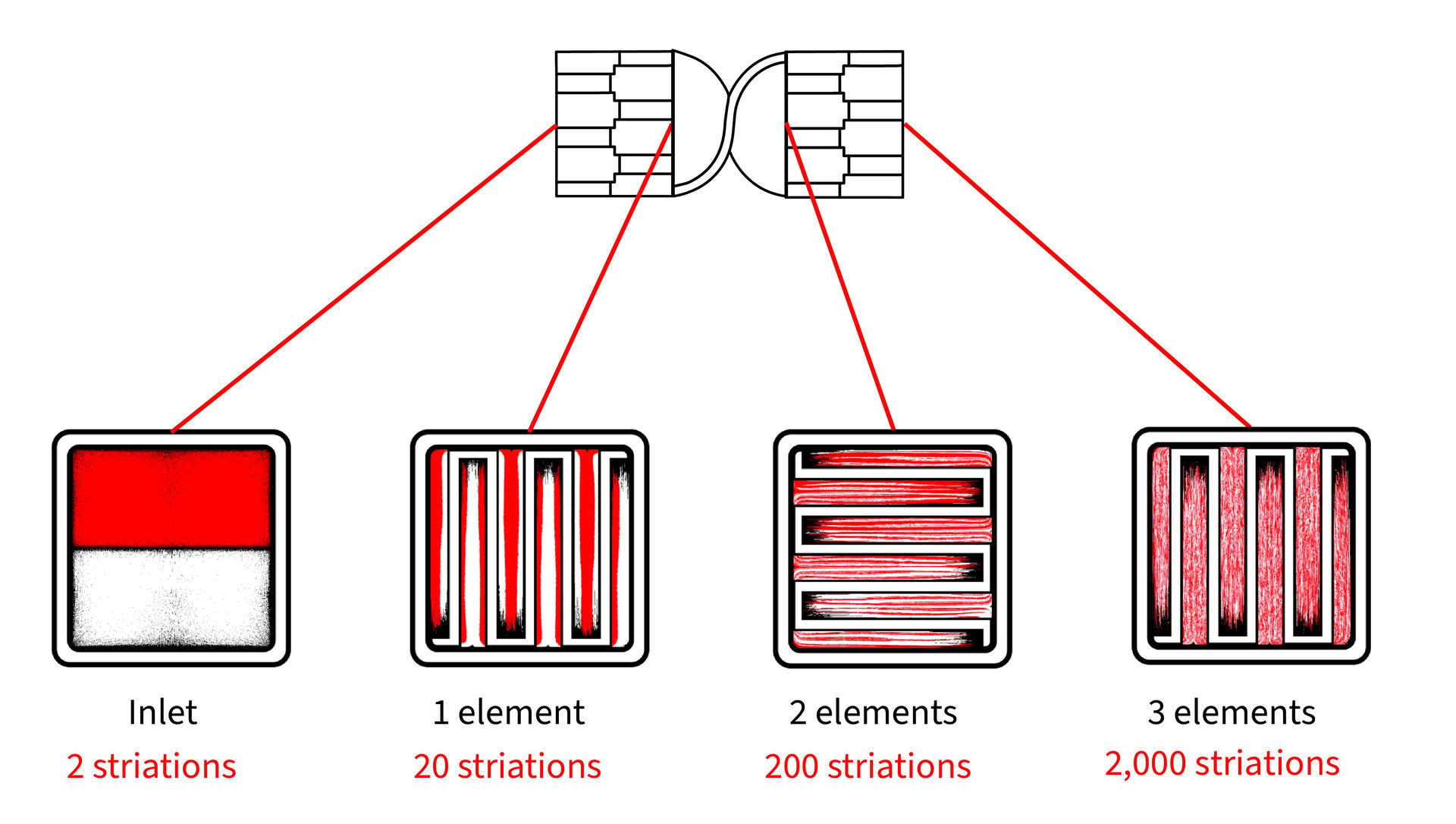
Figure 4: Third-generation mixers utilizing the Xemex transformation produce 2,000 striations after only 3 elements.
Xemex Transformation
Leveraging advanced CFD packages and machine learning techniques, a groundbreaking suite of mixing technologies has emerged. Using a verifiable simulation environment, thousands of virtual geometries were generated and analyzed in a recursive, evolutionary process, resulting in over 6,000 potential models. This approach led to the discovery of a completely new class of higher-order chaotic mapping.
The outcome is a novel mixing method called the Xemex transformation. Unlike the baker’s transformation, which doubles fluid striations per element, the Xemex transformation delivers a tenfold increase per element, offering exponential efficiency gains over traditional static mixer designs.
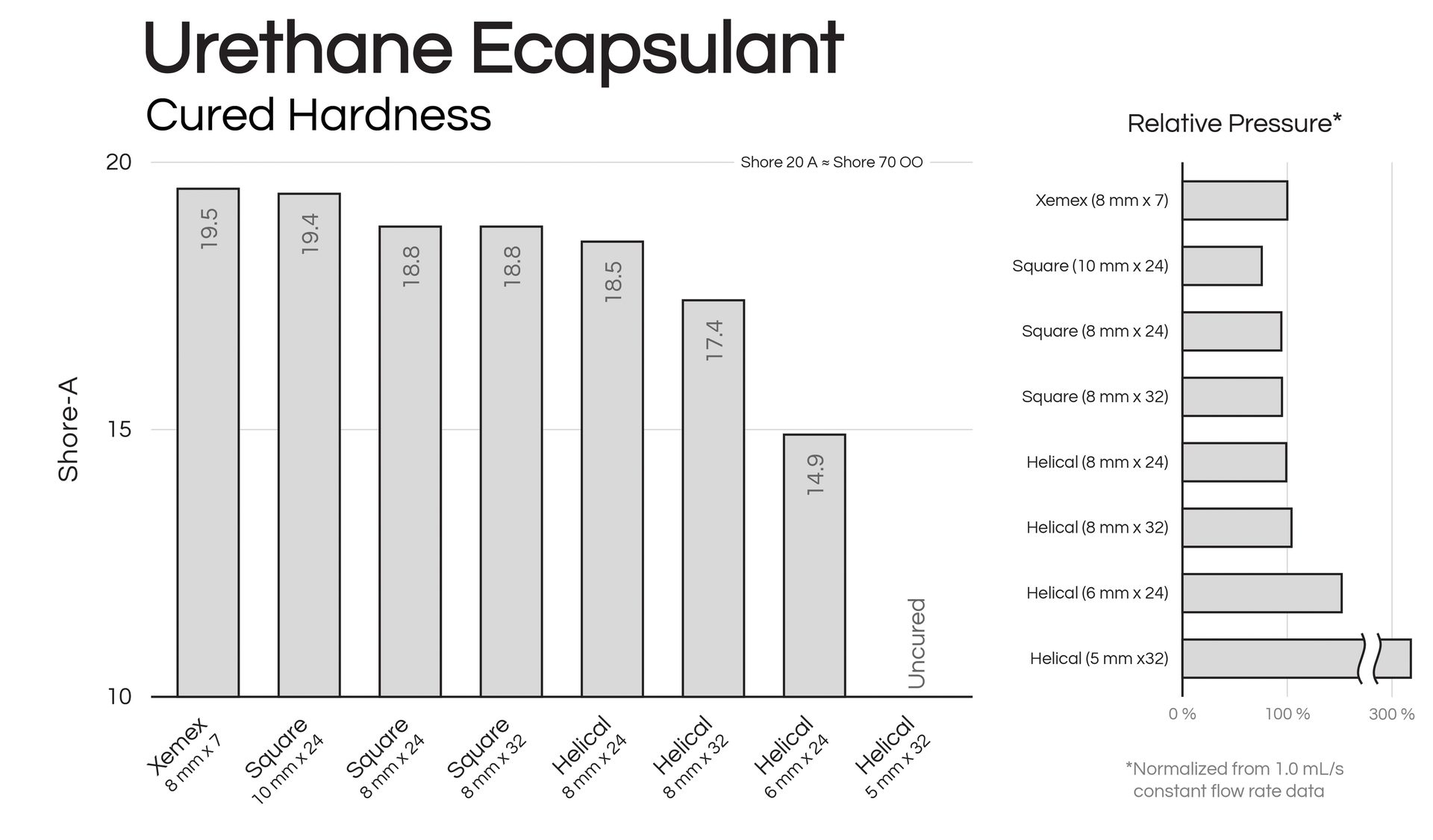
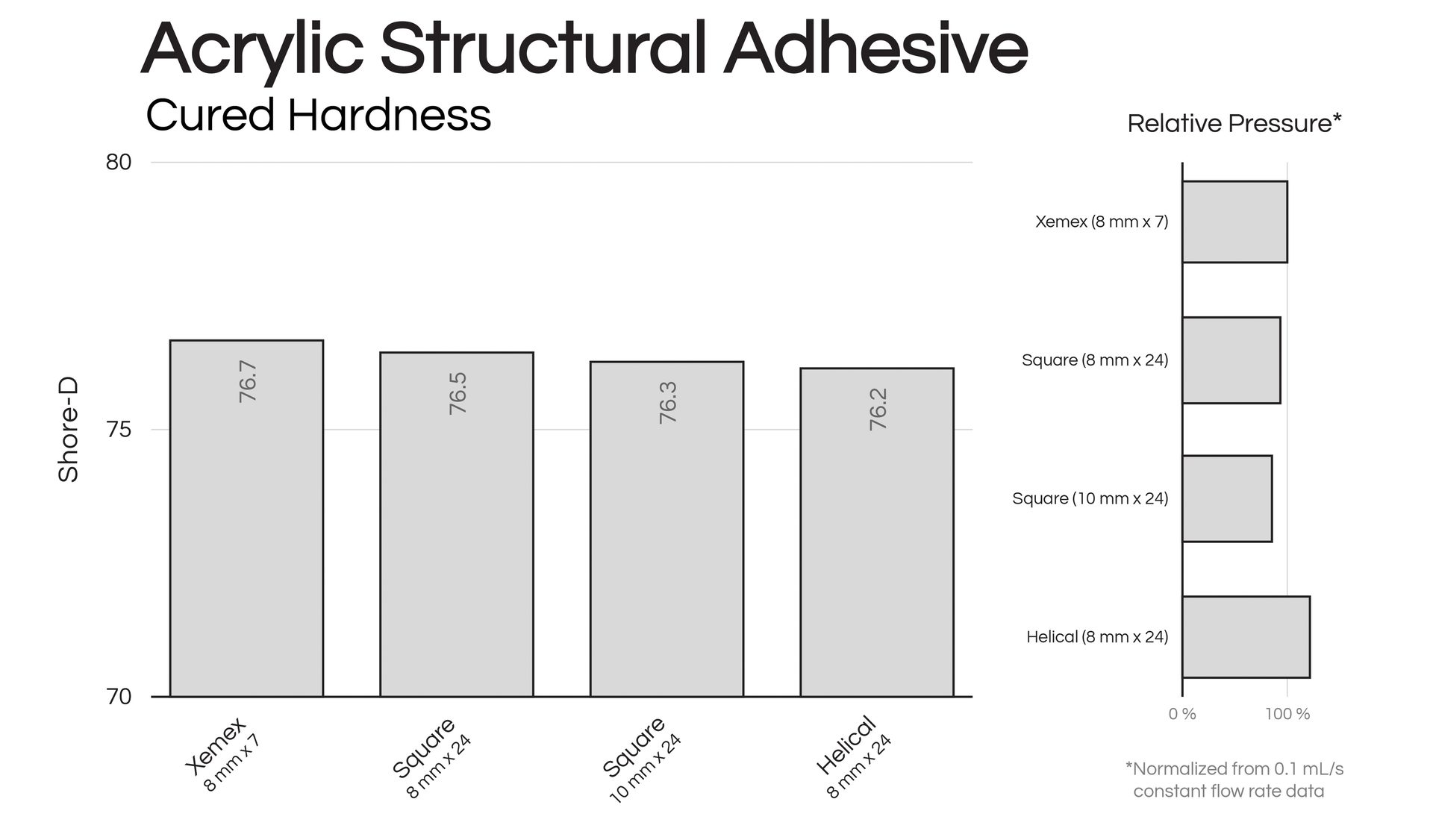
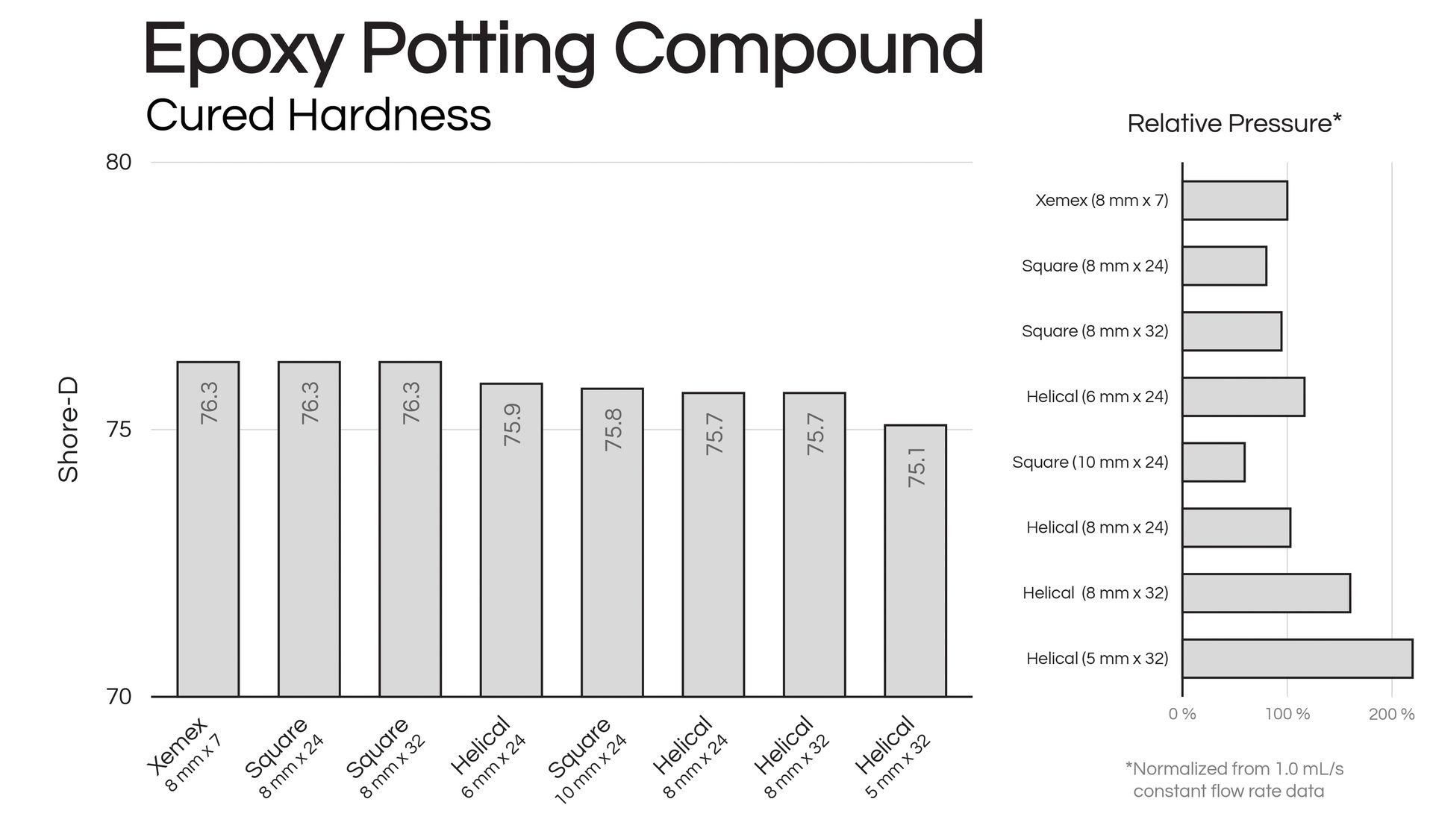
Figure 5: Hardness and backpressure results, summarized across three common applications.
For two-part adhesives, the Xemex transformation achieves optimal mixing with 75% fewer elements. What once required up to 32 mixing elements can now be accomplished with as few as seven. This significant reduction not only enhances adhesive performance but also minimizes waste in customer processes. With fold count per element constrained only by manufacturing capabilities, future applications in larger continuous-flow reactors (such as PFRs) promise even greater efficiency improvements over current industrial mixer designs.
Empirical Validation
While numerical analysis provides a strong foundation for comparing mixer technologies, real-world performance ultimately depends on empirical data. Building on simulation-driven geometries, nearly a thousand additional tests were conducted following ASTM standards. These experiments validated the Xemex transformation for dispensing 2K adhesives and helped identify a single mixer design optimized for the widest range of market applications.
The testing confirmed that relying on "element count" — a common industry metric for mixing capability — is an outdated and unreliable method for selecting a mixing nozzle. Instead, direct empirical data offers a far more accurate basis for comparison.
To present these findings clearly, a standardized white paper format was created, detailing the empirical results of various mixer geometries across common adhesive formulations. Although end-users must validate any mixer design for their specific needs, these results serve as a valuable reference when exploring new applications. A preview of this data is shown in the figures provided, with the full reports available on the Re Mixers, Inc. website (www.remixers.com/white-papers).
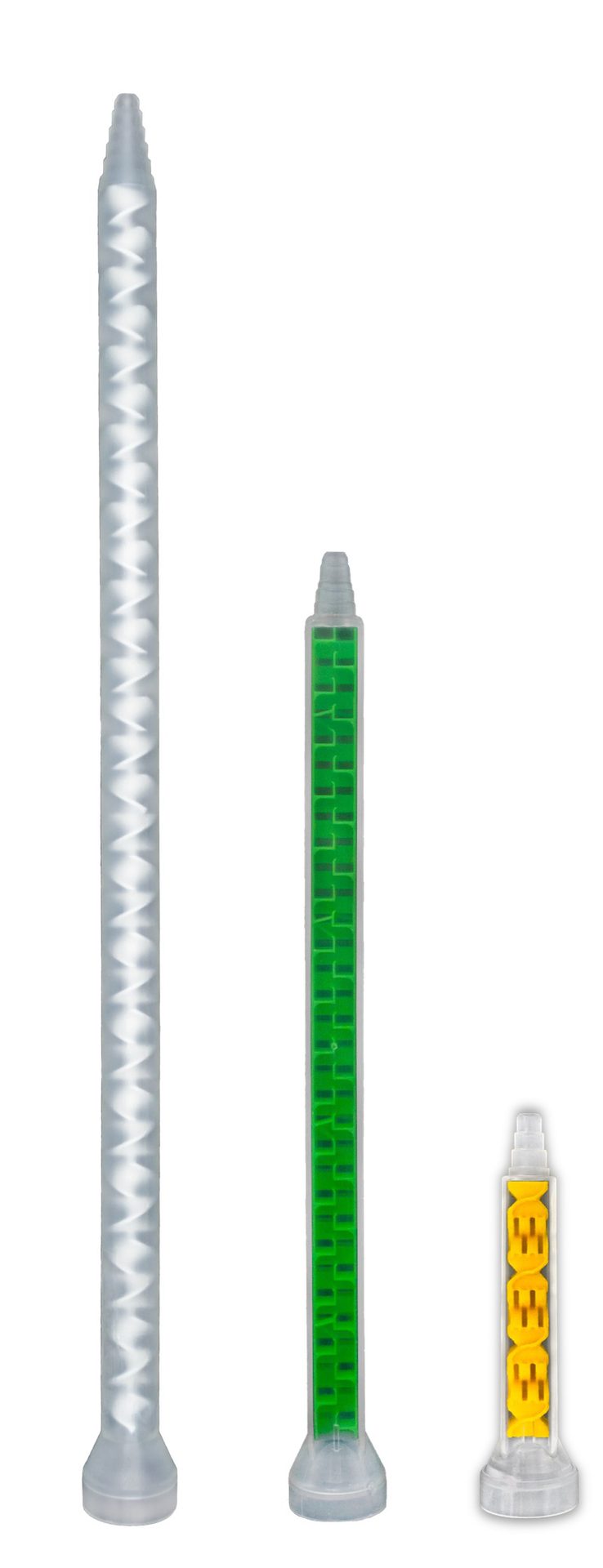
Figure 6: A visual comparison of first-, second-, and third-generation mix nozzles.
Sustainability & Impact
Xemex nozzles bring several key advantages over previous designs: superior mix quality, closer application to work surfaces, and precise positioning in automated systems. Most compellingly, these nozzles cut adhesive waste by 75%, helping manufacturers meet their sustainability goals.
Adhesive waste from traditional nozzles is substantial. Standard practice involves purging an amount equivalent to the nozzle’s internal volume before use, which is doubled in retained volume after use. First- and second-generation mixers waste an average of 19.1 mL per nozzle. In contrast, Xemex nozzles reduce this to just 5.0 mL, offering such significant efficiency gains that they effectively pay for themselves when compared to legacy designs.
A moderate manufacturer using 1,000 nozzles annually can eliminate 14,100 mL of adhesive waste by switching to third-generation technology. On a global scale, where conservatively, an estimated one billion nozzles are used each year, the potential impact is enormous. By transitioning to Xemex mixers, the industry could eliminate up to 12 million kg of adhesive waste annually, marking a significant step towards a more sustainable future.
Re Mixers, Inc. designs and manufactures cutting-edge fluid dispensing technologies at its facility in Madison, Wisconsin. As both an innovator in mixing science and a dependable U.S.-based supplier, Re Mixers is redefining industry standards. Their Xemex line of mixing nozzles delivers a sustainable, efficient alternative to traditional designs, while ensuring reliable supply chain solutions. Learn more at www.remixers.com.
All images courtesy of Re Mixers.