Sponsored Article
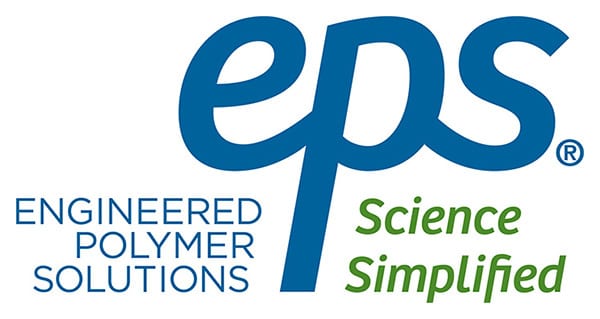
Cool Roofs That Stay Cool
Optimizing Long-Term Reflectivity in Roof Coating Formulations
Cool Roofs That Stay Cool
Optimizing Long-Term Reflectivity
in Roof Coating Formulations
Cool Roofs
That Stay Cool
Optimizing Long-Term Reflectivity in Roof Coating Formulations
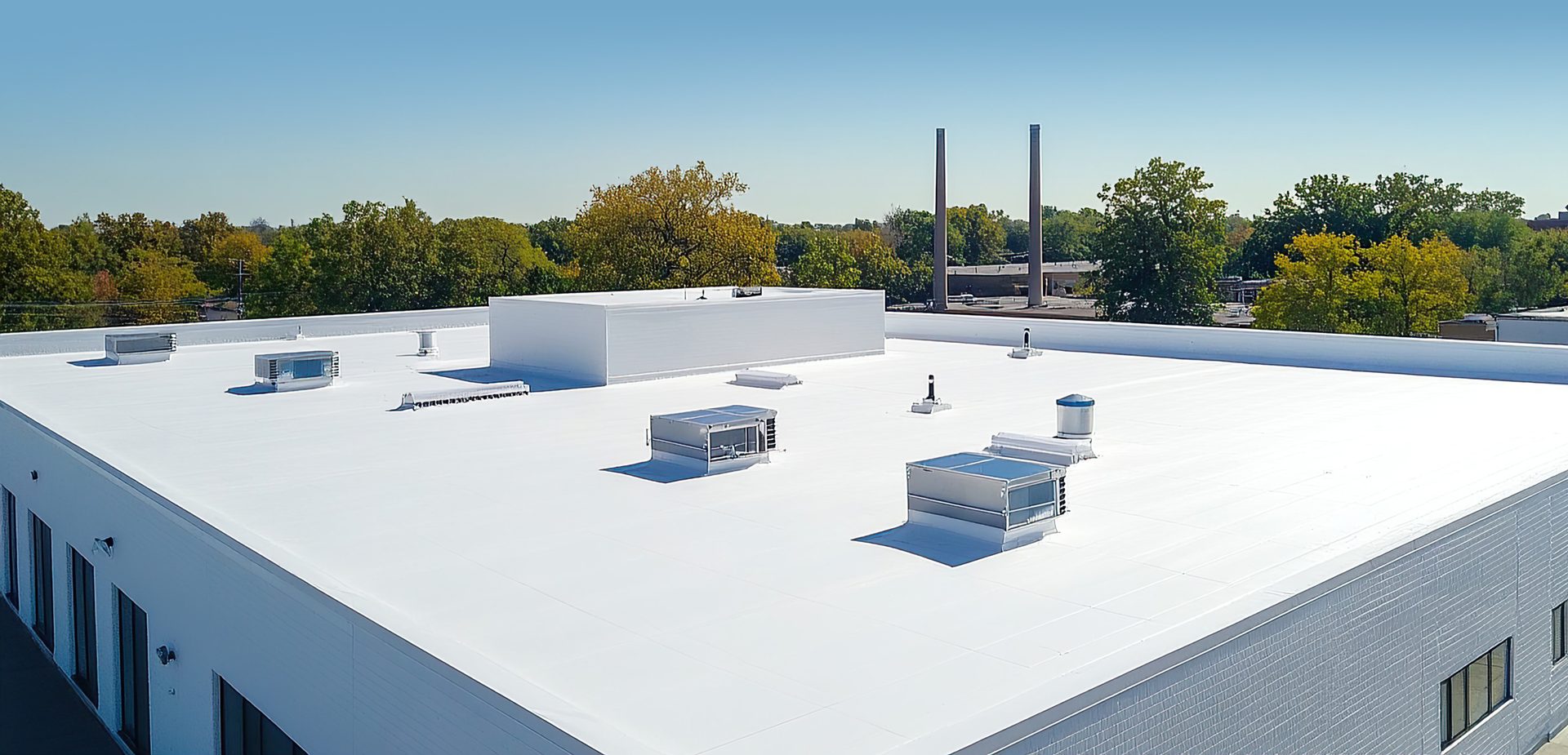
–Credit: Nikola / Adobe Stock–
By Dr. Brent Crenshaw, R&D Senior Scientist, Engineered Polymer Solutions (EPS)
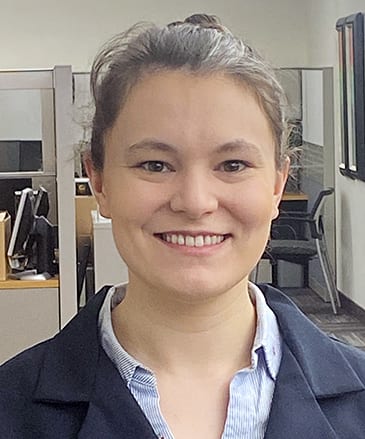
Kristi Ferrato
White acrylic roof coatings are widely recognized for their ability to reduce rooftop temperatures, improve indoor comfort, lower energy costs and mitigate the urban heat island effect. These coatings are especially valued for their high initial solar reflectance and bright white appearance. However, maintaining that performance over time is a challenge — and it all comes down to the formulation.
Environmental exposure gradually degrades reflectivity. Dirt accumulation, microbial growth and bleed-through from underlying materials can all contribute to a loss in performance. This article explores how the choice of acrylic latex is critical to sustaining whiteness and solar performance over the life of the roof.
Understanding Reflectivity
Solar energy reaches Earth as electromagnetic (EM) radiation. When this energy strikes a surface, it is either absorbed — contributing to heat — or reflected. While the sun is the primary source of EM radiation, all objects above absolute zero emit some energy, which is why thermal imaging works.
The solar performance of roof coatings is a combination of the ability of a material to both reflect and emit EM radiation. Three metrics are used to describe this, outlined below and in Figure 1:
- Solar Reflectance (SR): The fraction of solar energy reflected by the surface. Higher SR values mean less heat absorption and cooler roof temperatures.
- Thermal Emittance (TE): The ability of a surface to release absorbed heat. High TE values help the roof cool more efficiently.
- Solar Reflectance Index (SRI): A composite metric combining SR and TE to indicate a material’s overall ability to reject solar heat.
FIGURE 1–ǀ–Illustrative description of solar reflectance, thermal emittance and solar reflectance index.
X
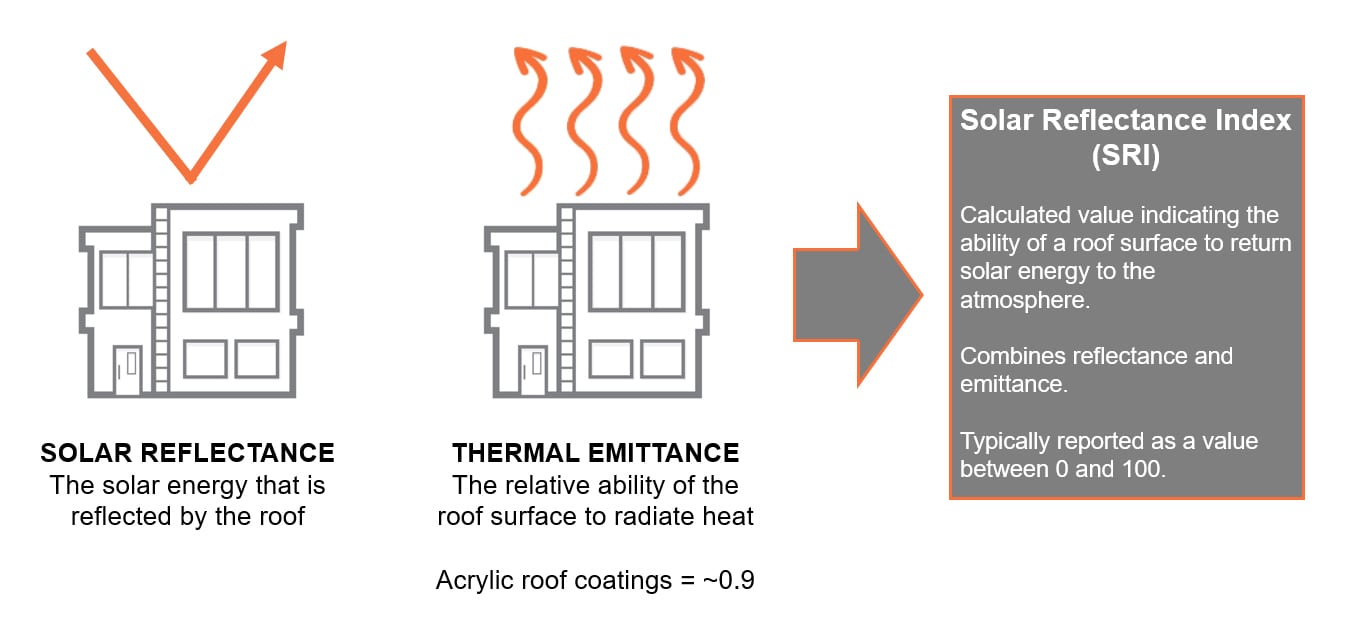
REVERSE PINCH TO ZOOM
X
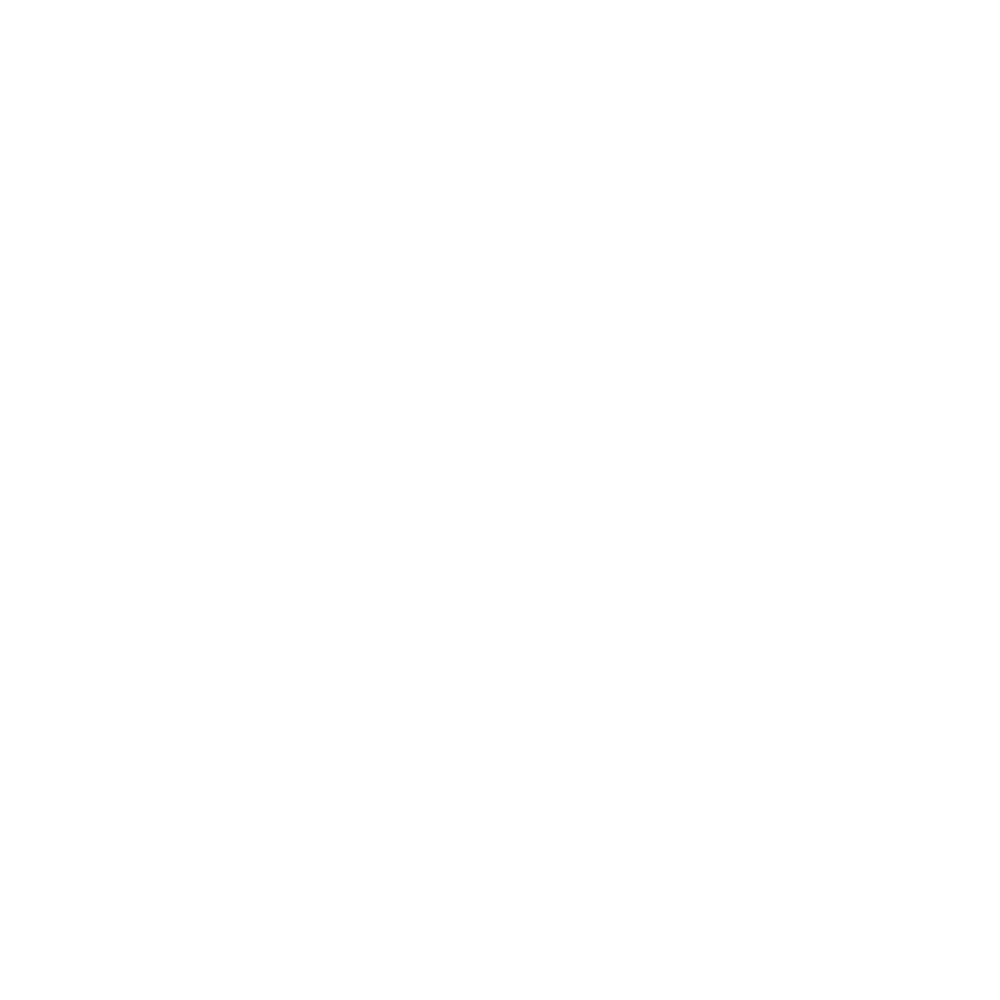
REVERSE PINCH TO ZOOM
X
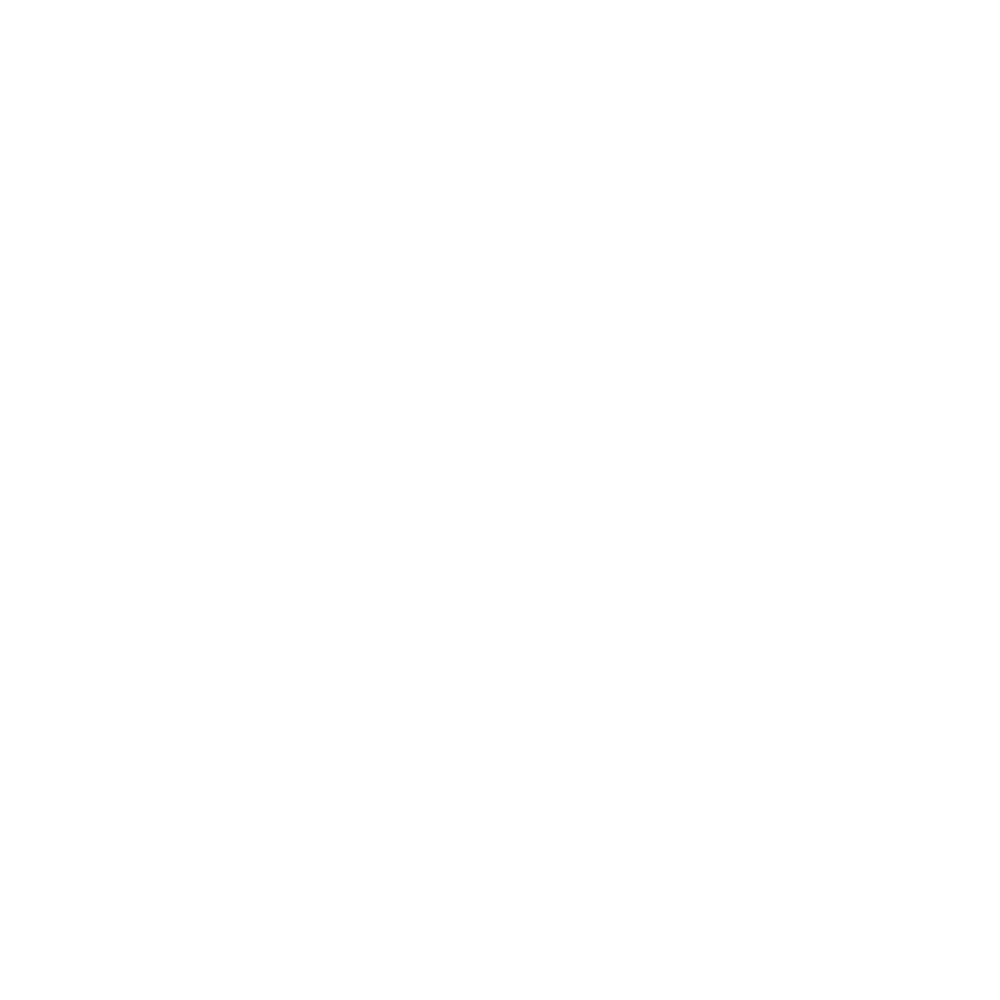
REVERSE PINCH TO ZOOM
X
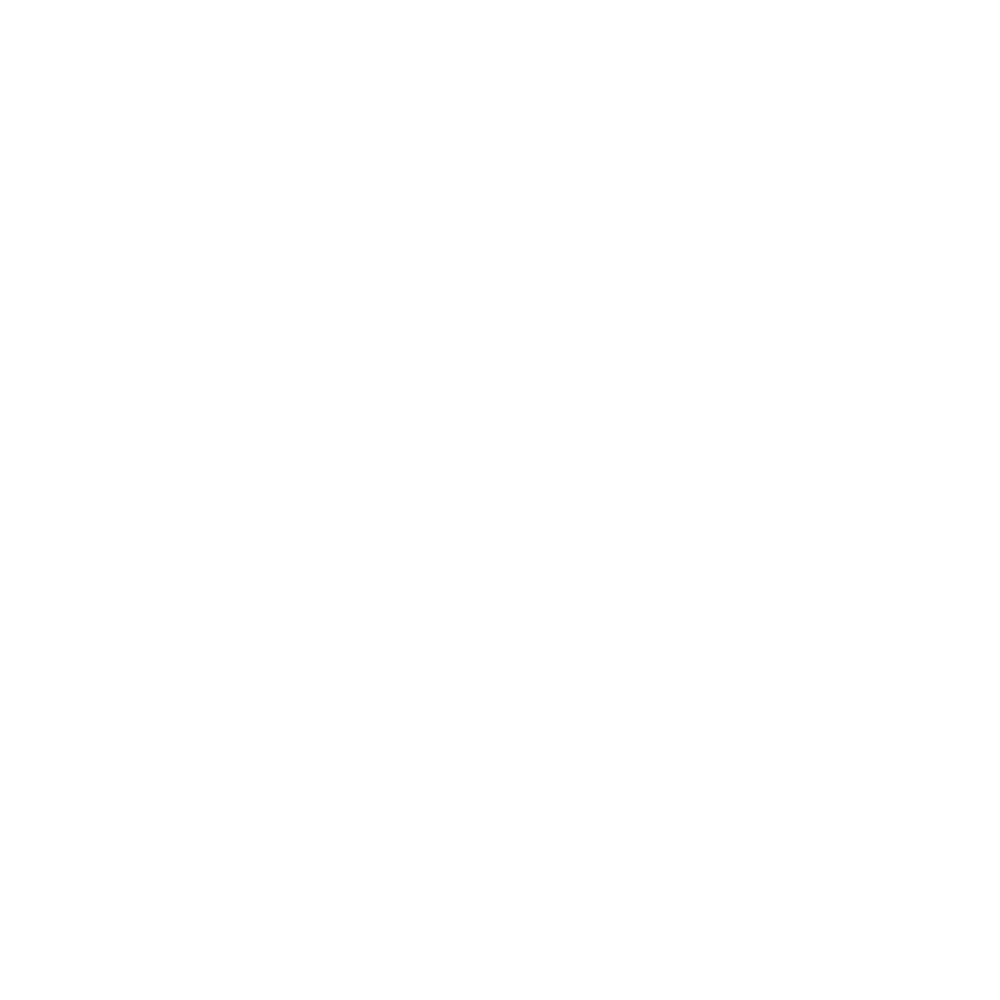
REVERSE PINCH TO ZOOM
Most acrylic roof coatings have a TE of around 0.9, which remains relatively stable over time. Therefore, this discussion focuses primarily on SR.
An acrylic cool roof coating is composed primarily of reflective pigments and other fillers dispersed in an acrylic polymer binder. Titanium dioxide (TiO₂) is the primary pigment responsible for the high reflectivity of white coatings. While initial SR values are typically high, they are not static. A review of initial and 3-year aged SR values for bright white acrylic coatings registered in the Cool Roof Rating Council’s Rated Roof Products Directory¹ shows a decrease in SR that ranges from 0.02 to 0.4, with an average decrease of 0.13. A drop of 0.13 in SR equates to a surface temperature increase of approximately 20 °F. A decrease of 0.4 would result in an average temperature increase as much as 60 °F. Thus, maintaining high SR over time is essential for a coating to be considered a true cool roof solution.
FIGURE 2–ǀ–Histogram of initial solar reflectance and 3-year solar reflectance.
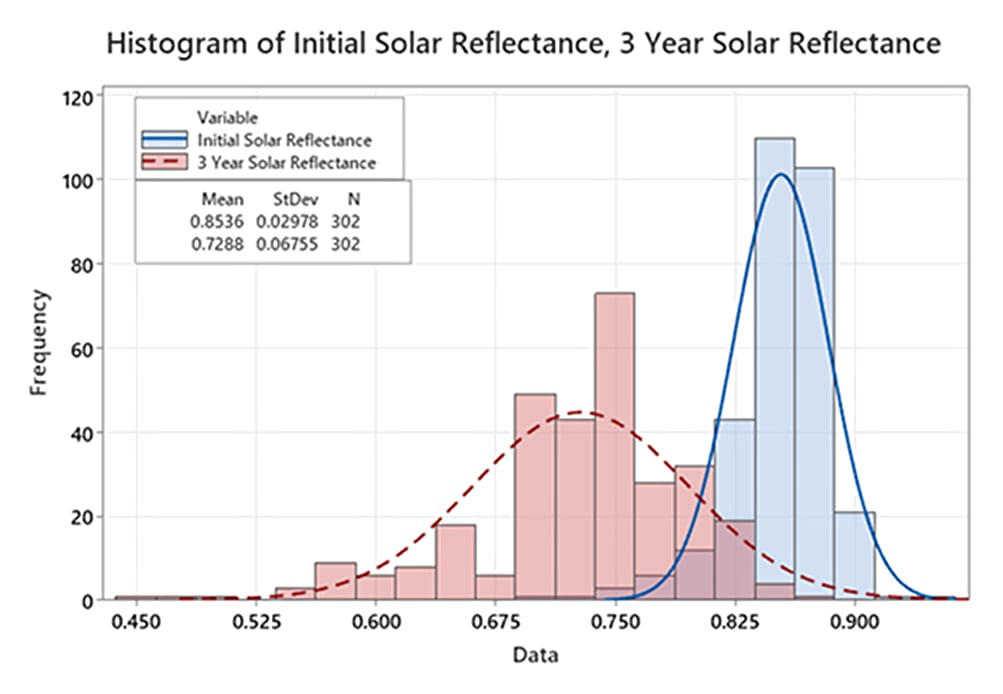
What Causes Reflectivity to Degrade?
Even though TiO₂ remains reflective, other components and environmental factors can interfere with its ability to reflect light. The three most common mechanisms of reflectivity degradation in roof coatings are:
- Bleed-through: Migration of compounds from the substrate through the coating. These compounds can absorb light themselves, change the properties of the coating so it is more susceptible to other mechanisms of reflectivity degradation, or both.
- Biofouling: Fungi and algae grow on the coating surface, blocking light from reaching the coating.
- Dirt pickup: Accumulation of organic and inorganic particles that block light from reaching the surface.
Each of these mechanisms reduces the amount of light that reaches and is reflected by the TiO₂, leading to a less reflective and less effective coating.
Key Formulation Components and Their Impact
Every ingredient in a roof coating plays a role in maintaining reflectivity. While most readers of this article are likely very familiar with the composition of a waterborne acrylic coating, Figure 3 and Table 1 help illustrate how each component can affect the coating’s resistance to reflectivity degradation.
FIGURE 3–ǀ–Primary components of an acrylic roof coating.
X
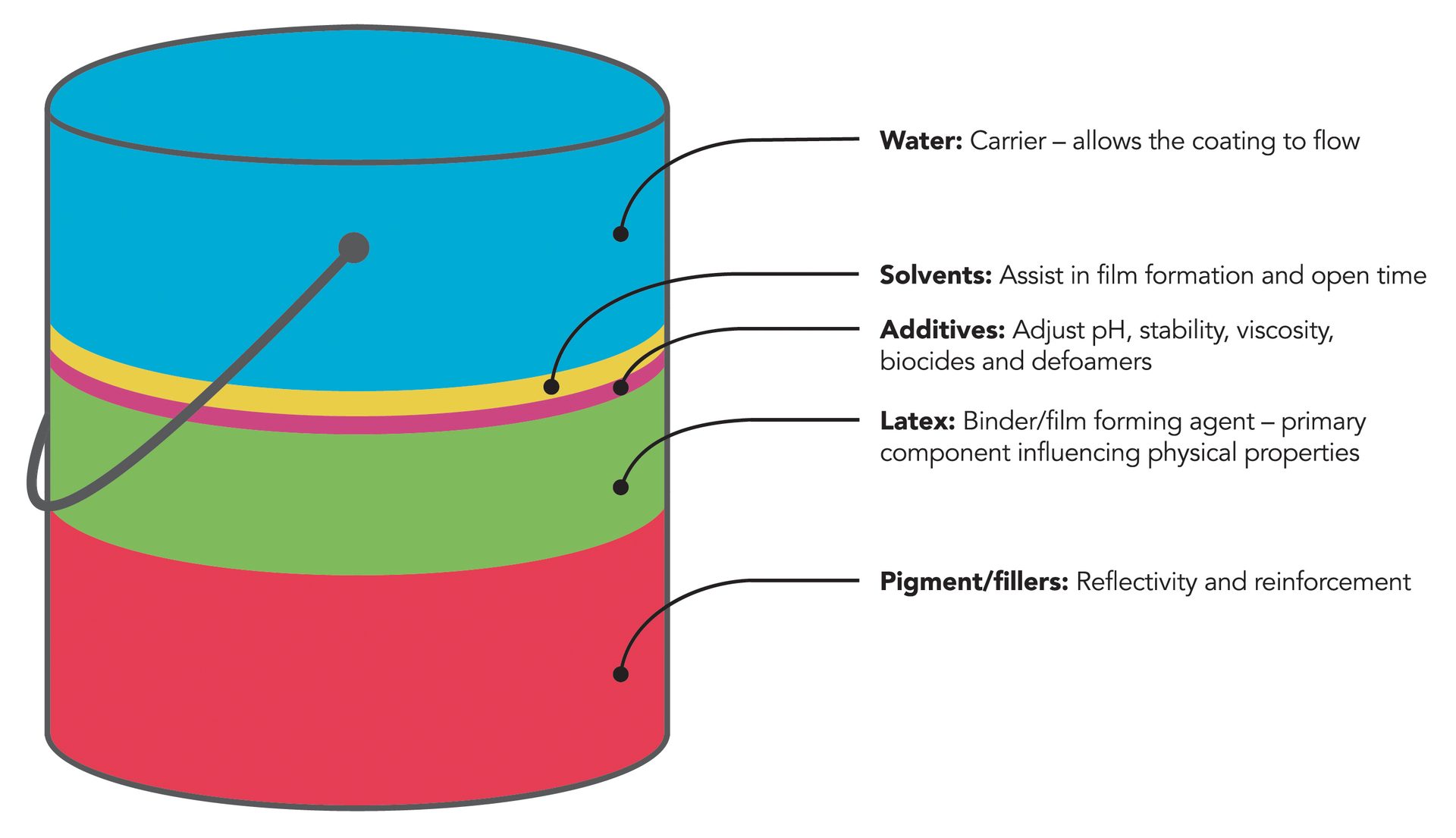
REVERSE PINCH TO ZOOM
X
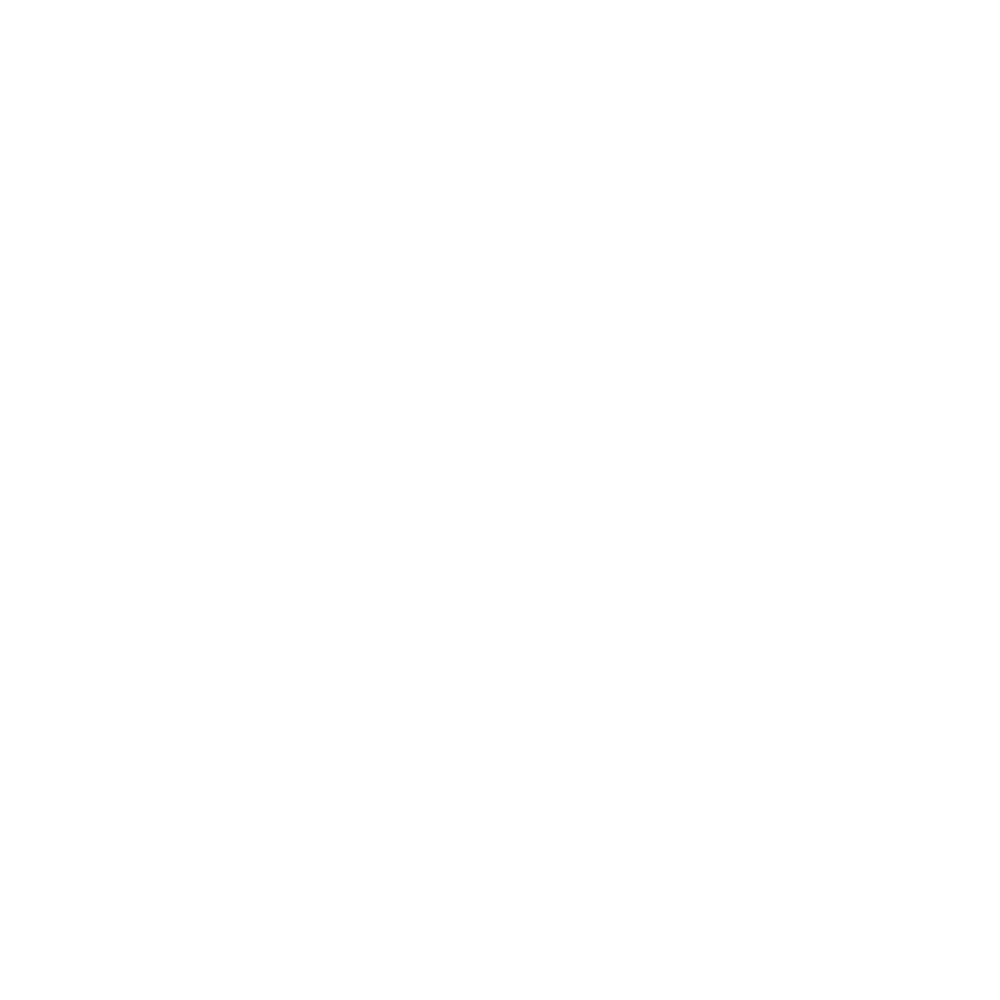
REVERSE PINCH TO ZOOM
X
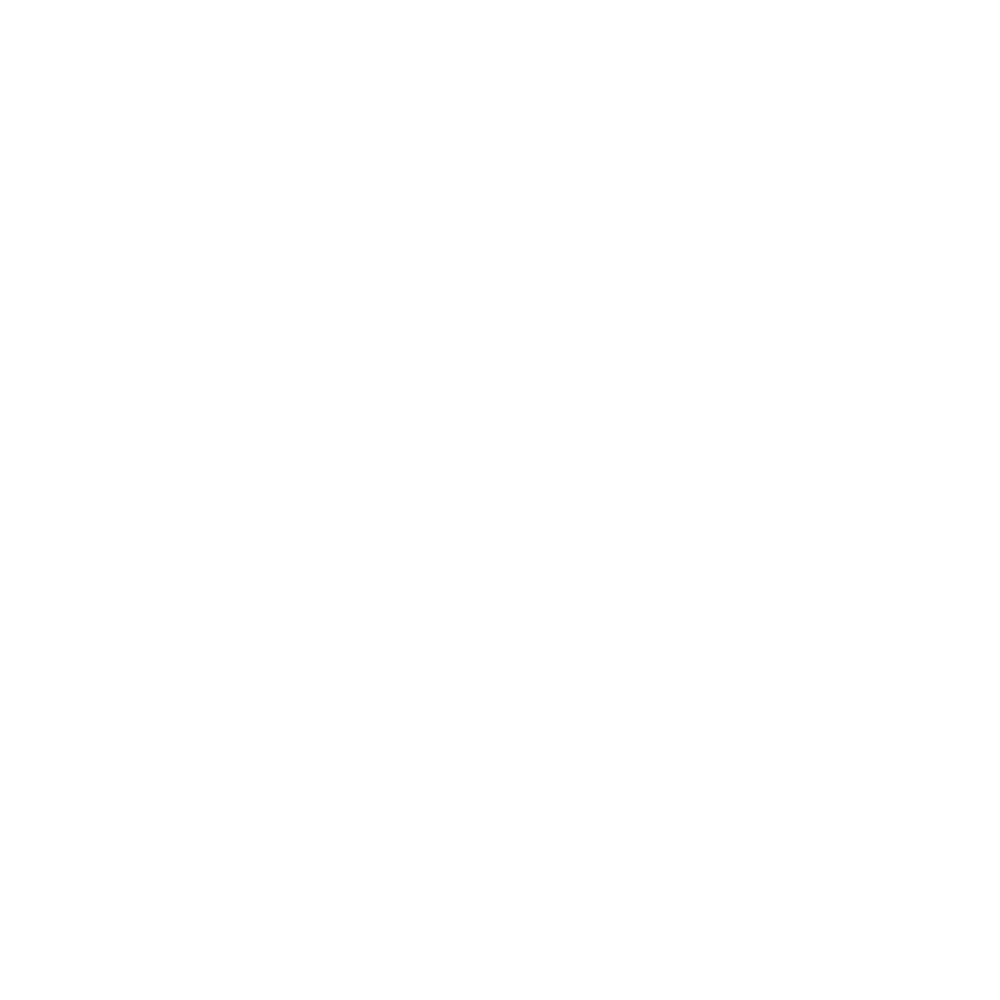
REVERSE PINCH TO ZOOM
X
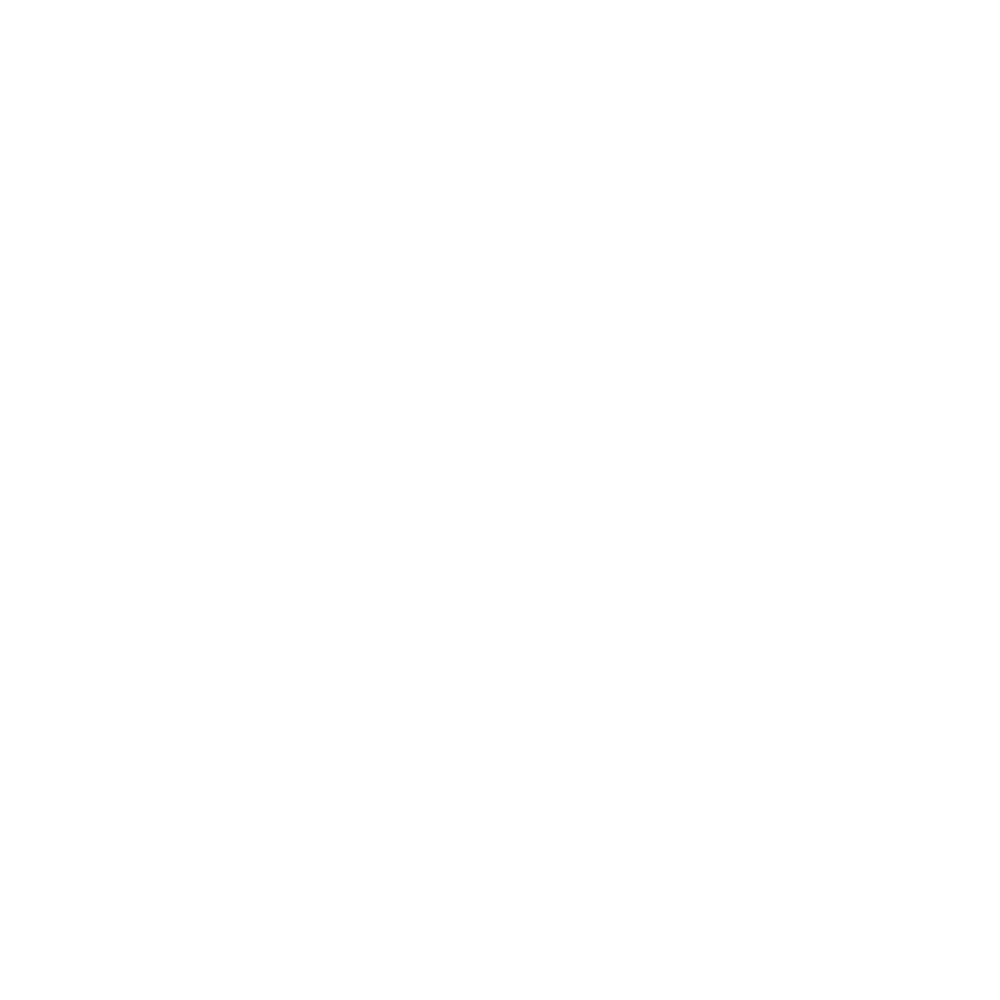
REVERSE PINCH TO ZOOM
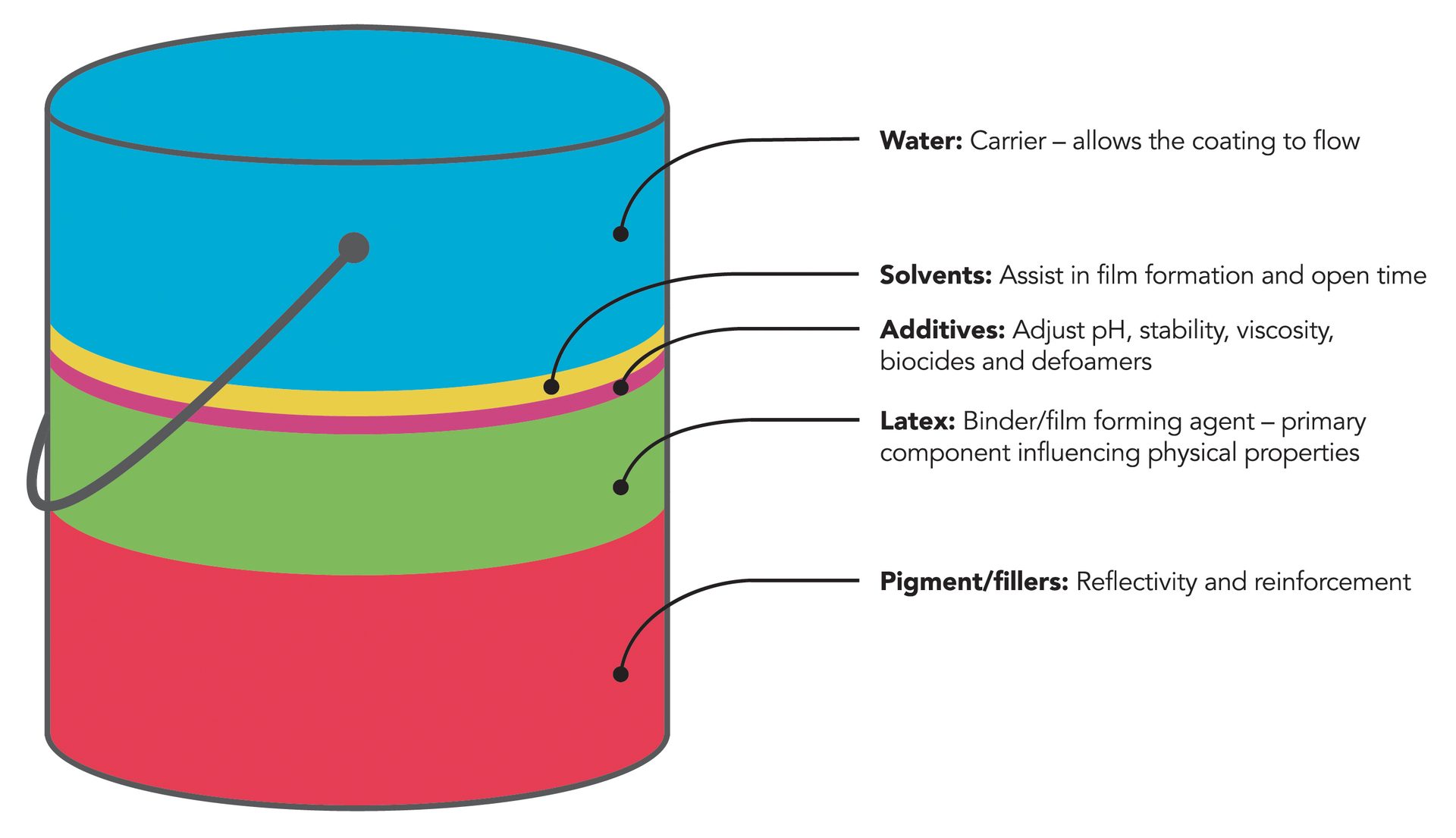
TABLE 1–ǀ–Primary components of an acrylic roof coating.
X
REVERSE PINCH TO ZOOM
X
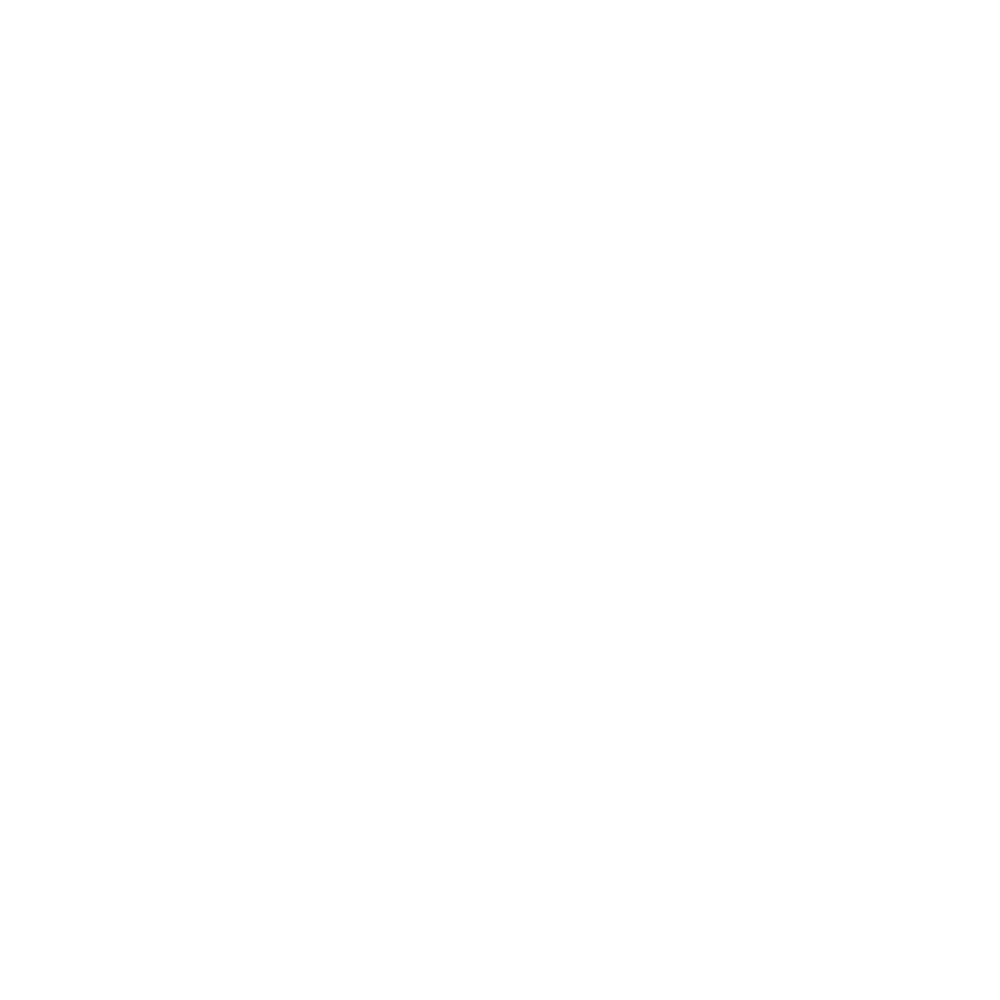
REVERSE PINCH TO ZOOM
X
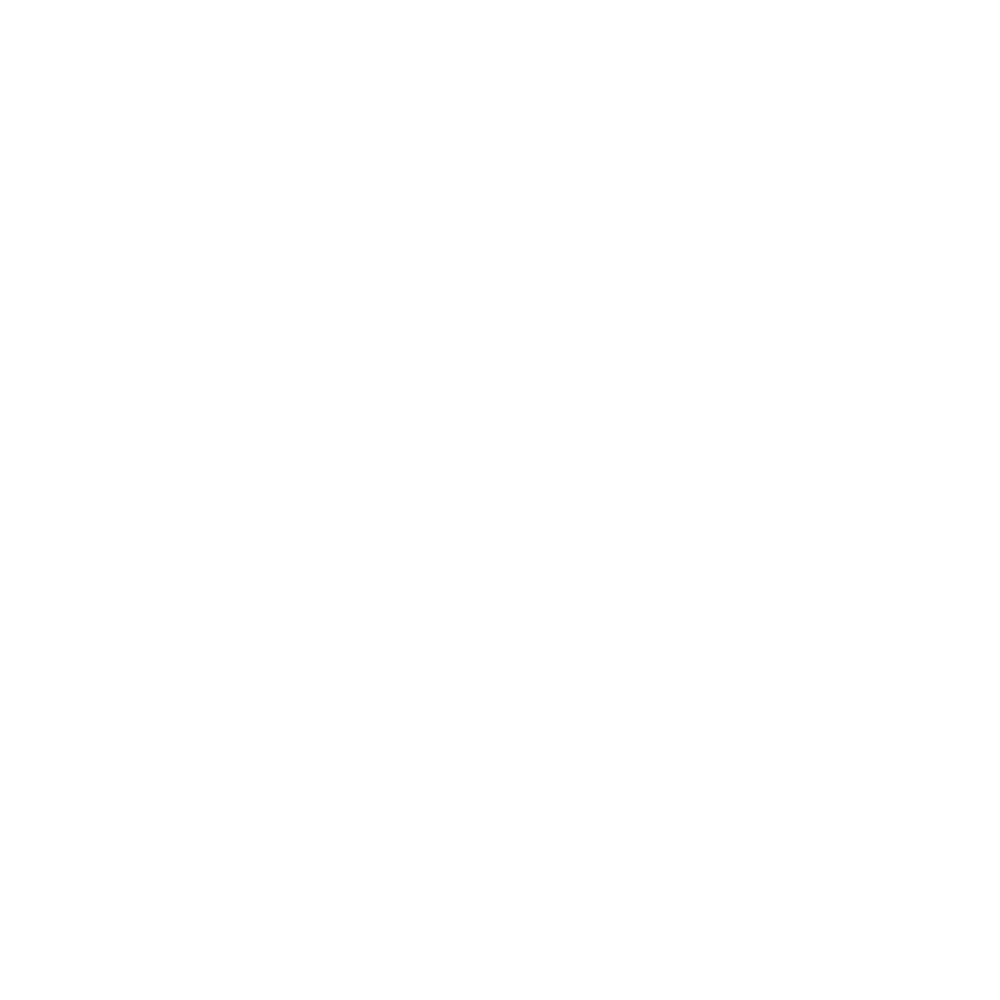
REVERSE PINCH TO ZOOM
X
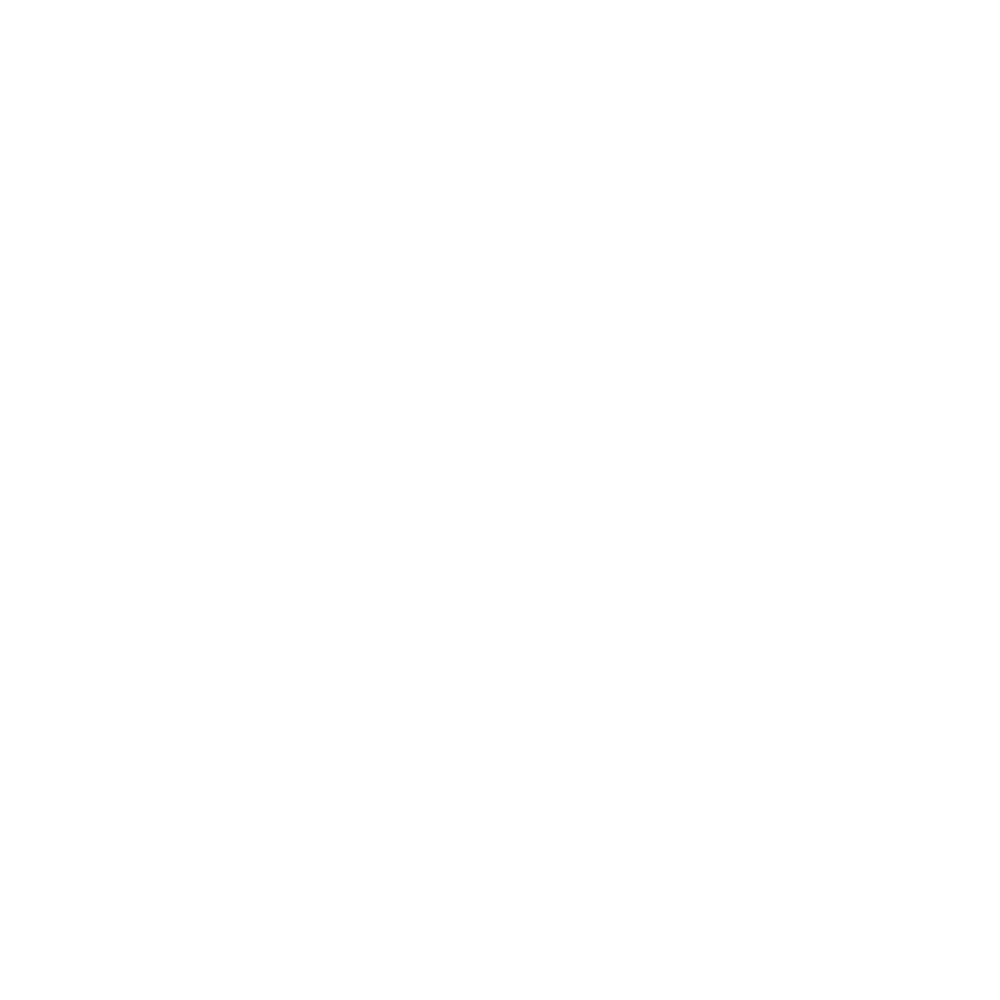
REVERSE PINCH TO ZOOM
Illustrative Test Results
Bleed-Through Resistance
The latex used is key to resisting bleed-through. Since the latex polymer forms the continuous phase surrounding the pigments and fillers, any migrating compounds must pass through it to affect the surface. There are two substrates that are particularly problematic:
- Bitumen substrates: Contain oils that migrate upward and absorb solar energy.
- PVC membranes: Contain plasticizers that soften the coating, thus potentially increasing dirt and microbial susceptibility.
In outdoor exposure tests, coatings applied to APP-modified bitumen and PVC membranes showed significant differences in performance based on the latex used. Figure 4 illustrates a comparative study of coatings made with different latexes, all formulated using the same base recipe. These coatings were applied in 6 in. × 6 in. sections onto 30 in. × 6 in. panels of three common roofing substrates: thermoplastic polyolefin (TPO), APP-modified bitumen (APP-MB) and polyvinylchloride (PVC) roofing membranes. Each panel was positioned outdoors in northern Illinois at a 5° angle to simulate real-world exposure. For reference, the left-most section of each panel (A) is a pass-control formulated with EPS® 2719, which is known to be highly resistant to bleed-through. The right-most section (E) is a fail control, containing a comparative resin known to have little resistance to bleed-through. Coatings in the center three sections (B, C, D) contain nine different experimental resins. The same coating layout was used across all three substrates to ensure consistency.
Over time, the panels were regularly evaluated for visual changes. The results clearly demonstrate the impact of substrate-specific migration on reflectivity. On the TPO panels (Panels 4–6), pass and fail controls show some differences after 38 months, but overall, the color of the panels is comparatively uniform from one section to another.
In contrast, on the APP-MB panels (Panels 13–15), several sections began to show a yellow cast within just a few days. By 13 months, discoloration was pronounced in the fail controls and most of the middle sections, and after 38 months, only EPS® 2719 and section 14D remained largely unaffected by asphalt bleed-through.
The PVC membrane panels (Panels 10–12) initially appeared uniform. By 13 months, noticeable soiling had developed on most sections, and by 38 months, only EPS® 2719 and section 12C remained relatively clean.
These findings underscore the importance of selecting the right latex for the specific substrate. Notably, the experimental latex that resisted asphalt bleed-through on bitumen (14D) was not the same as the one that best resisted plasticizer migration on PVC (12C) — highlighting the need for tailored formulation strategies.
FIGURE 4–ǀ–Images of coated panels exposed outdoors in Marengo, Illinois for 0, 13 and 38 months, illustrating the impact resin plays on bleed-through resistance and the subsequent effect on color change.
X
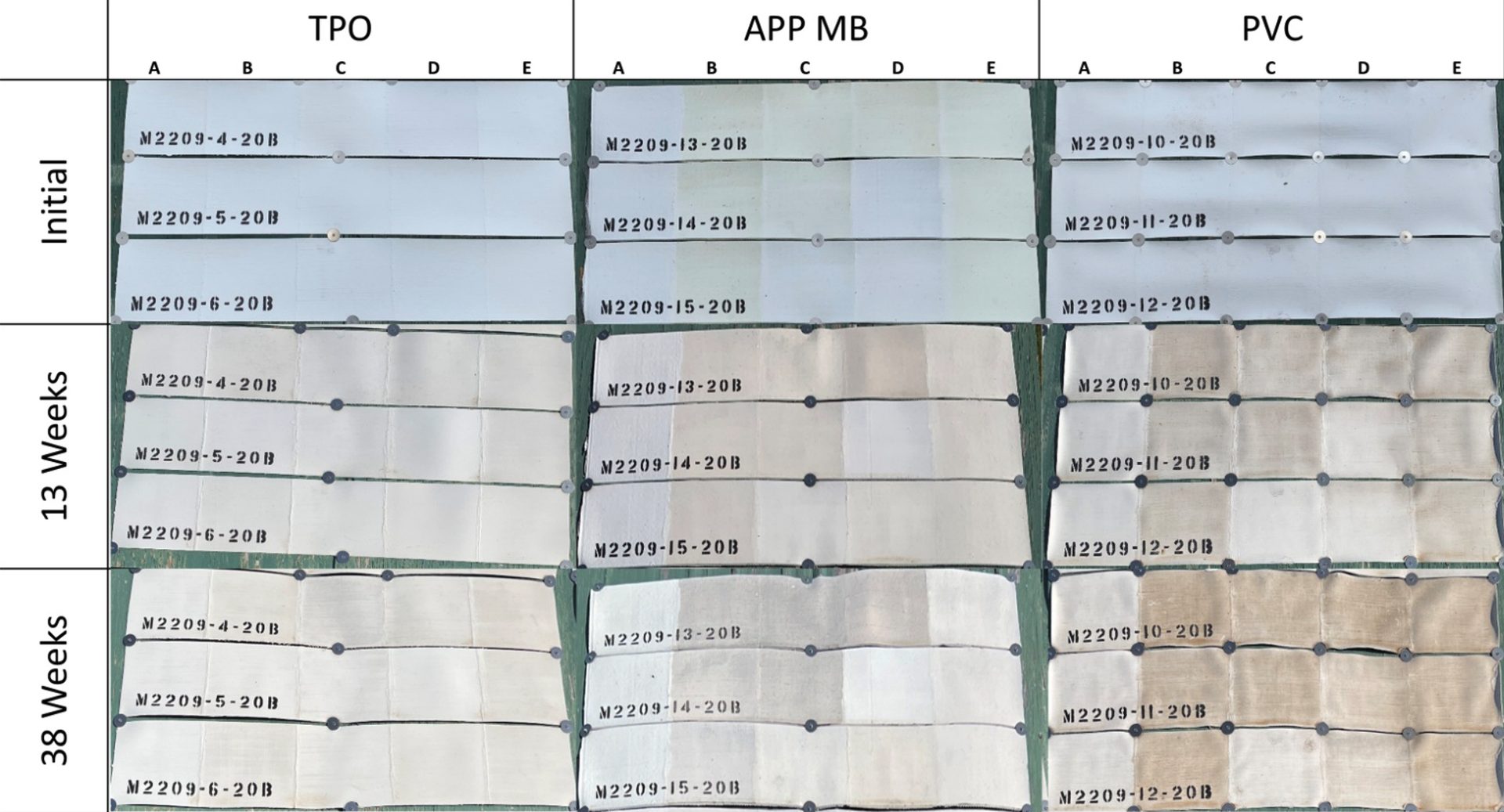
REVERSE PINCH TO ZOOM
X
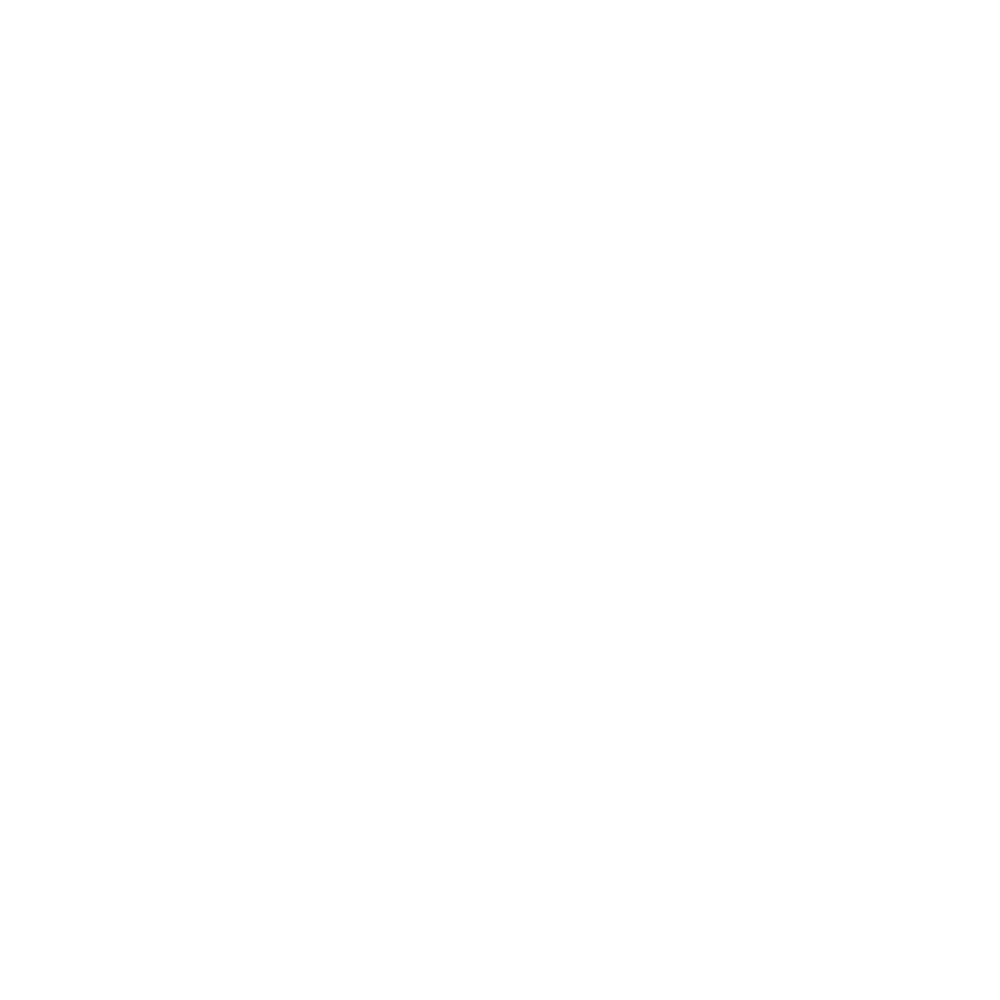
REVERSE PINCH TO ZOOM
X
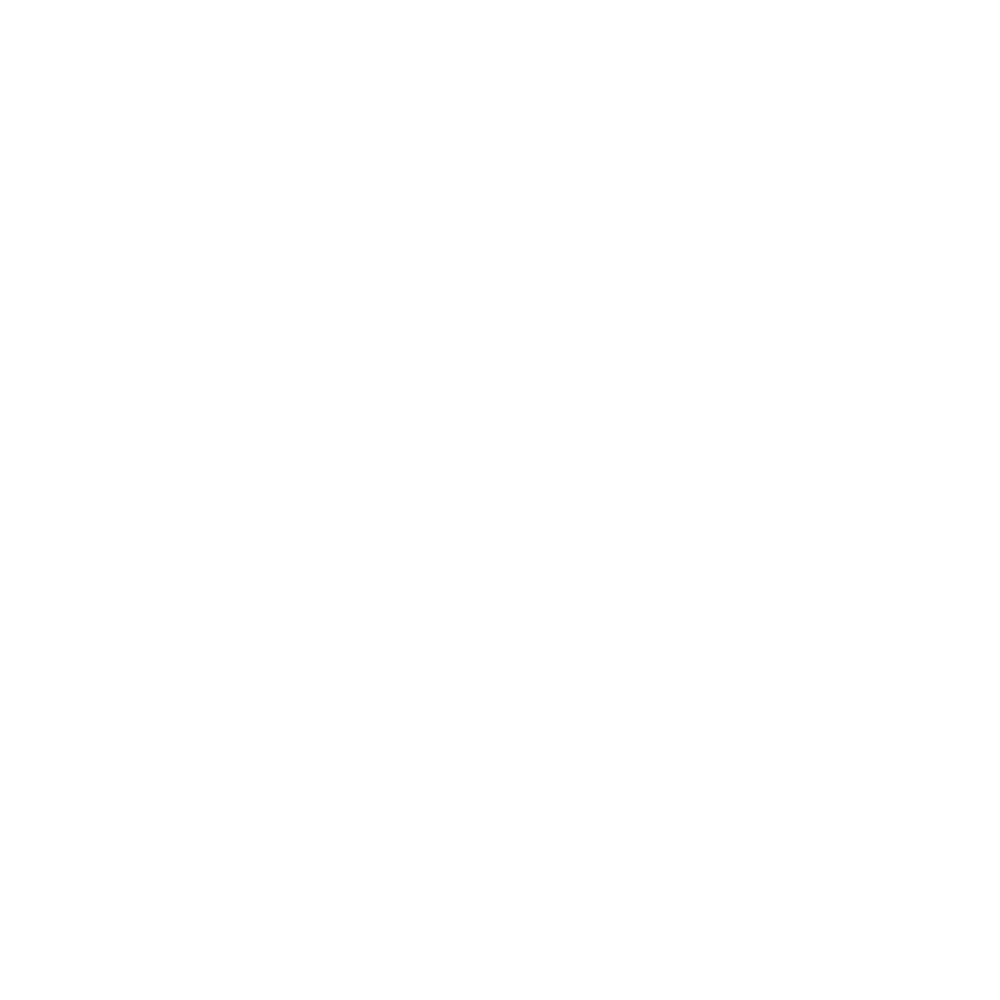
REVERSE PINCH TO ZOOM
X
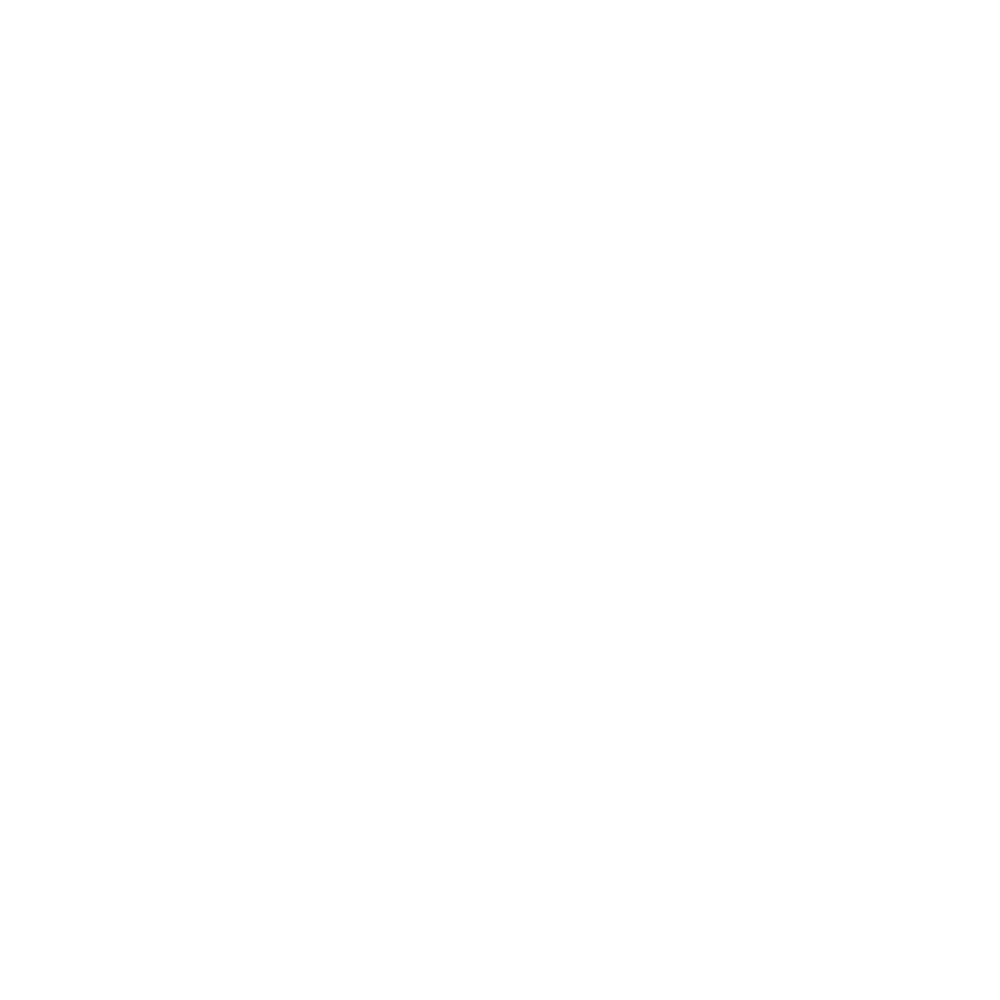
REVERSE PINCH TO ZOOM
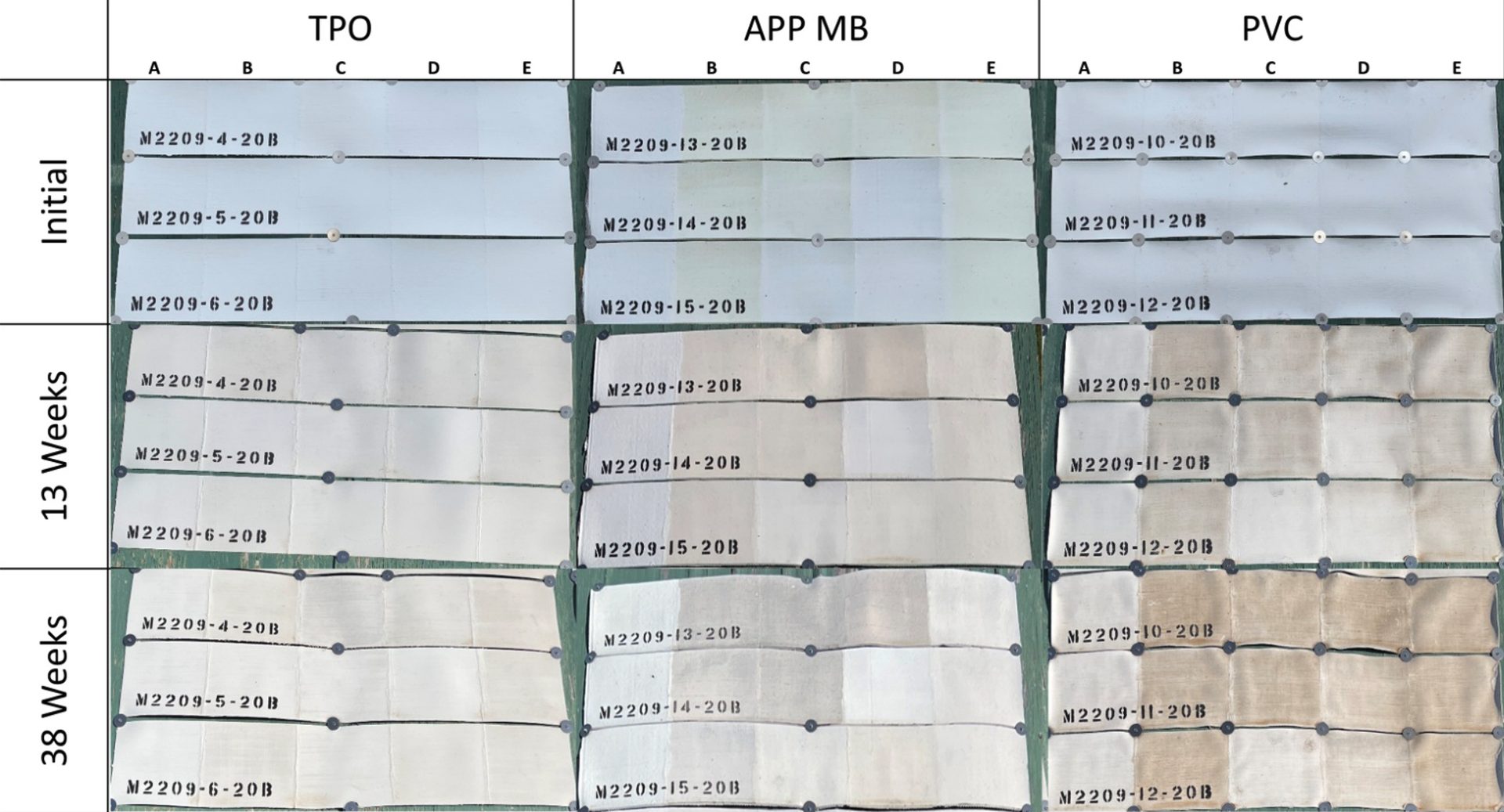
Biofouling
It’s no surprise that fungi and algae — collectively known as biofouling — can significantly reduce the reflectivity of white coatings. While dry-film preservatives are essential in regions prone to biological growth, the choice of resin also plays a major role.
Figure 5 shows the results of a long-term outdoor exposure test in Florida. Three coatings with identical formulations and preservative packages—but different latexes—showed dramatically different results after 71 months. The coating in the center, made with a comparative resin, was almost completely overgrown. The left-hand experimental coating showed moderate growth, while the coating on the right, containing EPS® 2719, remained substantially free of biological growth. This clearly demonstrates that some resins are far more resistant to biofouling than others, even when the same dry-film preservative package is used.
FIGURE 5–ǀ–Panel aged in Florida for 71 months showing vastly different degrees of biofouling based on different resins.
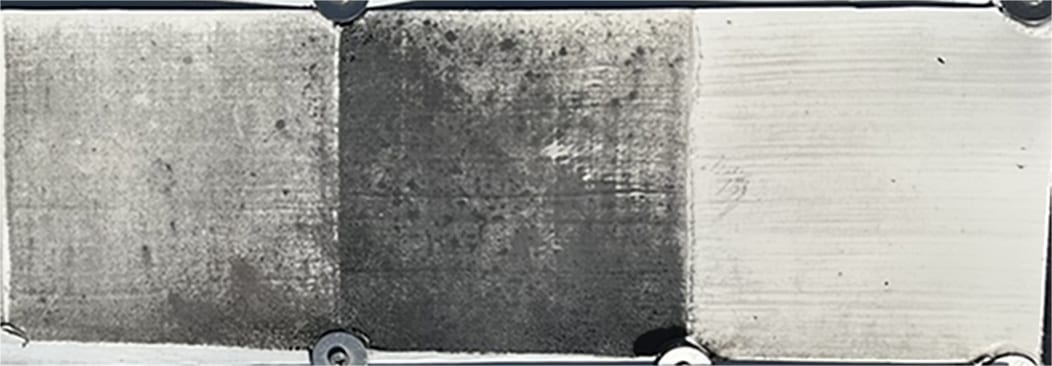
Dirt Pickup Resistance (DPUR)
Dirt pickup is perhaps the most visible and widely discussed cause of reflectivity loss. The challenge lies in the low glass transition temperature (Tg) required for flexibility in elastomeric coatings. Unfortunately, this softness can make the surface tacky — perfect for trapping airborne particles.
One common solution is to add benzophenone (BP), a photoinitiator that activates under UV light, to the coating formulation. BP works by initiating crosslinking at the surface of the coating, reducing tackiness and improving DPUR. While effective, BP has some drawbacks:
- It may trigger California Prop 65 labeling.
- It’s considered a VOC according to ASTM D6886 and must be listed on the safety data sheet (SDS).
- It’s a solid at room temperature, making it challenging to incorporate into formulations.
EPS employs a novel DPUR technology that is built directly into an acrylic latex. These resins offer improved DPUR without the added complexities of BP.
Figure 6 shows the results of a comparative test in which six coatings were applied to panels and exposed in Southern California for six months. The three sections on the left (A–C) all have a Tg of −26 °C, while the three sections on the right (D–F) have a Tg of −10 °C. The results are telling:
- Coatings with no DPUR technology (A and F) show significant dirt accumulation.
- Coatings with BP (C and D) perform better.
- Coatings made with the novel EPS DPUR-integrated latexes (B and E) showed the best performance—demonstrating that the right latex can make a big difference.
FIGURE 6–ǀ–Coated panels EPS DPUR vs. BP.
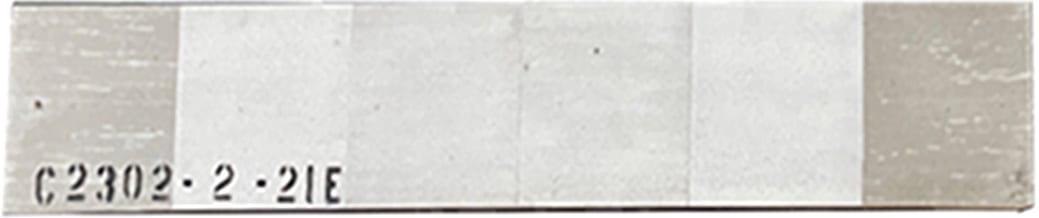
Conclusion
Among all the components in an acrylic cool roof coating, the choice of latex binder stands out as the most critical factor influencing long-term reflectivity. As the continuous phase of the coating, latex not only determines the coating’s flexibility but also plays a central role in resisting common reflectivity degradation mechanisms such as bleed-through, biofouling and dirt pickup. By choosing the right binder chemistry, manufacturers can significantly extend the reflective performance and durability of cool roof coatings — delivering coatings that not only start white but stay white.
EPS® 2210
Advanced all-acrylic emulsion for cool roof coatings designed to keep white roofs white by providing exceptional dirt pickup resistance and asphalt bleed-through resistance.
EPS® 2719
All-acrylic emulsion designed to minimize asphalt bleed-through in cool roof coatings while maintaining flexibility and toughness.
EPS® 2252
High solids acrylic emulsion designed to adhere to low-energy substrates commonly used in roofing like TPO and EPDM.
RayFlex® 765
Styrenated acrylic emulsion designed for flexible roof coatings, textured finishes and wall mastics. It offers excellent elongation and tensile strength, low-temperature flexibility and water resistance.
Learn more here.
About the Author
Dr. Brent Crenshaw is a research and development senior scientist at EPS, where he has led R&D projects in multiple segments of the construction market for the past 14 years and has gained recognition as an industry specialist in roof coatings. Dr. Crenshaw holds a bachelor's degree in chemical engineering from Brigham Young University and a Ph.D. in macromolecular science and engineering from Case Western Reserve University. Dr. Crenshaw is actively engaged in the RCMA – Roof Coatings Manufacturers Association as well as ASTM.
References
1 Cool Roof Rating Council. CRRC Rated Roof Products Directory. Accessed May 29, 2025.