The Innovation Ecosystem:
How Collaboration Fuels Coatings Advancements
Why the Next Wave of Coatings Technology
Depends on Full Value Chain Collaboration
The Innovation Ecosystem:
How Collaboration Fuels Coatings Advancements
Why the Next Wave
of Coatings Technology
Depends on Full Value
Chain Collaboration
–Credit: Oleksii Lishchyshyn / Creatas Video+ via Getty Images Plus–
By Juliane Hefel, Senior Vice President, Industrial Coatings and Specialty Products, PPG
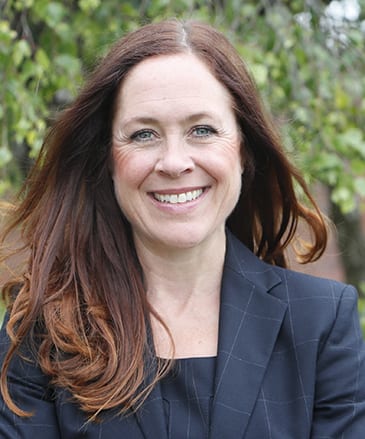
Juliane hefel
Coatings and specialty products manufacturers face a rapidly changing market. New manufacturing technologies, shorter lead time expectations and sustainability goals are affecting the way coatings and other solutions are formulated and produced. To remain competitive globally and deliver solutions that meet customer needs, collaboration throughout the value chain is essential. By working together, industry players can serve as incubators for innovative products, business models and sustainable practices.
Innovation thrives in an ecosystem where insights, technologies and best practices are shared. It is paramount to break down information silos that can impede product development and market adoption. Strategic partnerships enable suppliers and fabricators to go beyond traditional product development pipelines and develop transformative technologies that will shape the future of the industry.
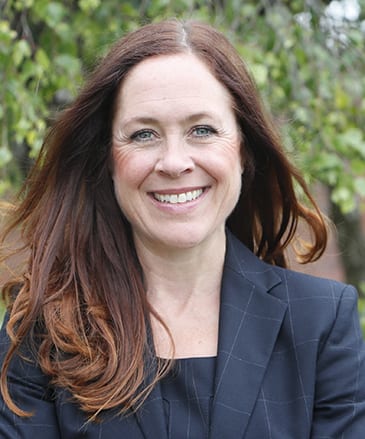
Juliane Hefel
Connecting manufacturers and customers helps teams share information and optimize processes, ultimately leading to more effective R&D efforts and accelerated commercialization. These types of collaborative relationships are not without their challenges — every successful partnership must be able to weather some constructive friction during the building process — but the payoff is worth it. Bringing teams together to share risks and learn from collective trials and failures will enable the next generation of technological advancements that will change how coatings are manufactured, applied and utilized.
Leverage Data and Automation
The rise of digitization and big data in manufacturing is revolutionizing traditional product development processes. Data collection efforts support demand forecasting, inventory optimization and customization at scale, increasing competitiveness in a fast-evolving market. By sharing data on equipment capabilities and manufacturing constraints, companies can better leverage data to predict performance via virtual simulations, reduce physical trials and product iterations, and bring products to market with greater speed and efficiency.
This type of early-stage collaboration supports process optimization, leading to enhanced operational productivity and opportunities for automation. PPG, as a paint and coatings manufacturer, is investing significant resources into streamlining the color matching process for customers. At the PPG Springdale Plant in Pennsylvania, coatings are developed using customer input about where and how the products will be applied, allowing for more accurate formulations early in the process. Samples are prepared using automated machinery, saving time and energy, and helping customers receive their perfect paint matches as quickly as possible.
By sharing data on equipment capabilities and manufacturing constraints, companies can better leverage data to predict performance via virtual simulations, reduce physical trials and product iterations, and bring products to market with greater speed and efficiency.
Enhance Speed to Market
Collaboration also positions companies to capitalize on growth opportunities in a dynamic market. With new technologies emerging every day, speed is the new superpower. Being first to market can be a key differentiator for coatings manufacturers. By involving customers and fabricators in product development, manufacturers can help streamline feasibility analysis and testing phases, and enable a faster time to market for new products.
Technical support from material suppliers assists manufacturers in integrating new products seamlessly into their operations. PPG partnered with a home appliance manufacturer to lead process design workshops to help the company’s coating operations adopt the latest powder coating technologies quickly and efficiently while reducing energy consumption. Suppliers can also conduct facility audits, provide training sessions and recommend process improvements that enhance energy efficiency, quality and productivity.
Evaluate the Total Cost of Ownership
A holistic approach to product development that considers the needs and capabilities of manufacturers and customers results in leaner, more resilient operations that benefit all parties. By addressing the total cost of ownership — not only the cost per unit of a product — partner organizations can help each other spot inefficiencies throughout the development and production processes and utilize resources effectively.
Coordinated efforts across the value chain also help businesses integrate sustainable practices into their operations more effectively. By aligning with global frameworks like the U.N. Sustainable Development Goals (SDGs) and the Science Based Targets initiative (SBTi), companies speak “one language” to work together to reduce direct and indirect greenhouse gas emissions. PPG’s development of energy-curable coatings for metal coils helps manufacturers eliminate the need for thermal ovens, using ultraviolet (UV) or electron beam (EB) coating technologies that cure materials at room temperature. This results in significant energy savings while also increasing productivity through rapid curing.
By addressing the total cost of ownership — not only the cost per unit of a product — partner organizations can help each other spot inefficiencies throughout the development and production processes and utilize resources effectively.
Think Outside the Process
A well-developed new product introduction (NPI) process is a critical part of every business, but the emergence of new technologies and the proliferation of startups can make innovation difficult within these established frameworks. The expansion of extended reality (XR) devices is an excellent example of a developing market. To manufacture wearable devices that are compatible with augmented reality (AR) software, lenses, projectors and processors are all being used in completely new ways. Companies that are open to collaboration are finding effective ways to combine technologies to create something new, like adapting 3D manufacturing to lens coating processes and embedding electronics into lens materials.
Industry shifts require agility in how companies work with suppliers and customers. In order to take advantage of new developments, the R&D process may look different than the traditional NPI process. Working with startups and developing technologies requires the flexibility to focus on the long-term potential of innovation without the same ROI milestones used in the past. By accepting a different way of measuring progress, teams can work together with the freedom to explore technologies and applications that have the power to not just improve a product, but revolutionize the market. Developing flexible approaches to product development and manufacturing contributes to the resilience of the coatings industry as a whole.
Companies that are open to collaboration are finding effective ways to combine technologies to create something new, like adapting 3D manufacturing to lens coating processes and embedding electronics into lens materials.
Fail Fast to Make It Happen
We all know that collaboration is important. But how can companies build relationships and make these types of successful partnerships a reality? The bottom line is that companies need to be willing to accept joint risks. While the specific outcomes may be uncertain, long-term collaboration and value chain integration fuel continuous improvement, benefiting both new product development and the refinement of existing technologies. It is also critical to fail fast. Partners must take risks and invest in new technologies, but also realize when a project cannot move forward and pivot.
The opportunity to drive product breakthroughs with full value chain collaboration is incredibly promising. When companies involve partners early, they unlock the potential to create better solutions, optimize processes and discover new commercial options for evolving markets. The combination of sustainable innovations and close partnerships with customers positions companies to make significant strides in efficiency and environmental impact and support overall industry growth. By leveraging collaboration as a strategic advantage, coatings manufacturers can lead the development and implementation of disruptive technologies that will expand the capabilities of coatings performance.
Not every player in the value chain will be ready to embark on this journey, but those who are will be looking at a promising future. I am excited to help this industry transform.