Industrial Paint and Coatings 101
Exploring Alkyd Resins
Industrial Paint
and Coatings 101
Exploring Alkyd Resins
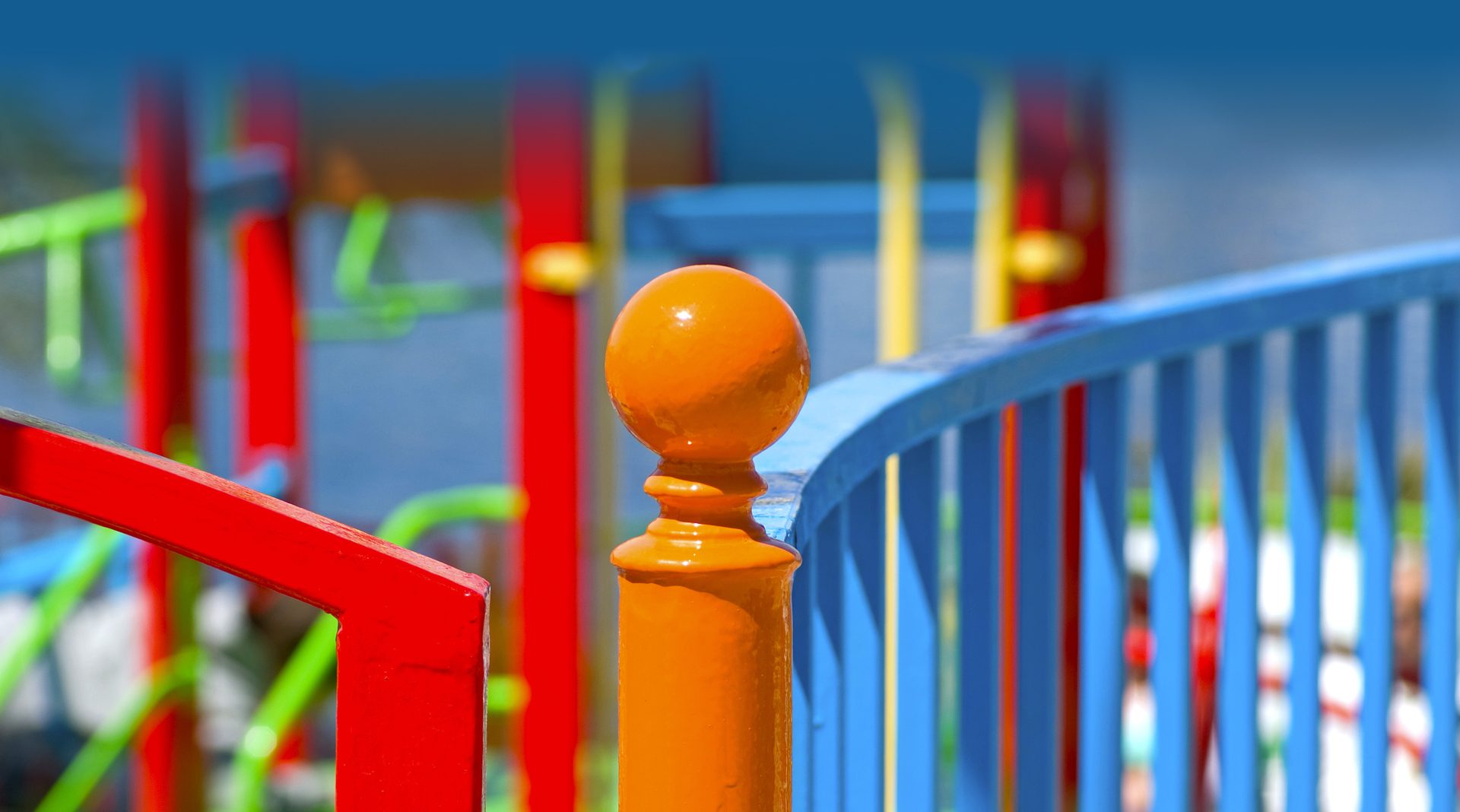
Credit: annalovisa / iStock via Getty Images Plus
By Sheboygan Paint Company
Alkyds are a type of synthetic resin commonly used in industrial coatings. They are favored for:
- Versatility: They can be formulated for a wide range of applications, from protective coatings to decorative finishes.
- Durability: Alkyd coatings are known for their resistance to wear, weather and chemical exposure.
- Gloss and Color Retention: They typically provide a smooth, glossy finish that maintains color over time.
- Ease of Application: Alkyd-based coatings can be applied using various methods, including spraying, brushing or rolling.
- Cost-Effectiveness: Generally, alkyds are more affordable than some other resin types, making them a popular choice in industrial settings.
While they offer many benefits, alkyd coatings can also have some limitations, such as longer drying times compared to other formulations and potential yellowing over time. Although chemical resistance and gloss retention of alkyds are good, they cannot match that of alternative chemistries such as urethanes. Cost savings from using alkyds versus alternative coatings are significant, which makes alkyds very favorable for industrial use. The widespread use of alkyds in industries like transportation, marine and general manufacturing highlights their effectiveness in protective and aesthetic applications.
Alkyds are a type of synthetic resin commonly used in industrial coatings. They are favored for versatility, durability, gloss and color retention, ease of application and cost-effectiveness.
The Chemistry
Alkyd resins are classified as thermoplastic polyesters synthesized via polycondensation reaction with polyhydric alcohol, polybasic acids or anhydrides, and fatty acids or triglyceride oils. They cure by both physical drying, where the solvent evaporates, and chemical curing. The chemical process, termed “autoxidative cure,” occurs when oxygen from the atmosphere reacts with the double bonds in drying oils to form cross-linking through radical reactions that increase the stiffness of the film at normal temperatures.
Metal drier compounds, such as cobalt, manganese, zirconium and others, have traditionally been used throughout the coatings industry to enhance the cure speed of alkyd coatings. Our Sheboygan Paint Company labs are actively testing new drier products developed by our suppliers to replace cobalt, which would offer safer and more sustainable alternatives for the environment.
The “oil length,” or percentage of oil to resin in the coating formula, can be adjusted in alkyds to influence the properties of the final product. Here’s how:
- Drying Time: Longer oil lengths (more oil) generally result in slower drying times, which can be beneficial for certain applications where workability is essential.
- Film Properties: Oil length affects the hardness and flexibility of the dried film. Short-oil alkyds (less oil) tend to be harder and more rigid, while long-oil alkyds provide increased flexibility and toughness.
- Gloss and Appearance: The oil length can influence the gloss level of the coating. Longer oil lengths typically yield a glossier finish, which can enhance aesthetic appeal.
- Chemical Resistance: Variations in oil length can affect the coating’s resistance to chemicals and environmental factors, which can be critical in certain industrial applications.
- Adhesion: The oil length can also influence how well the coating adheres to substrates, impacting durability and performance.
- Application Properties: Oil length can affect viscosity, making it easier or more challenging to apply depending on the desired application method.
Our Sheboygan Paint Company labs are actively testing new drier products developed by our suppliers to replace cobalt, which would offer safer and more sustainable alternatives for the environment.
While the amount of oil used in an alkyd resin dictates performance characteristics, so does the type of oil used. Here are some of the common oils used in alkyd resin production:
- Drying Oils: Oils that harden into a tough, solid film through the oxidation process. Drying oils consist of glycerol triesters of fatty acids and are characterized by high levels of polyunsaturated fatty acids. Key components for many coatings and some varnishes, drying oils are being replaced more and more frequently by various alkyd resins.
- Tung Oil: Also known as China wood oil, tung oil is a drying oil that is obtained by pressing the seed from the nut of the tung tree. This type of oil has been used since around the year 400 BC and is typically used on various wood products. After curing, this oil produces a very hard and easily repaired finish. Tung oil is also popular since it resists water better than any other pure oil finish.
- Linseed Oil: Linseed oil, also known as flaxseed oil, is obtained from the dried, ripened seeds of the flax plant via a pressing process. It is often combined with other oils, resins and solvents, and is typically used in varnishes for wood coatings. Throughout the years, linseed oil has also been used as a plasticizer and hardener in putty and in the manufacturing of linoleum. As with tung oil, the use of linseed oil has declined over the years due to the increased use of synthetic alkyd resins.
Other natural oils used in the production of alkyd resins include soybean oil, safflower oil, sunflower oil, tall oil, castor oil and palm oil. Each type of oil contributes different properties to the final product.
The Result
By carefully adjusting oil type and length, formulators can tailor alkyd resins to meet specific performance and application requirements. For more information, click here.